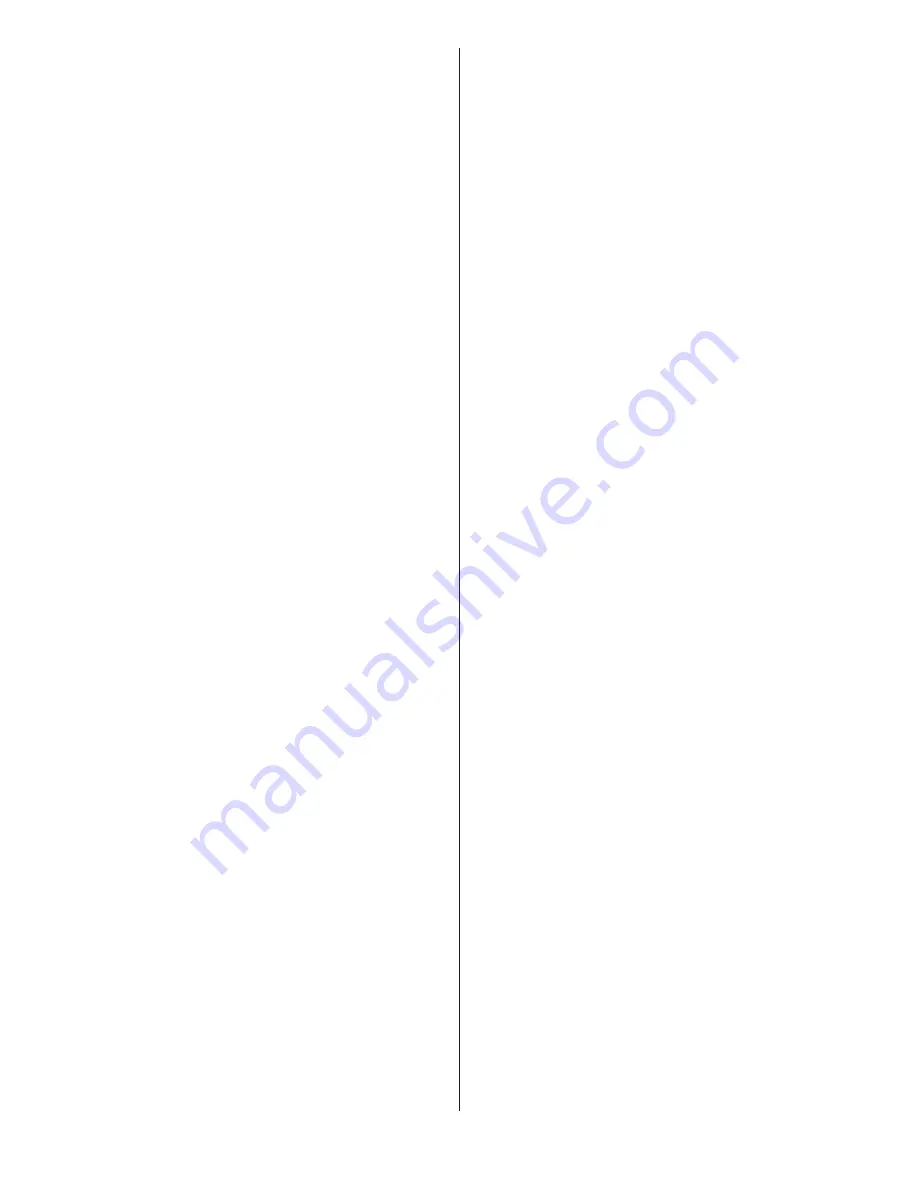
13. Central Heating Sensor.
See Fig. 31.
Remove the inner casing cover as described in Section 14.3(b).
Check that the electricity supply to the appliance is turned off.
Carefully pull off the two leads from the sensor.
Pull off the sensor and spring retaining clip from the pipe.
Fit the replacement sensor in reverse order with a layer of heat
sink compound between the faces. Refit the leads.
14. Domestic Hot Water Sensor.
Check that the electricity supply to the appliance is turned off.
Hinge the facia assembly in the servicing position as described in
Section 14.3(c and d).
Carefully pull off the two leads from the sensor.
Undo and remove the screw, pull off the sensor and spring
retaining clip from the pipe.
Fit the replacement sensor in the reverse order ensuring a layer
of heat sink compound is between the faces. Refit the leads.
15. Circulating Pump.
Check that the electricity supply to the appliance is turned off.
Drain the central heating circuit as described in Section 15.3(a).
Hinge the facia assembly in the servicing position as described in
Section 14.3(d).
Undo the two union nuts and the pipe to the expansion vessel,
remove the pump from the pipe-work. Support the pump and
remove the electrical cover.
Disconnect the electrical wires taking note of their positions.
Fit the replacement pump in the reverse order using new sealing
washers.
(Alternatively replace the pump head only by removing the four
Allen screws on the pump, remove the head and support whilst
removing the electrical connections. Refit the new head).
