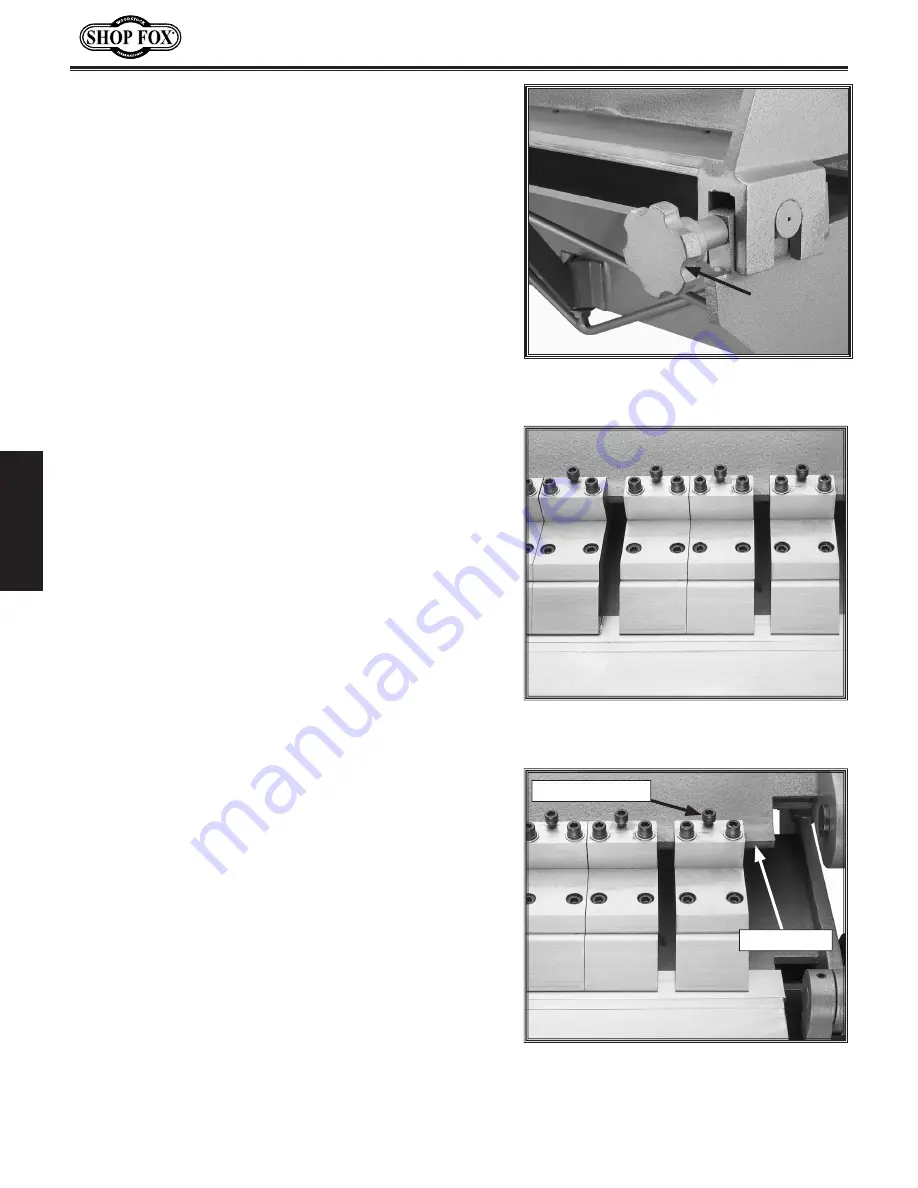
-18-
M1012 48" Pan and Box Brake
O
PE
R
AT
O
N
S
Figure 21.
Setback adjustment knob (one
of two) for clamping leaf.
2.
Rotate both setback knobs evenly (
Figure 21
) to
move the front edge of the fingers toward or away
from the edge of the clamp block.
Note:
Make sure the finger edges are parallel with
the edge of the clamp block or your bend will be dis-
torted.
Spacing Fingers
The fingers can be spaced apart for clearance when mak-
ing pans or boxes. This requires removing one or more of
the fingers so that you can space the others to match the
width of your pan or box (
Figure 22
).
To space the fingers apart, do these steps:
1.
Remove one of the end fingers by loosening the top
cap screw, shown in
Figure 23,
and slide it off the
front guide.
2.
Loosen the top cap screws of the fingers you need to
move, and slide them across the front guide so that
you have adequate room for your workpiece on both
sides.
Note:
You may need to mix and match finger widths
to equal the size of your workpiece.
3.
Align the fingers and tighten the cap screws. (See
Page 16
for alignment instructions.)
Figure 22
. Fingers spaced apart to allow
clearance of pan or box sides.
Figure 23.
Top cap screw for loosening
finger in order to slide it off the front
guide.
Front Guide
Top Cap Screw
Summary of Contents for SHOP FOX M1012
Page 2: ......
Page 28: ... 26 M1012 48 Pan and Box Brake PARTS PARTS ...
Page 30: ... 28 M1012 48 Pan and Box Brake PARTS PARTS ...
Page 35: ......
Page 36: ......