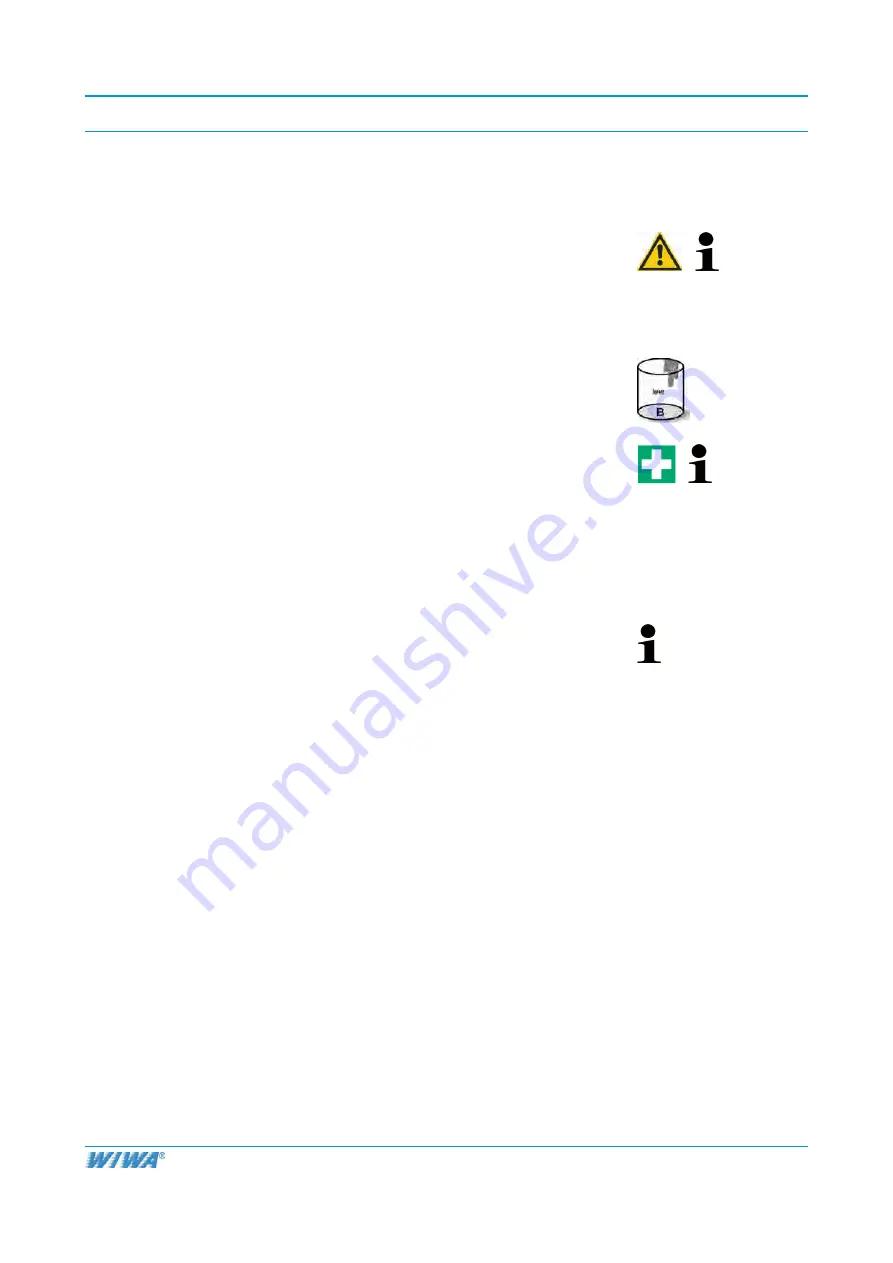
Safety
2
Translation of the original operation manual
13
13
•303_208176_1004_en•ski
2.6
Behavior in case of emergency
Leaks
If leaks occur in the system, it must be shut down
immediately
and the entire system
has to be depressurized:
➤
Interrupt the compressed air supply with the main tap lock and the pressure regulator.
➤
Make sure the whole unit is fully depressurized (the material circulate is opened and
the spray gun* has been triggered).
➤
Open the spray gun* and direct it into an open empty container. Take care to keep
the gun in contact with the container.
➤
Damaged parts must be replaced immediately.
Injury
➤
Should an injury occur through contact with liquid spray, we recommend a doctor be
called immediately.
➤
Inform the doctor of the material sprayed (e.g. paint) and the solvent (thinner). Have
the product data sheet at hand (address and telephone number of supplier or manu-
facturer, name of material and material number).
➤
Memorize the local emergency phone numbers.
➤
In any case, become familiar with the first-aid measures.
Fires
➤
Read the instructions for fire alarm and escape routes put up in your factory.
➤
Do not apply any other extinguishing agents than those which are prescribed by the
manufacturer of the materials.