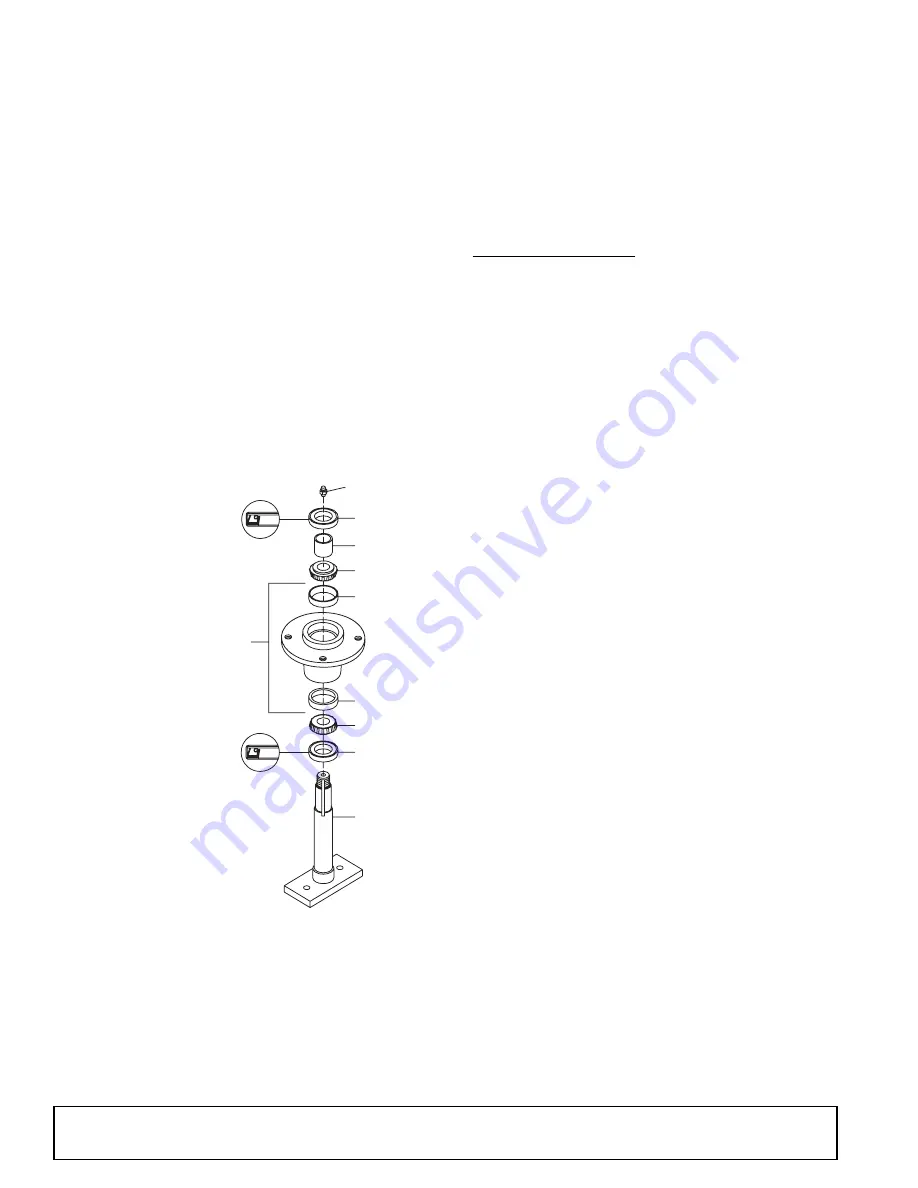
22
Dealer Service
MAN0180 (Rev. 1/7/2005)
Refer to Figure 19.
12.
Apply a thin coat of Permatex to shaft area where
sleeve will seat.
13.
Install sleeve on shaft and press sleeve and
bearing into housing until all free play is removed
and there is a very light drag on bearings (similar to
adjusting front wheel bearings on an automobile).
Check by spinning spindle. It should turn freely.
14.
Be careful not to overtighten bearings. Proper
bearing adjustment is essential to good bearing
life.
15.
If you overtighten bearings, hold spindle housing
and rap spindle shaft with a lead hammer.
16.
Carefully press top seal in with spring up. Top seal
should be flush with or to within 1/16" above the
housing.
17.
Rotate housing on spindle shaft, checking for free
movement.
18.
Install grease fitting in spindle shaft.
Figure 19
. Spindle & Shaft Assembly
Spindle Installation
IMPORTANT
■
Pulley installation sequence is very important
for bearing life. Follow the sequence exactly.
1.
Install spindle through bottom of mower and secure
with four mounting bolts.
2.
Install pulley and split taper bushing with integral
key on spindle shaft. Make sure bushing is in
contact with sleeve on spindle shaft.
3.
Alternately tighten split taper bushing cap screws
to 12 lbs-ft.
4.
Install toothed lock washer and nut on spindle
shaft. Tighten nut until snug. Bend up edge of lock
washer against a flat side on nut.
GEARBOX REPAIR
Read this entire section before starting any repair.
Many steps are dependent on each other.
Fill gearbox with SAE 80W or 90W gear lube until it
runs out the side level plug.
Repair to this gearbox is limited to replacing bearings,
seals, and gaskets. Replacing gears, shafts, and a
housing is not cost effective. It is more economical to
purchase a complete gearbox if repair to anything other
than replacement of bearings, seals or gaskets is
required.
Inspect gearbox for leakage and bad bearings.
Leakage is a very serious problem and must be cor-
rected immediately.
Bearing failure is indicated by excessive noise and side
to side or end play in gear shafts.
Seal Replacement
Recommended sealant for gearbox repair is Perma-
tex
®
Aviation 3D Form-A-Gasket or equivalent.
Leakage can occur at the vertical or horizontal gaskets
and shaft seals.
Leakage at the horizontal gasket or seal can be
repaired without removing the gearbox from the cutter.
Seal Installation
NOTE:
Proper seal installation is important. An improp-
erly installed seal will leak.
1.
Clean area in housing where seal outer diameter
(OD) seats. Apply a thin coat of Permatex.
2.
Inspect area of shaft where seal seats. Remove
any burrs or nicks with an emery cloth.
3.
Lubricate gear shaft and seal lips.
4.
Place seal squarely on housing, spring-loaded lip
toward housing. Select a piece of pipe or tubing
with an OD that will sit on the outside edge of the
seal but will clear the housing. Tubing with an OD
that is too small will bow seal cage and ruin seal.
5.
Carefully press seal into housing, avoiding
distortion to the metal seal cage.
2
1
2
3
4
5
4
5
7
6
Seal Lip
Seal Lip
CD5061
1. Grease fitting
2. Seal, 1.50 x 2.12 x .31
3. Sleeve, 1.14 x 1.50 x
.55
4. Bearing, cone
5. Bearing, cup
6. Spindle, housing
7. Shaft, blade spindle