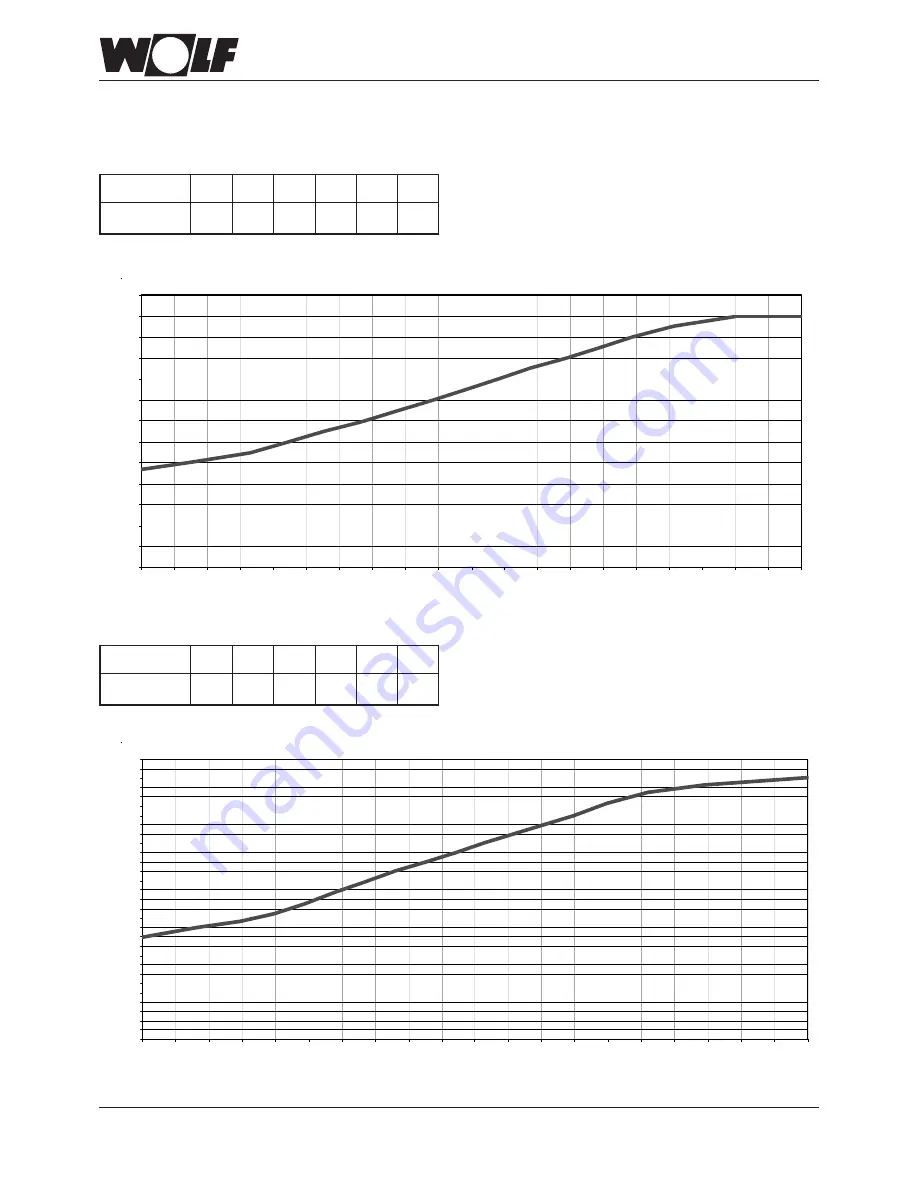
1 8
3062087_0207
Limiting the maximum output
The output setting can be modified with Wolf control accessories with eBUS capability via parameter HG 04.
The heating output will be determined by the modulation current of the the gas valve. By reducing the modulation current in accordance
with the table, the maximum output will be matched at 80/60 °C to natural gas H and LPG.
0
2
4
6
8
10
12
14
16
18
20
22
24
26
0
5
10
15
20
25
30
35
40
45
50
55
60
65
70
75
80
85
90
95
100
Output [kW]
Modulation current [%]
Output change CGG-1K-24 G31 / G30 / G20
Output [kW]
Modulation current [%]
Output change CGG-1K-28 G31 / G30 / G20
0
1
2
3
4
5
6
7
8
9
10
11
12
13
14
15
16
17
18
19
20
21
22
23
24
25
26
27
28
29
30
0
5
10
15
20
25
30
35
40
45
50
55
60
65
70
75
80
85
90
95
100
Output [kW]
10.9
14
18
22
26
28
I
Mod
[%]
1
22
38
56
73
100
Output [kW]
9.4
12
15
18
21
24
I
Mod
[%]
1
22
39
54
69
100