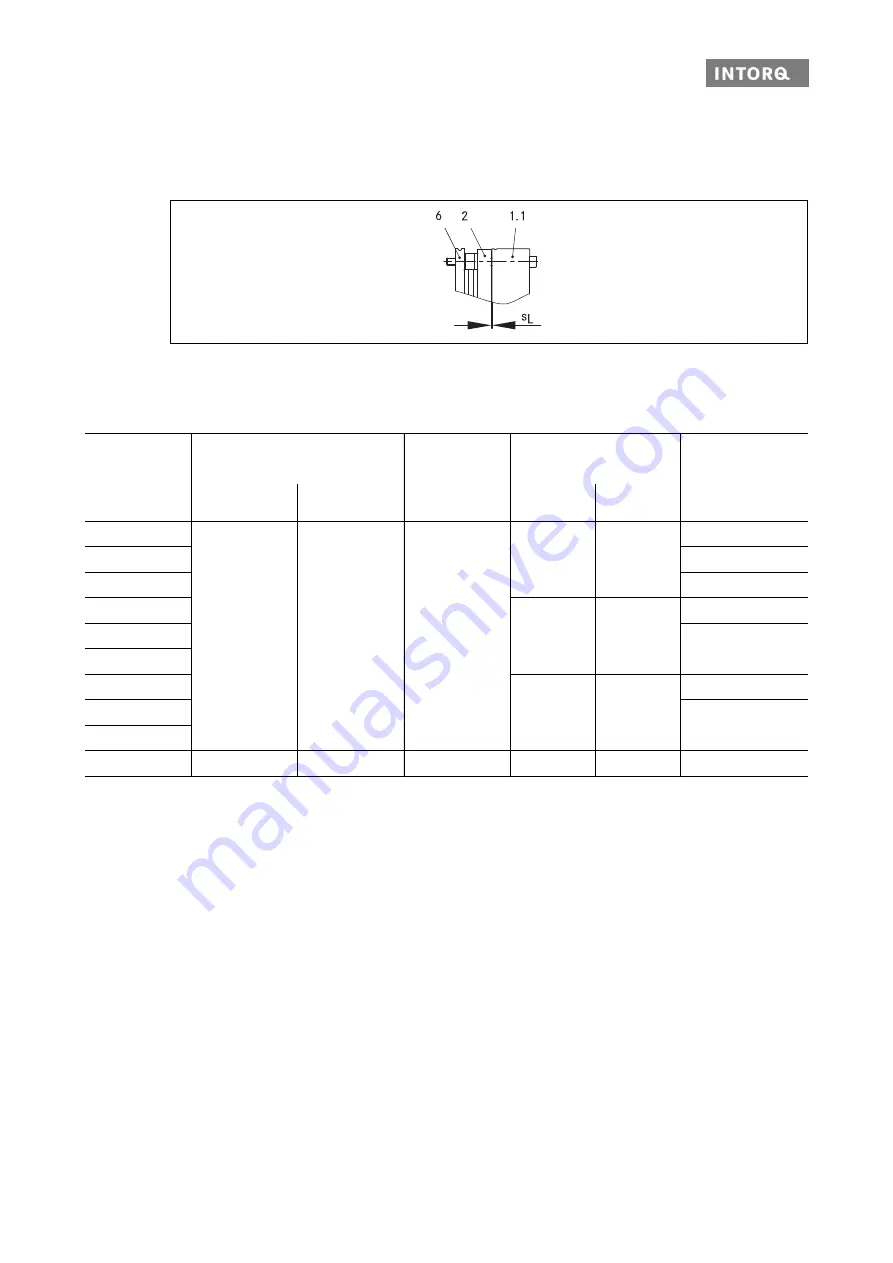
Technical specifications
INTORQ | BA 14.0197 | 04/2016
16
3.2
Rated data
3.2.1
Dimensions
1.1 Stator, complete
2
Armature plate
6
Flange
Type
Air gap
Perm. wear
Rotor thickness
Stator weight
complete
s
LN
+0.05
[mm]
s
Lmax
[mm]
[mm]
min. [mm] max. [mm]
m [kg]
BFK464-17
S
0.4
0.6
0.2
12.7
13
12
BFK464-18
S
15
BFK464-18
S.2
14.5
BFK464-19
S
15.7
16
18.8
BFK464-20
S
22
BFK464-20
S.1
BFK464-22
S
19.7
20
24
BFK464-25
S
42
BFK464-25
S.1
BFK464-28
S
0.5
0.8
0.3
17.6
18
46
Summary of Contents for WSG-TB.3 series
Page 29: ......
Page 30: ......
Page 31: ......
Page 33: ......
Page 37: ......
Page 38: ......
Page 39: ......
Page 43: ......
Page 44: ......
Page 45: ......
Page 46: ......
Page 47: ......
Page 95: ...Notes INTORQ BA 14 0197 04 2016 48 Notes...
Page 144: ...Notes INTORQ BA 14 0210 12 2016 48 Notes...
Page 145: ...Notes INTORQ BA 14 0210 12 2016 49...
Page 146: ...Notes INTORQ BA 14 0210 12 2016 50...
Page 147: ......