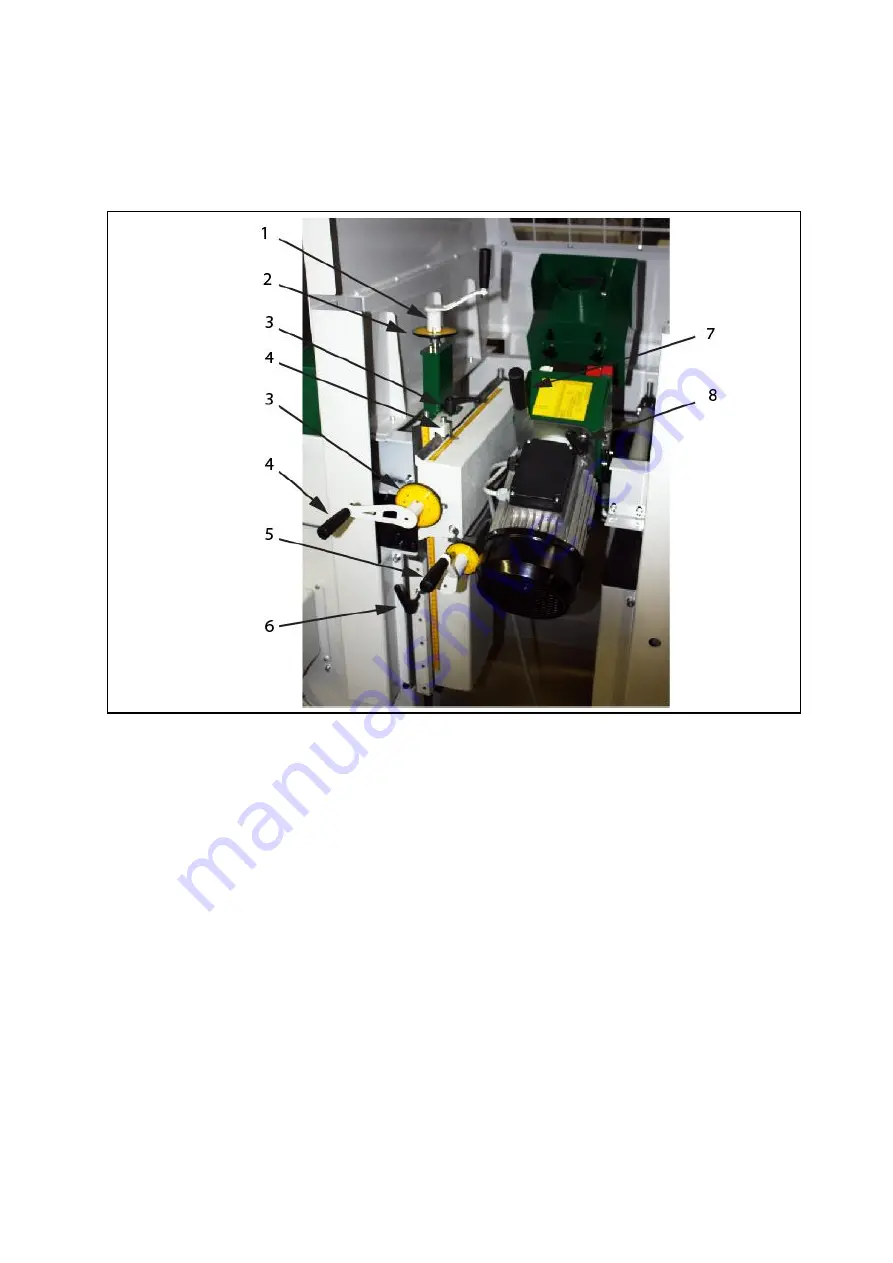
11
5th cutter
5th cutter can be used for a variety of
machining operations such as:
- finplanhyvling
- Profiling at different angles
- Brushing
- grinding
Safety
• Ensure that the cutter always do not
climb routing (rotates against the feed
direction)
• Cuttter with 30 mm hole must be
approved for 9000 r / min.
• Rotating shaft tools can have up to
D20 mm shaft and be approved for
14000 rpm.
Handling
Starting the machine is interlocked by:
- thermoswitch in the motor (the motor
is to warm and will not start the cutter)
- switch on belt gearbox (if the door is
open does not start cutter)
- emergency stop (emergency stop
button must be pulled out)
- switch on hood (if the door is open
does not start cutter)
On the backside of the machine it is a
electrical box for the 5
th
cutter. The
lamp on this box will bo on if all
swiches is in the run position.
Summary of Contents for PH365
Page 18: ...18 Overview ...
Page 19: ...19 Front ...
Page 20: ...20 Front ...
Page 21: ...21 Backside ...
Page 22: ...22 Backside ...
Page 23: ...23 Left vertical cutter ...
Page 25: ...25 Upper cutter feed rollers ...