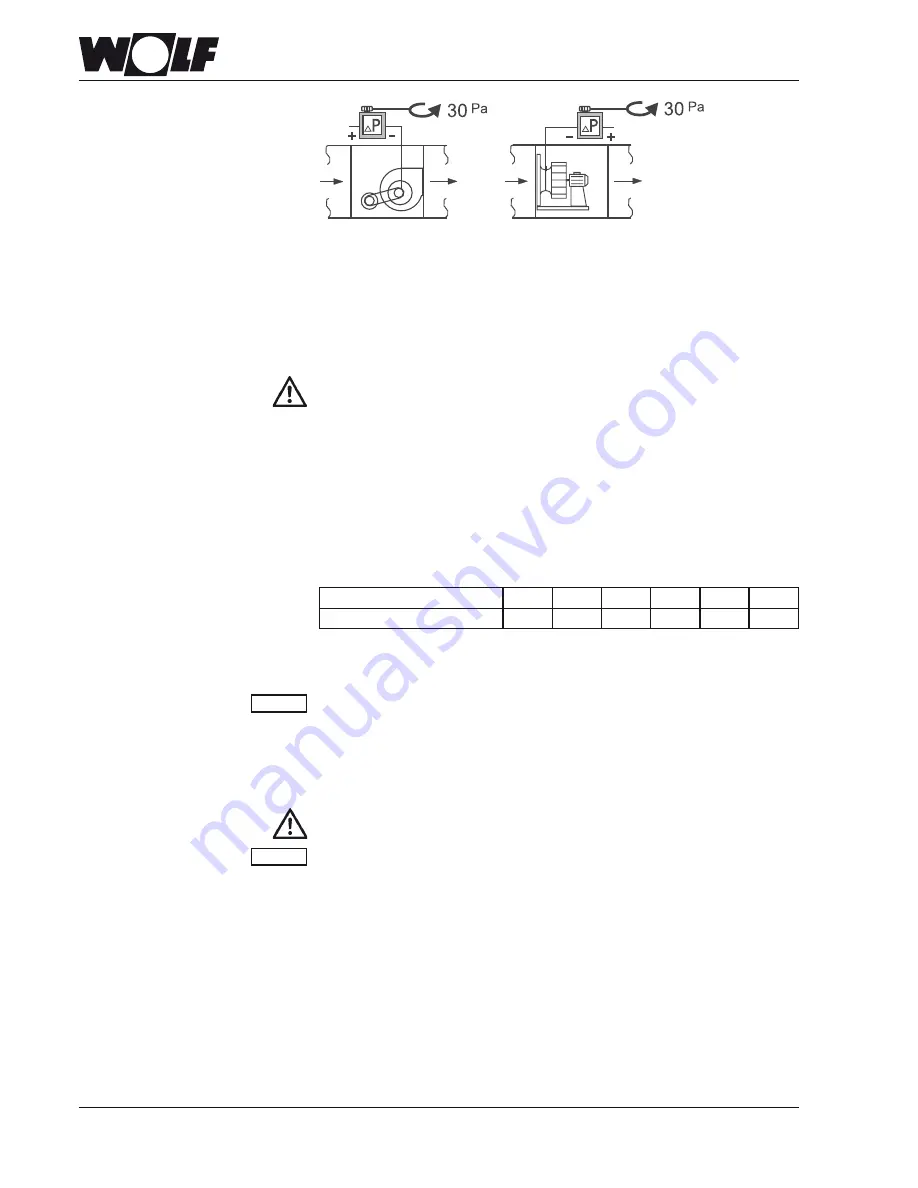
26
3064058_201610
AHU TE
AHUW TE
Commissioning
Cooling coil
(cold water)
Before commissioning the air-handling unit, check the entire pipework for leaks.
- Vent the heat exchanger and the pipework.
- Ensure that condensate can drain off, to prevent the condensate tray from
overflowing.
- If appropriate, before commissioning a chilled water cooling coil check whether the
antifreeze concentration in the chilled water is adequate for the anticipated temperature
range. When antifreeze is added to the chilled water, the cooling coil’s power decreases
in proportion to the increase in antifreeze concentration.
The minimum airflow velocity over the electric heating coil is 1.5 m/s (otherwise risk of
overheating).
If the motor is of the multi-speed or variable-speed type, irrespective of the heating power
of the electric heating coil it is important to ensure that the airflow velocity does not drop
below the specified minimum even when the motor is operating at its lowest speed.
It is permissible to install an electric heating coil on the intake side (upstream of the drive
motor/fan as viewed in the direction of air flow) only if the heating coil’s air discharge
temperature does not exceed 40 °C.
Always comply with the applicable safety regulations for electric heating appliances.
Always ensure that the electric heating register shuts down automatically if
the air flow stops. In addition, the electric heating register must be switched
by one or more switching devices (contactors) having a control circuit wired
through the series connected safety temperature limiter. Ensure that at least
one safety temperature limiter is installed at the top inside of the heating coil.
Ensure that the electric heating register is protected against humidity and water.
Note
Note
Electric heating coil
To prevent overheating, ensure that the air flow rates comply with the minimum value
specified below (figures are in m³/h):
Appliance type AHU TE/AHUW TE 21/43
64/96 130/170 210/270 320/380
450
2200
3200
5700
9000
12500
22500
Heating coil
(warm water/hot water/steam)
Before starting the air-handling unit, check the entire pipework for leaks.
- Vent the heat exchanger and the pipework.
- Ensure that condensate can always drain freely from steam registers, to prevent
steam hammer from damaging the register.
- To prevent overheating due to inadequate heat transfer, ensure that the fan is running
before you switch on the heating water pump or open the water/steam valve.
- Check the air discharge temperature; max. air discharge temperature with heating
coil on intake side is 40 °C; otherwise risk of motor overheating.
Always bear in mind that surfaces of heat exchangers and connecting adaptors
become hot.
Risk of burns and scalding.
Plate-type heat exchanger
with dampers
The recirculating air damper must be open and the bypass damper must be closed if
a plate-type heat exchanger with bypass dampers (and extra recirculating air damper)
operates in recirculating air mode. This means that the fresh air induced into the system
is preheated. The outside air damper can be partially closed in recirculating air mode.
Closing the bypass damper means that the outside air is preheated. Opening the bypass
damper provides a means of defrosting the plate-type heat exchanger if ice forms in winter.
Flow rate monitor