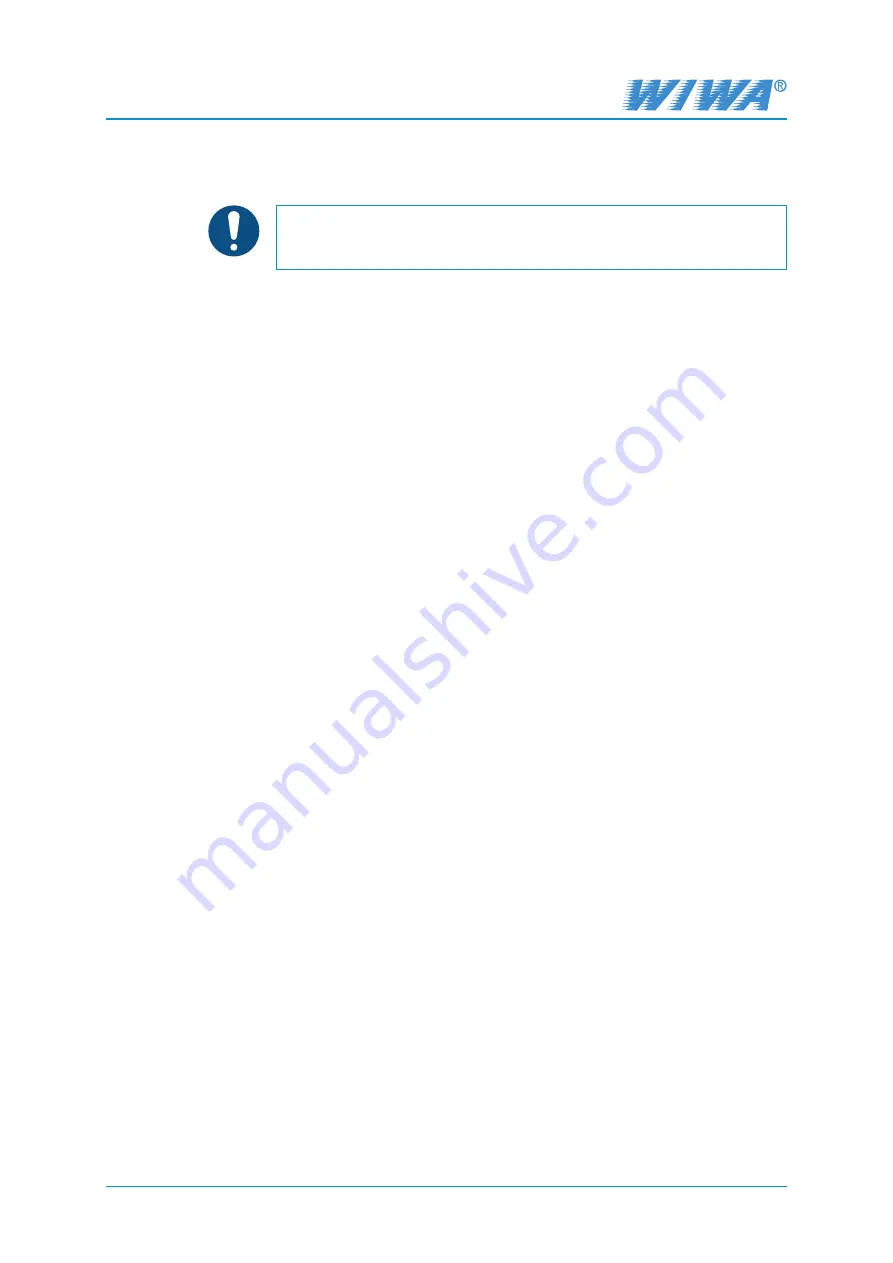
36
Original operation manual
AIRCOMBI
AirCombi_BAoDB_en_1701 • rs
Operation
5.8 Disposal
It is necessary to collect residues of spray material, cleaning fluids, oil,
greases and other chemical substances according to the legal regulations
for recycling or disposal. The official local waste water protection laws apply.
At the end of the machine's use it must be put out of use, disassembled and
disposed of according to the legal regulations.
➤
Thoroughly clean the machine of material residues.
➤
Disassemble the machine and separate the materials – metals must
be taken to a scrap metal depot, plastic parts can be disposed of with
household waste.