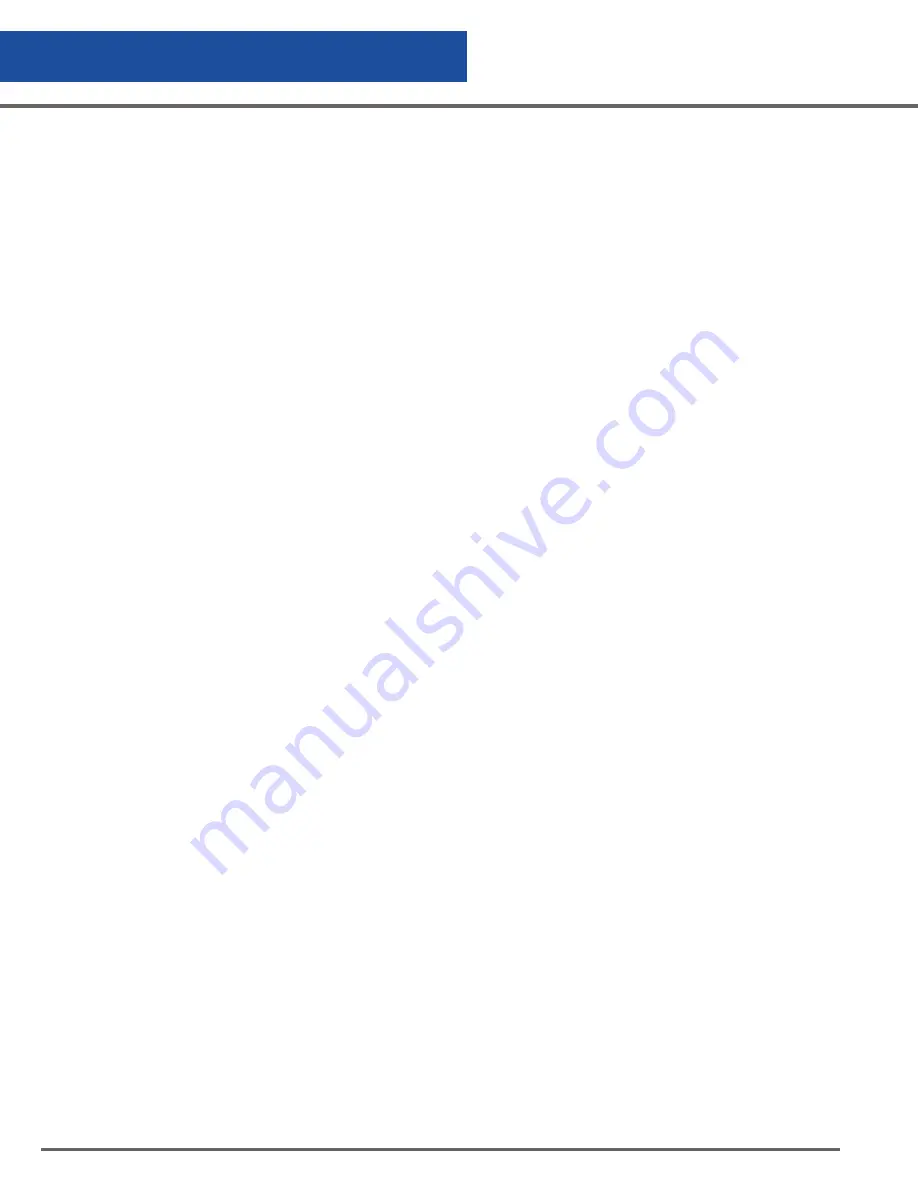
CS200
Control Systems
Table
of Contents
Wiring Diagram .................................................................................................. 31
Installation & Setup .............................................................................................. 32
External Connector Ratings ................................................................................... 34
LED Status Wheel Flash Patterns ............................................................................ 35
Temperature Thermocouple Select ......................................................................... 35
Temperature Calibration ...................................................................................... 35
Test Temperature System ....................................................................................... 36
Test Level Sensors ................................................................................................ 36
Alarms and Error Conditions ................................................................................ 37
System Alarms .................................................................................................... 37
Test Alarms ........................................................................................................ 37
Logging ............................................................................................................. 37
Display Brightness ............................................................................................... 38
Making Adjustments to the CS200 Series Control System Sensor Assembly ............... 38
Removing/Installing the Solenoid Valve ................................................................. 39
Removing/Installing the Controller 10K/24K Units ................................................. 39
Removing/Installing the Thermocouple .................................................................. 40
Removing/Installing the Sensor Probes .................................................................. 40
Making Adjustments to the Level Settings ............................................................... 40
Removing/Installing the Solenoid Valve ................................................................. 41
REPLACEMENT PARTS ......................................................................42
Plumbing Assembly ............................................................................................. 42
Controller Assembly ............................................................................................ 43
TROUBLESHOOTING ........................................................................45
Symptoms ......................................................................................................... 45
Controller Will Not Turn ON ............................................................................... 45
High Liquid Level ................................................................................................ 45
Indicates Low LN
2
Supply ..................................................................................... 46
Indicates Open Sensor ......................................................................................... 46
Temperature Reading 10° to 20° Warm ................................................................. 46
Fill Solenoid Cycles On and Off ............................................................................ 47
Solenoid Makes Excessive Humming Noise ............................................................ 47
Lid Open Alarm .................................................................................................. 47
QCF (Quick Chill Feature) Will Not Operate ......................................................... 47
Auto Defog Feature Will Not Operate .................................................................. 47
Push Buttons Will Not Respond ............................................................................ 48
Liquid Level Readout is Incorrect ........................................................................... 48
Power Failure Alarm ........................................................................................... 48
SERVICE AND MAINTENANCE HISTORY LOG ....................................49
APPENDIX .......................................................................................50
EN Compliance Tables ......................................................................................... 50
EC Declaration of Conformity ............................................................................... 54
Warranty ........................................................................................................... 55
Labels ................................................................................................................ 55
Summary of Contents for CS200
Page 2: ......