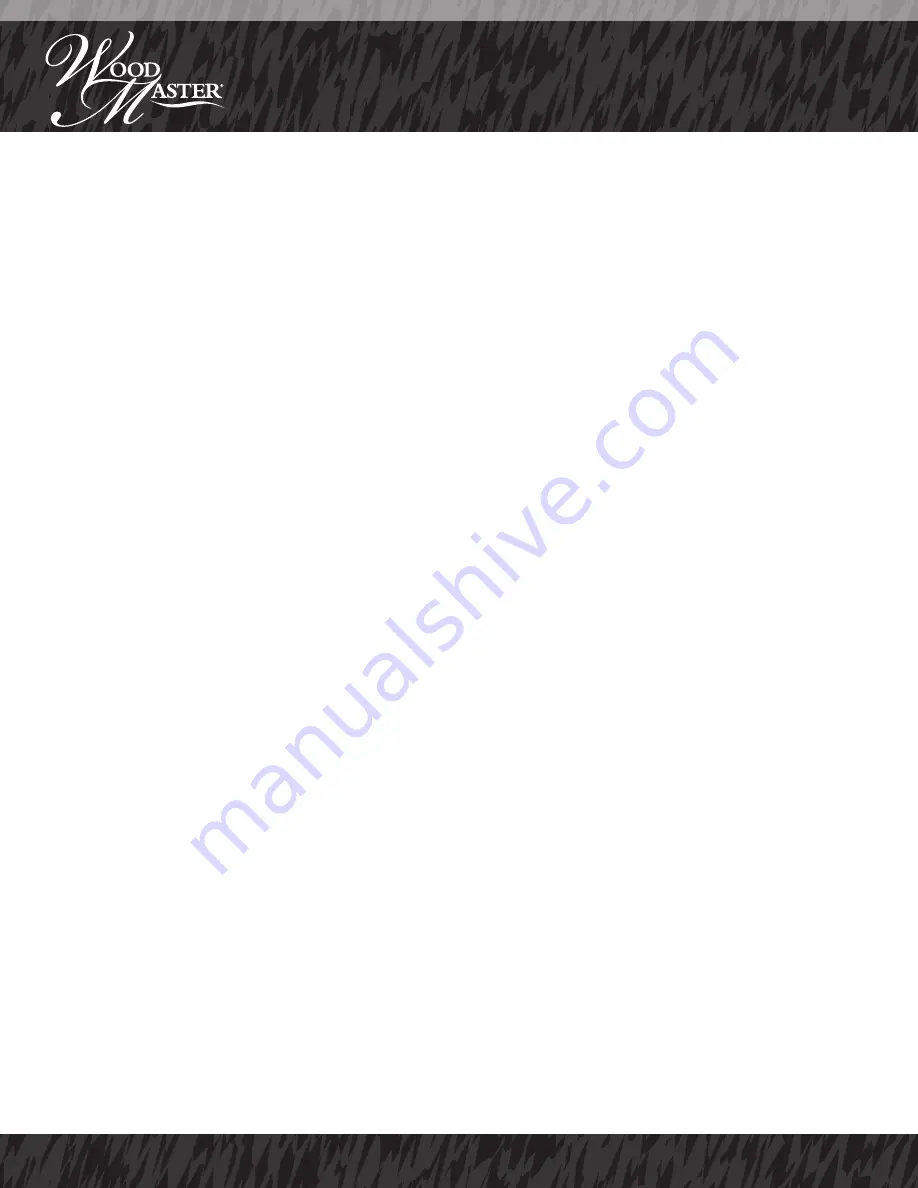
40
Mini Boiler Owners Manual
2015
Warranty
VI. Any costs for labor for the examination, removal or reinstallation of allegedly defective parts, transportation of the parts to and
from Northwest Manufacturing, Inc. facilities will not be covered and will be the responsibility of the Original Owner. This includes
any other labor and costs for any material necessary for the said examination, removal or re-installation.
VII. The warranty will not cover damage to the Boiler and Burner or any of their original parts, replacement parts or other accesso-
ries or standard equipment caused by excessive temperatures or pressures, vandalism, fuel or gas explosion, electrical, chemical or
electrochemical reaction, electrical failures, insurrection, riots, war, acts of God, combustion air contaminated externally, air
impurities, sulfur or sulfuric action or reaction, dust particles, corrosive vapors, oxygen corrosion, and situating the Boiler and
Burner in an unsuitable location or continuing use of the Boiler and Burner after onset of a malfunction or discovery of a defect.
VII. Consumable parts, and parts in direct contact with the flame, will not be covered under this warranty.
WARRANTY TERMS
The Warranty shall also be subject to the following terms and conditions:
I. The Boiler and Burner must have been installed by a Certified Contractor.
II. The Boiler and Burner must have been properly maintained, cleaned and serviced during the Warranty Periods in accordance to
the manual.
III. This Warranty is non transferable and only covers the Original Owner, at the original site of installation.
IV. Northwest Manufacturing, Inc. shall have the time needed and unobstructed access to the Boiler and Burner for the purpose of
conducting tests of the Boiler and Burner and for the making of repairs or installation of replacement parts.
V. Repairs, replacement or the repair of replacement parts shall be subject to the terms and conditions of this Warranty as if they
had been installed at the time of original installation.
VI. This Warranty is limited to the provisions previously described and does not extend to any Boiler and Burner, related parts or
products that are (a) not sold in Canada or the United States; (b) not installed in Canada or the United States; or (c) not purchased
from an Authorized Distributor.
VII. Northwest Manufacturing, Inc. shall not be responsible for any consequential damages, direct or indirect caused by the
products described in this Warranty.
APPLICABLE LAW
All disputes or claims on the Warranty shall be determined in accordance with the laws of Red Lake County, Minnesota.
WARRANTY CLAIM/SERVICE
Notify the Certified Contractor who installed your Boiler and Burner. The Contractor will then notify Northwest Manufacturing, Inc.
who will make all warranty decisions. No warranty work can be carried out without approval from Northwest Manufacturing, Inc..
If the Certified Contractor fails to make a warranty claim, contact Northwest Manufacturing, Inc. directly. Allegedly defective parts
MUST be returned to Northwest Manufacturing, Inc. for the purpose of inspection to determine cause of failure.
Northwest Manufacturing, Inc. / 600 Polk Ave. SW / Red Lake Falls, MN 56750-5002
(800) 932-3629 • Fax: (218) 253-4409 / www.woodmaster.com