Open the valves and fill and re-pressurise the system as
described in Section 12.2
NOTE:
The direction of flow should be downwards. The speed
should always be set to maximum.
16. Expansion Vessel.
Drain the central heating circuit as described in Section 15.3(a).
Hinge the facia assembly in the servicing position as described in
Section 14.3(d).
Remove the air pressure switch, gas to water heat exchanger,
water to water heat exchanger and pump as described in 15.4
(2), (5), (15) and (20) and remove the vessel.
Fit the replacement vessel in the reverse order.
Open the valves and fill and re-pressurise the system as
described in Section 12.2
17. Pressure Relief Valve.
See Fig. 24.
Drain the central heating circuit as described in Section 15.3(a).
Hinge down the facia assembly as described in Section 14.3(c)
Remove the Bottom panel as described in Section 14.3(d)
Remove the pressure gauge connection, pull out the retaining
clip, undo the discharge pipe connection and remove the valve
taking care not to distort the pipework.
Fit the replacement valve in reverse order. Reconnect the
discharge pipe.
Open the valves and fill and re-pressurise the system as
described in Section 12.2
18. Water Diverting Valve Micro Switch Assembly.
Check that the electricity supply to the appliance is turned off.
Hinge down the facia assembly as described in Section 14.3(c).
Remove the Bottom panel as described in Section 14.3(d)
Using a pair of fine nosed pliers, pull the circlip off and remove
the micro switch assembly from the valve. Remove the black
cover and carefully pull off the connections from the terminals
on the micro switches.
Withdraw the switch assembly from the appliance.
Fit the replacement micro switch assembly in the reverse order.
19. Water Diverting Valve.
Check that the electricity supply to the appliance is turned off.
Drain the central heating and domestic hot water circuits as
described in Sections 15.3 (a and b).
Hinge down the facia assembly in the servicing position as
described in Section 14.3.(c).
Remove the Bottom panel, water to water heat exchanger, micro
switch assembly and filling loop as described in Section 14.3(d)
and 15. 4 (20) and (24).
Undo all the water connections to the valve.
Fit the replacement valve in the reverse order ensuring that the
filter and all fibre washers and ‘O’ rings are in place and lubricated.
Open the valves and fill and re-pressurise the system as
described in Section 12.2.
20. Water to Water Heat Exchanger.
Check that the electricity supply to the appliance is turned off.
Drain the central heating and domestic hot water circuits as
described in Sections 15.3(a and b).
Hinge down the facia assembly in the servicing position as
described in Section 14.3(c).
Remove the Bottom panel as described in Section 14.3(d).
Remove the filling loop as described in Section 15.4 (24). Undo
the diverter valve connection. Remove the bolt and circlip and
pull the heat exchanger forward and away from the appliance.
Fit the replacement heat exchanger in the reverse order.
Open the valves and fill and re-pressurise the system as
described in Section 12.2
21. Domestic Hot Water Flow Restrictor.
Remove the water to water heat exchanger assembly as
described in Section 15.4.20.
The plastic flow restrictor is located within the brass housing on
the heat exchanger.
Fit the replacement flow restrictor and reassemble in the reverse
order ensuring the fibre washers and ‘O’ rings are in place.
22. Pressure Gauge.
Check that the electricity supply to the appliance is turned off.
Drain the central heating circuit as described in Section 15.3(a).
Remove the two upper screws and hinge down the facia panel as
described in Section 14.3(c).
Remove circlip and pull out the capillary sensing bulb in the
return manifold.
Prize back the retaining clips securing the gauge to the facia
panel and remove.
Fit the replacement gauge in the reverse order ensuring the “O”
ring is in place.
Open the valves and fill and re-pressurise the system as
described in Section 12.2
23. Control Board.
Check that the electricity supply to the appliance is turned off.
Undo the 3 screws and remove the facia bottom panel.
Carefully pull off all the connectors. Disconnect the mains supply
lead at terminal ST 12and the earth connection at the back.
Remove the two upper screws and hinge down the facia assembly.
Remove the plastic water cover.
Remove the four corner screws on the back of the facia and
separate the metal back panel from the plastic facia.
Release the four plastic pillars on the control board and pull
forward off the back panel.
Remove transformer from rear of board.
Fit the replacement board in the reverse order ensuring it is
pushed firmly onto the four posts and clicks into place.
Refit the facia panel and hinge the control box assembly in the
servicing position as described in Section 14.3 (c).
24. Filling Loop.
Check that the electricity supply to the appliance is turned off.
Drain the central heating circuit as described in Section 15.3 (a).
Remove the two upper screws and lower the facia.
Undo the two screws and slide the filling loop assembly to the
left and remove from the appliance.
Fit the replacement assembly in the reverse order.
Open the valves and fill and re-pressurise the system as
described in Section 12.2.
25. Transformer.
Check that the electricity supply to the appliance is turned off.
Remove the control board as described in Section 15.4 (23).
Pull the transformer from the back of the control board.
Fit the replacement transformer in the reverse order.
21