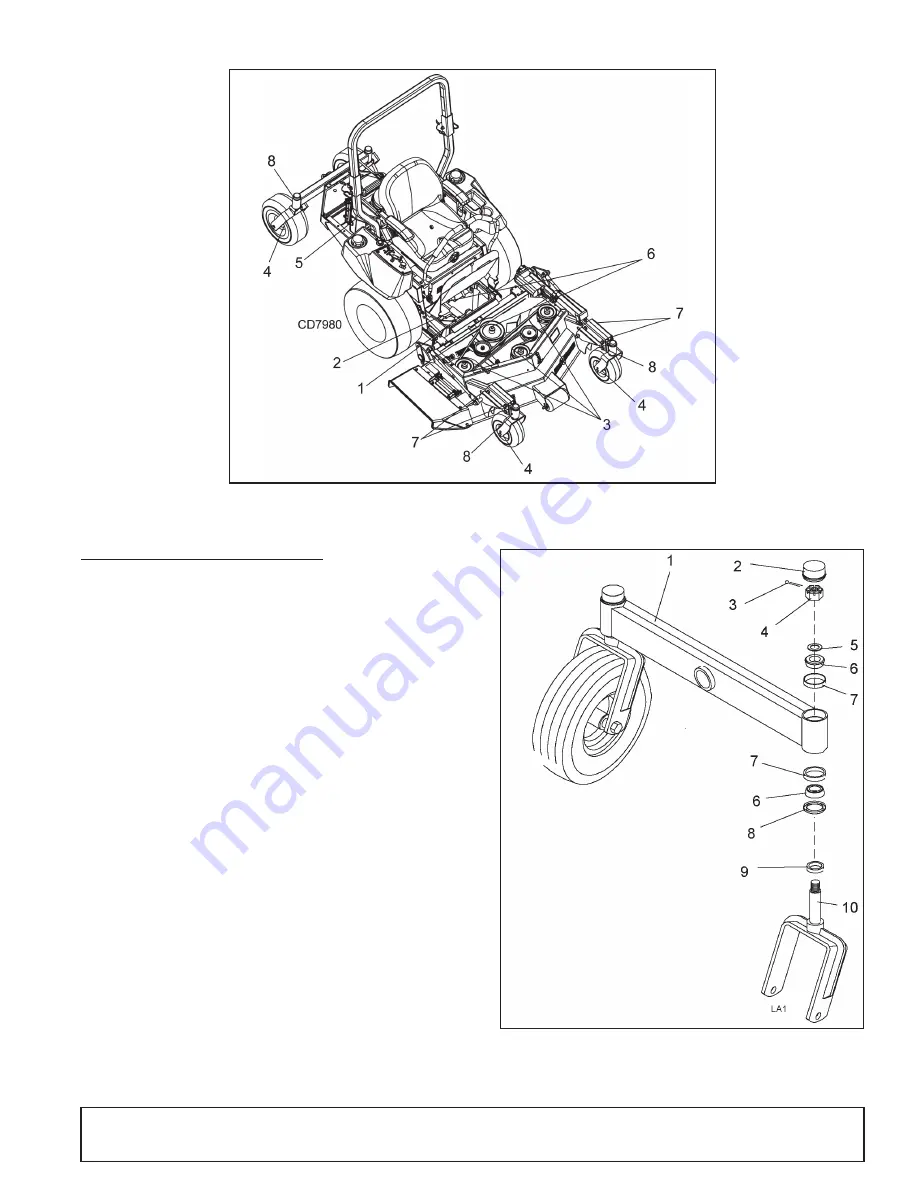
Owner Service
17
MAN1192 (1/13/2017)
Figure 4
. Lubrication Diagram
TAILWHEEL MAINTENANCE
Once a year, disassemble tailwheel assembly and
inspect roller bearings:
1.
Remove dust cap (2) from top of tailwheel
assembly (1).
2.
Remove cotter pin (3) and slotted hex nut (4).
3.
Remove wheel fork (10), bearing cones (6) and
remaining hardware from assembly.
4.
Inspect bearing cones (6) and bearing cups (7) for
wear and replace if necessary. Replace seals and
washers as necessary.
5.
Pack bearing cones (6) with a good grade wheel
bearing grease.
6.
Install wheel fork (10) bearing cones (6) and
remaining hardware into assembly as shown.
7.
Set bearings by torquing nut to 26 lbs-ft. All bearing
free play should be removed.
NOTE:
Proper bearing adjustment is essential to good
bearing life.
If bearings are loose, casters will wobble and/or slap
side-to-side.
If bearings are overtightened, loosen hex nut and rap
shaft with a lead hammer to loosen bearings. Readjust
bearings until proper setting is obtained.
Figure 5
. Tailwheel Assembly (Typical)
1. Tailwheel assembly
2. Dust cap
3. Cotter pin
4. Slotted hex nut
5. Bushing washer 3/4 x 14 GA
6. Bearing cone
7. Bearing cup
8. Seal
9. Spacer
10. Wheel fork
Summary of Contents for MOW'N MACHINE FZ22-2
Page 1: ...OPERATOR S MANUAL MOW N MACHINE MAN1192 1 13 2017 FZ22 2 TM ...
Page 28: ...28 Dealer Check Lists MAN1192 1 13 2017 NOTES ...
Page 30: ...30 Parts MAN1192 1 13 2017 FZ22 2 FRAME ASSEMBLY ...
Page 34: ...34 Parts MAN1192 1 13 2017 PTO CLUTCH PUMP ASSEMBLY ...
Page 38: ...38 Parts MAN1192 1 13 2017 FZ22 2 WIRING DIAGRAM ...