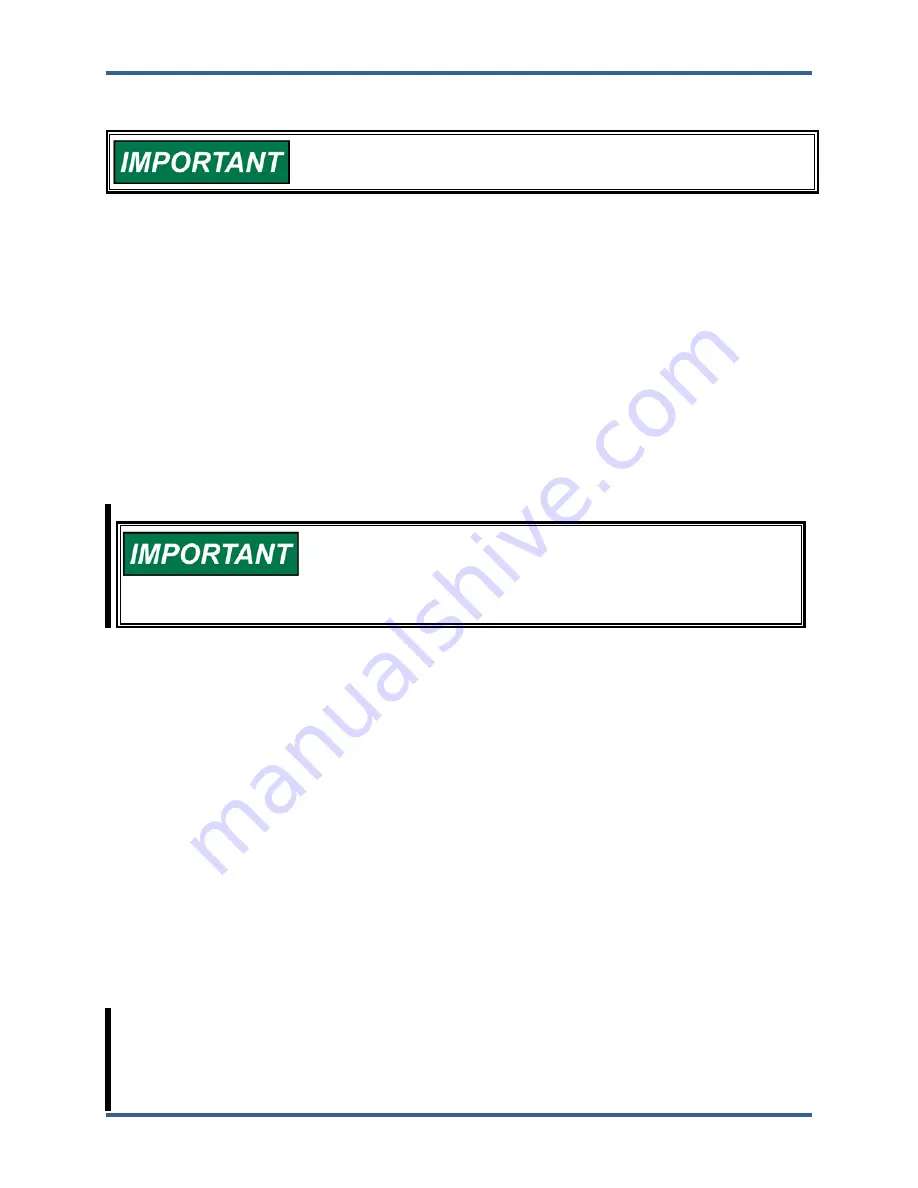
Manual 26166V1
MicroNet Simplex & MicroNet Plus
Woodward
8
Regulatory Compliance
For LINKnet regulatory information, please refer to the appropriate
chapter in Volume 2 of this manual.
European Compliance for CE Marking
These listings are limited only to those units bearing the CE Marking:
EMC Directive:
Declared to Directive 2014/30/EU of the European Parliament and
of the Council of 26 February 2014 on the harmonization of the laws
of the Member States relating to electromagnetic compatibility
(EMC)
Low Voltage
Directive:
Directive 2014/35/EU on the harmonisation of the laws of the
Member States relating to the making available on the market of
electrical equipment designed for use within certain voltage limits
ATEX – Potentially Explosive
Atmospheres
Directive:
Directive 2014/34/EU on the harmonisation of the laws of the
Member States relating to equipment and protective systems
intended for use in potentially explosive atmospheres
Zone 2, Category 3, Group II G, Ex nA [nL] IIC T3 X
EMC Compliance
The MicroNet Digital Control must be installed inside a metal
enclosure or cabinet to meet the EMC Directive requirements.
Reference Section 15 of manual 26166V2 for considerations
regarding the installation location and specific cabinet construction
requirements.
Other European and International Compliance
Compliance with the following European Directives or standards does not qualify this product for
application of the CE Marking:
EAC
Customs Union:
Certified for use in Ordinary Locations only to Technical Regulation
CU 004/2011 On the Safety of Low Voltage Equipment and CU
020/2011 On the Electromagnetic Compatibility of Technical
Equipment Declaration of Conformity Registration No: RU C-US
.A
Л
32.B.02262.
North American Compliance
These listings are limited only to those units bearing the CSA identification:
CSA:
CSA Listed for Class I, Division 2, Groups A, B, C, & D, T3A at 55
°C surrounding air temperature. For use in Canada and the United
States.
5441-694 DIO FTM Relay Driver rated for temperatures up to 75 °C,
Temperature Code T3A per certifcate 2314167.
Marine
American Bureau
of
Shipping:
Rules for Condition of Classification, Part 1 2015 Steel Vessels
Rules 1-1-4/7.7, 1-1-A3, 1-1-A4, which covers the following: Steel
Vessel (2015): 4-2-1/7.5.1, 4-2-1/7.3, 4-9-8/13, 4-9-6/23, 4-9-5/17;
Steel Vessels Under 90 Meters (295 Feet) in Length (2015):
4-7-4/3.9 Offshore Support Vessels (2015): 4-2-1/7.5.1, 4-2-1/7.3,
4-9-8/13, 4-9-6/23, 4-9-5/17
Released