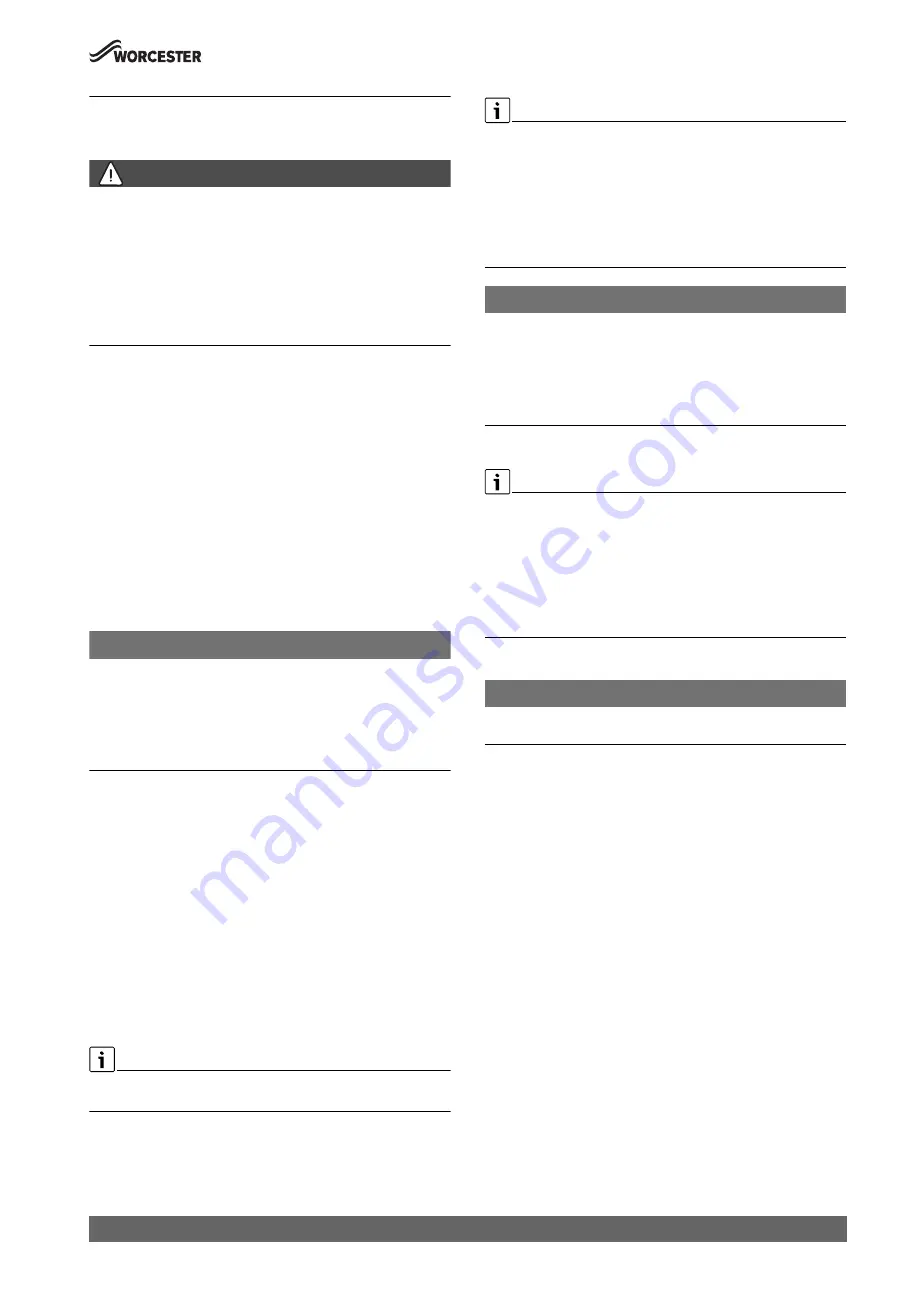
Commissioning
43
Greenstar 4000 – 6 720 891 162 (2020/09)
6
Commissioning
6.1
Pre-Commissioning checks
DANGER
Risk of electric shock!
