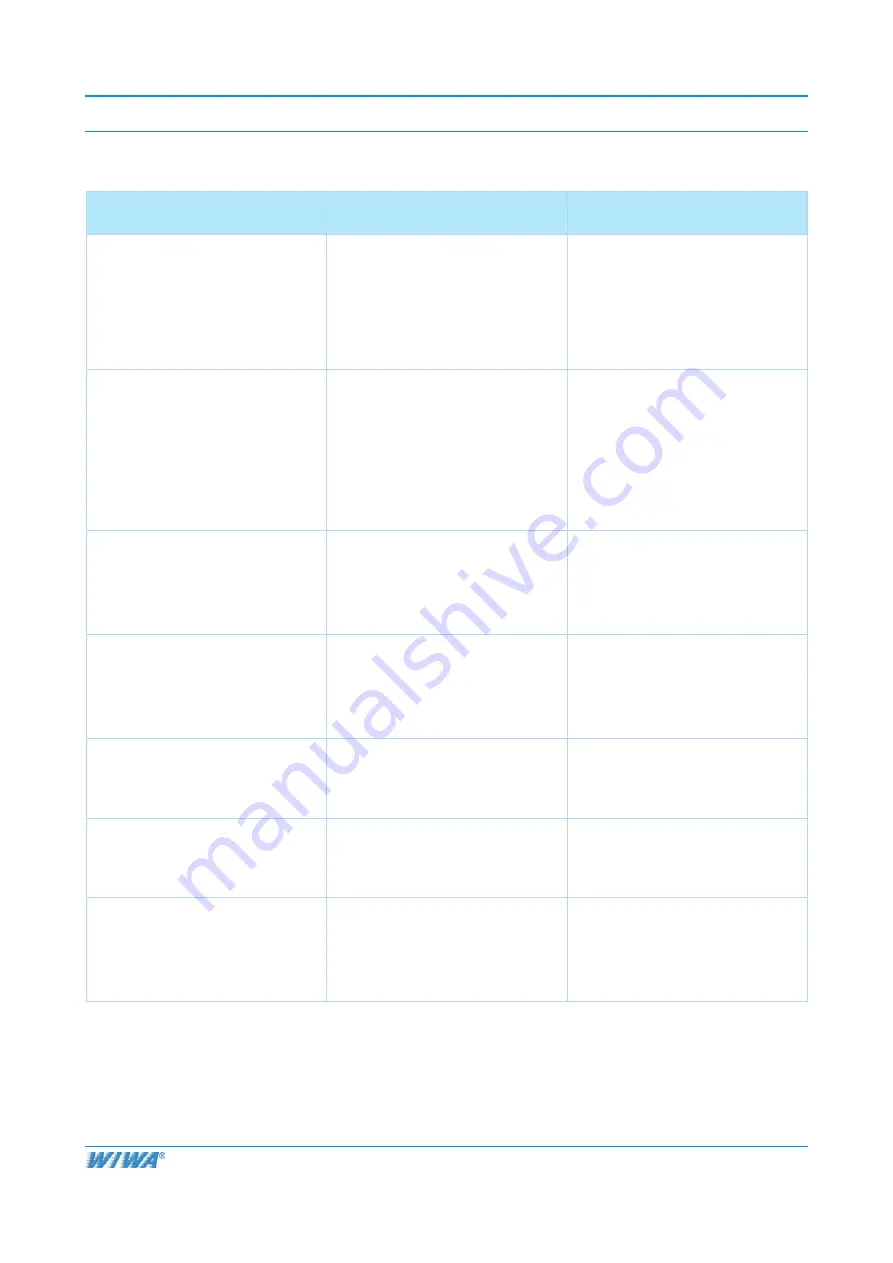
Disturbances during operation and trouble-shooting
9
Translation of the original operation manual
45
45
•303_208176_1004_en•ski
Faults
Probable Causes
Remedies
8. Pressure of hardener and base
is considerably higher on the
upstroke than on the downstroke.
Feed hose bloats or safety valve
at the outlet manifold opens and
the material is delivered back to
the container through the return
hose.
➤
One of the bottom valves of the
base material pumps is defective.
➤
Check and clean both bottom
valves.
➤
Replace defective balls and valve
plates.
9. No pressure is built up on the
base side when cycling up and
down.
Pressure at the hardener side is
high.
➤
No material is delivered to the
base material pump
➤
Rupture disk at the high pressure
filter defect.
➤
Drain valve of base material is
leaking.
➤
Ball valve at material inlet is
closed.
➤
Check material supply.
➤
Check rupture disk of the base at
high pressure filter.
➤
Check drain valve of base for
proper function.
➤
Open ball valve.
10. When circulating, pressure of
base remains.
➤
Drain valve of base does not
open.
➤
Return hoses are clogged.
➤
High pressure filter insert is
clogged.
➤
Check drain valve.
➤
Check whether return hoses are
clogged.
➤
Clean high pressure filter.
11. When draining, pressure of hard-
ener remains.
Pressure of base drops.
➤
Drain valve of hardener does not
open.
➤
Return hoses are clogged.
➤
High pressure filter insert is
clogged.
➤
Check drain valve.
➤
Check whether return hoses are
clogged.
➤
Clean high pressure filter.
12. When spraying, pressure of base
increases continuously compared
to the pressure of the hardener
pump.
➤
High pressure filter insert of base
is becoming clogged.
➤
Packings of hardener pump start-
ing to leak.
➤
Clean filter insert of high pressure
filter, or replace by a coarser one.
➤
Repair hardener pump (change
packings).
13. When spraying, pressure of
hardener increases continuously
compared to the pressure of the
base pump.
➤
High pressure filter insert of hard-
ener is becoming clogged.
➤
Packings of base pump are start-
ing to leak.
➤
Clean filter insert of high pressure
filter, or replace by a coarser one.
➤
Repair base pump (change pack-
ings).
14. When spraying, there is not suf-
ficient pressure or paint at the
gun, although the pressure at the
equipment is high.
➤
Filter inserts are clogged.
➤
Mixing block, static mixer, paint
hose or spray gun* are clogged.
➤
Tip of gun is clogged.
➤
Clean filter insert of high pressure
filter, or replace by a coarser one.
➤
Clean or replace the mixing block,
static mixer, paint hoses and gun.
➤
Replace tip of gun.