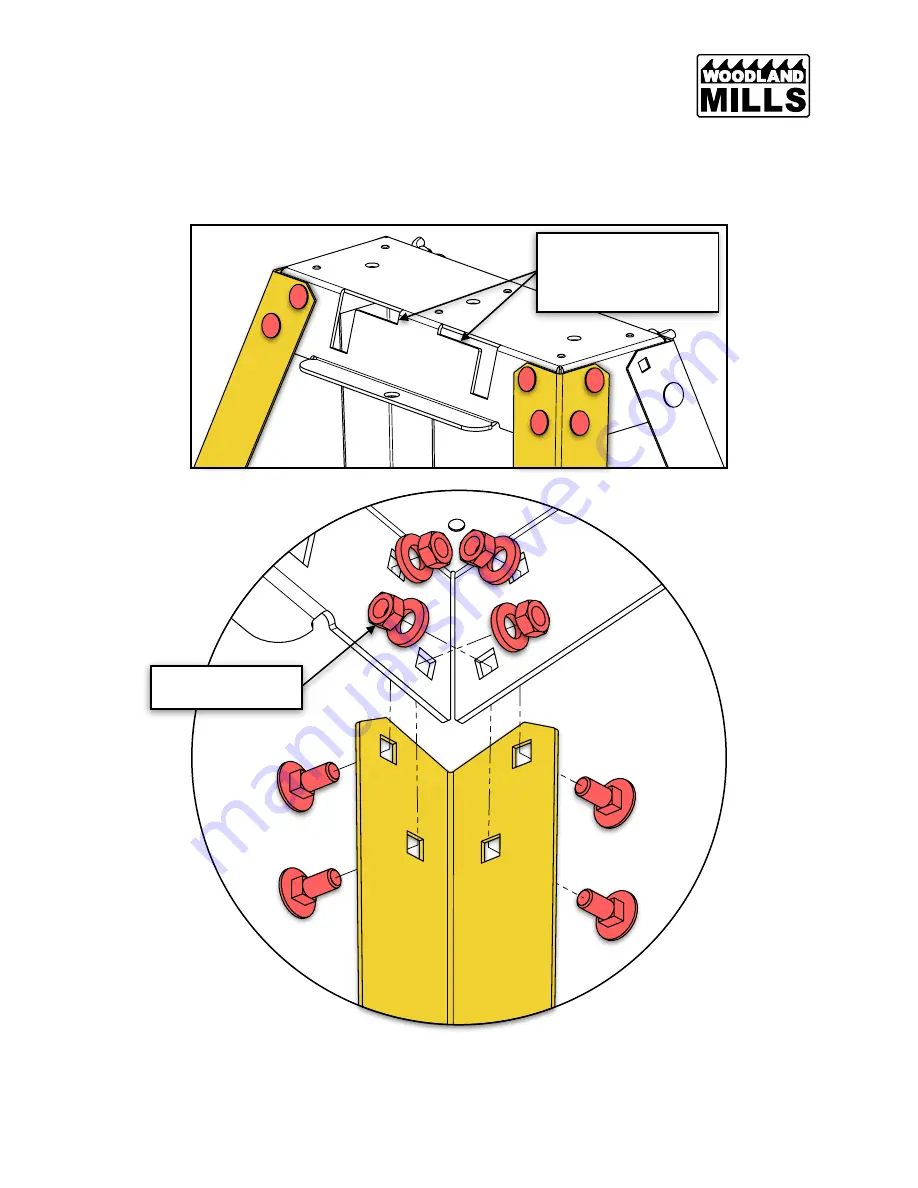
Sharpener Operator’s Manual
C. LEGS-TO-MOUNTING BASE (REAR)
Fasten the rear legs to the mounting base using the following hardware on each leg: four (4) M5
X 12 mm carriage bolts, four (4) M6 flat washers, four (4) M5 hex nuts.
BBS-MY2020-EN: Rev A
Page
of
10
52
19-May-2020
(4X) M5 Hex Nuts
Rear face of mounting
base has slots for
support arms.
Summary of Contents for BANDSAW BLADE SHARPENER
Page 1: ...BANDSAW BLADE SHARPENER OPERATOR S MANUAL BBS MY2020 EN Rev A Publication Date 19 May 2020 ...
Page 2: ......
Page 47: ...Sharpener Operator s Manual CONTROL BOX BBS MY2020 EN Rev A Page of 45 52 19 May 2020 ...
Page 48: ...Sharpener Operator s Manual GRINDING HEAD BBS MY2020 EN Rev A Page of 46 52 19 May 2020 ...
Page 51: ...Sharpener Operator s Manual NOTES BBS MY2020 EN Rev A Page of 49 52 19 May 2020 ...
Page 52: ...Sharpener Operator s Manual BBS MY2020 EN Rev A Page of 50 52 19 May 2020 ...
Page 53: ...Sharpener Operator s Manual BBS MY2020 EN Rev A Page of 51 52 19 May 2020 ...
Page 54: ...Sharpener Operator s Manual BBS MY2020 EN Rev A Page of 52 52 19 May 2020 ...
Page 55: ......
Page 56: ......