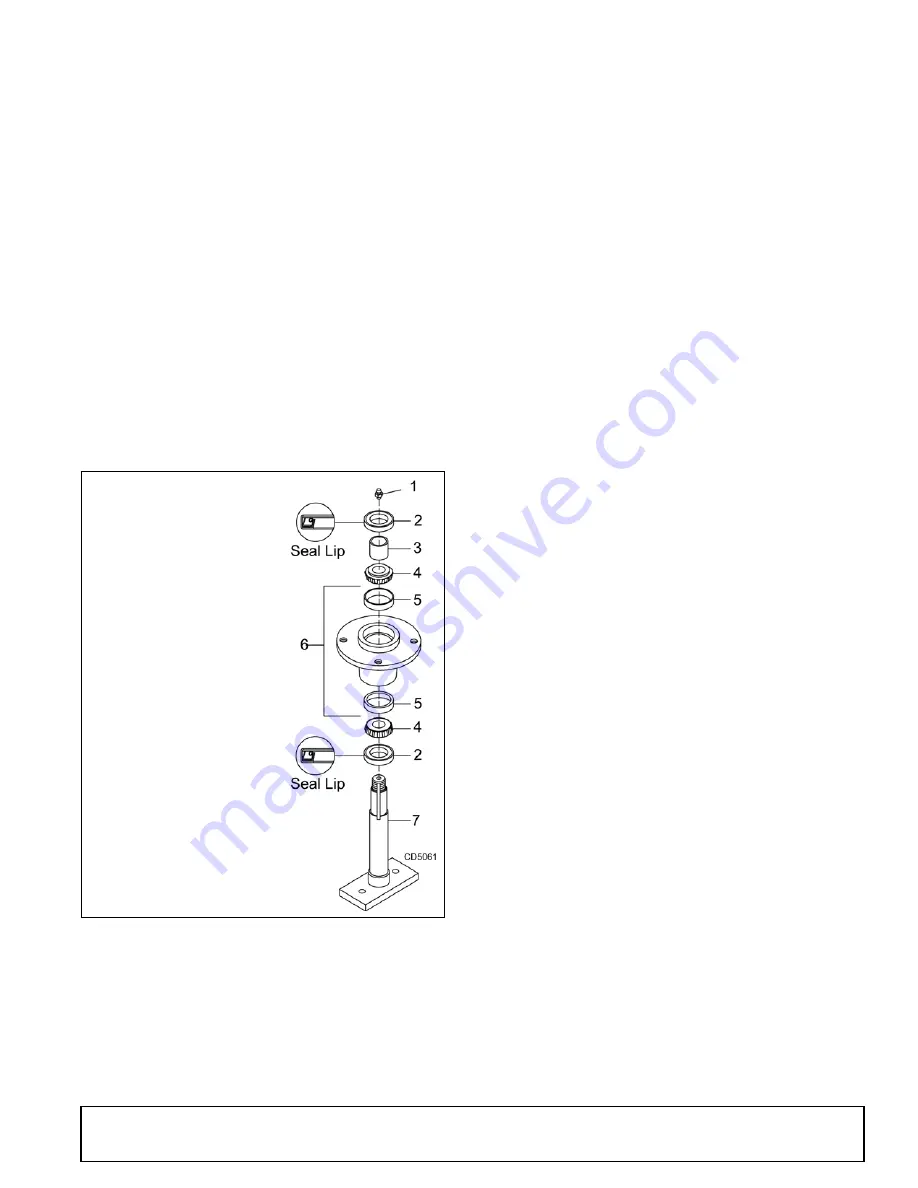
Dealer Service 23
MAN0475 (9/21/2005)
Spindle Assembly
Refer to Figure 17.
Bearing cones and cups are designed to work together.
It is important to position them so bearing cone taper
mates with cup taper.
1. Lubricate new cups with a light oil. Place them in
spindle housing so they will mate with bearing
cones. Cups and cones are a press fit to minimize
wear.
Seat cups securely with a press or place a large
drift in the flat lip and drive them into housing until
cup seats against machined shoulder of housing.
Remove bearing cups from housing by placing a
punch in the slots provided and driving them out.
Alternate punch positions from side to side. Take
care to prevent housing damage.
2. Place bottom bearing cone into spindle with taper
positioned to mate with cup.
Figure 17. Spindle and Shaft Assembly
IMPORTANT
■
Improper positioning of seals can cause seal
damage. An improperly installed seal will leak and
could cause bearing failure.
3. Identify the open side of the seal containing the
spring.
4. Apply a thin coat of Permatex to the area of
housing where seals seat.
5. Install bottom seal with spring up toward center of
housing.
6. Place seal squarely on housing and select a piece
of pipe or tubing with an OD that will set on outside
edge of seal. A tubing with an OD that is too small
will bow seal cage.
7. Carefully press seal into housing, to prevent
distortion to metal seal cage. Bottom seal should
seat firmly and squarely against machined
shoulder in housing.
8. Make sure seal lip did not roll under. Distortion to
seal cage or damage to seal lip will cause seal to
leak. Damaged seals must be replaced.
9. Insert shaft and bearing through bottom of housing.
10. Fill housing cavity with a medium grade grease.
11. Install top bearing on shaft to mate with top cone.
12. Apply a thin coat of Permatex to shaft area where
sleeve will seat.
13. Install sleeve on shaft and press sleeve and
bearing into housing until all free play is removed
and there is a very light drag on bearings (similar to
adjusting front wheel bearings on an automobile).
Check by spinning spindle. It should turn freely.
14. Be careful not to overtighten bearings. Proper
bearing adjustment is essential to good bearing
life.
15. If you overtighten bearings, hold spindle housing
and rap spindle shaft with a lead hammer.
16. Carefully press top seal in with spring up. Top seal
should be flush with or to within 1/16" above the
housing.
17. Rotate housing on spindle shaft, checking for free
movement.
18. Install grease fitting in spindle shaft.
Spindle Installation
IMPORTANT
■
Pulley installation sequence is very important
for bearing life. Follow the sequence exactly.
1. Install spindle through bottom of mower and secure
with four mounting bolts.
2. Install pulley and split taper bushing with integral
key on spindle shaft. Make sure bushing is in
contact with sleeve on spindle shaft.
3. Alternately tighten split taper bushing cap screws
to 12 lbs-ft.
4. Install toothed lock washer and nut on spindle
shaft. Tighten nut until snug. Bend up edge of lock
washer against a flat side on nut.
1. Grease fitting
2. Seal, 1.50 x 2.12 x .31
3. Sleeve, 1.14 x 1.50 x .55
4. Bearing, cone
5. Bearing, cup
6. Spindle, housing
7. Shaft, blade spindle