▶ Isolate electrical components from the power supply (230 V AC)
(fuse, circuit breaker) and secure against unintentional re-
connection before carrying out any work.
Information on safe isolation can be found in the Health and Safety
Executive guidance HSG85.
▶ Check for zero potential before proceeding with work, using test
equipment approved to GS38 to confirm that the electricity supply is
disconnected.
Checks before commissioning:
▶ Check that the service and water pipes are connected correctly.
▶ Check the gas type specified on the identification plate matches that
of the gas supply and that the gas supply is properly purged.
▶ Check that the appliance is filled with water and under pressure (0.8
to 1.7 bar) and that there are no leaks.
▶ Check that the electrical connections of the appliance are correct:
– Mains electrical supply - 230V, 50Hz
– Compliant earth connection
– Correct polarities.
– External equipment and controls are wired in correctly.
▶ Check that the flue is correctly fitted, airtight, free from any
obstruction and the connections are secure.
▶ Check that the condensate pipework is connected properly and that
there are no leaks.
NOTICE
If the appliance is not to be commissioned immediately then, after
successfully completing all of the checks and any rectification work:
▶ Isolate the electricity supply.
▶ Isolate the gas supply.
▶ Close the water shut-off valves to the appliance.
▶ Label appropriately.
6.2
Water treatment
Primary system flushing (Central Heating)
Ensure that the system has been cleaned:
• Following the guidance of BS 7593:
– Code of Practice for treatment of water in hot water central
heating systems.
• Overview available in Pre-installation, Cleaning primary systems
section.
Inhibitor (Central Heating):
Add a suitable inhibitor that is compatible with aluminium (or combined
inhibitor/anti-freeze, if the system is exposed to freezing conditions), to
the heating system in accordance with the DWTA code of practice and
manufacturer‘s guidelines.
The pH value of the system water must be between 6.5 and 8 or the
appliance warranty will be invalidated.
The inhibitor or combined inhibitor/anti-freeze must not cause damage
to the materials within the appliance (aluminium, mild steel, stainless
steel, copper and brass) and any other materials/components within the
system.
▶ Record the date when the inhibitor was added to the system on the
guarantee card.
▶ The concentration level of inhibitor in the system should be checked
every 12 months or sooner if system content is lost.
NOTICE
Sealing agents
Normally the addition of sealing agents to the system water is not
permitted as this can cause problems with deposits left in the heat
exchanger.
▶ In cases where all attempts to find a system micro leak have failed,
Worcester, Bosch Group supports the use of Fernox F4 leak sealer.
6.2.1
Filling the appliance and adding Inhibitor
Before pressurising the system.
The appliance integral expansion vessel is pre-charged to 0.75 bar
(equal to a static head of 7.5m (24.6ft)). A Schrader type valve is fitted
to the expansion vessel to allow for pressure adjustment if required.
▶ If an extra expansion vessel is fitted to the central heating system,
ensure that it is set to the same pressure as the appliance internal
expansion vessel, refer to separate instructions supplied with the
extra expansion vessel.
Filling the system - Sealed systems
NOTICE
▶ Salt based softened water must not be used to fill the central heating
system.
▶ Check drain cocks and manual air vents are closed and all radiator
valves are open. Add a suitable inhibitor or combined inhibitor/anti-
freeze, if the system is exposed to freezing conditions, to the heating
system water in accordance with the manufacturers instructions.
▶ Turn on the water main and open the system valves.
▶ Fill the system to between 1 and 1.5 bar via a WRAS approved filling
loop.
▶ The Automatic Air Vent will release any air trapped in the appliance.
▶ Manually vent all radiators, tighten when completed and check the
system for any leaks and correct if required.
▶ Top up the system pressure if the pressure drops below 1 bar.
▶ Isolate and remove filling loop connections to the system.