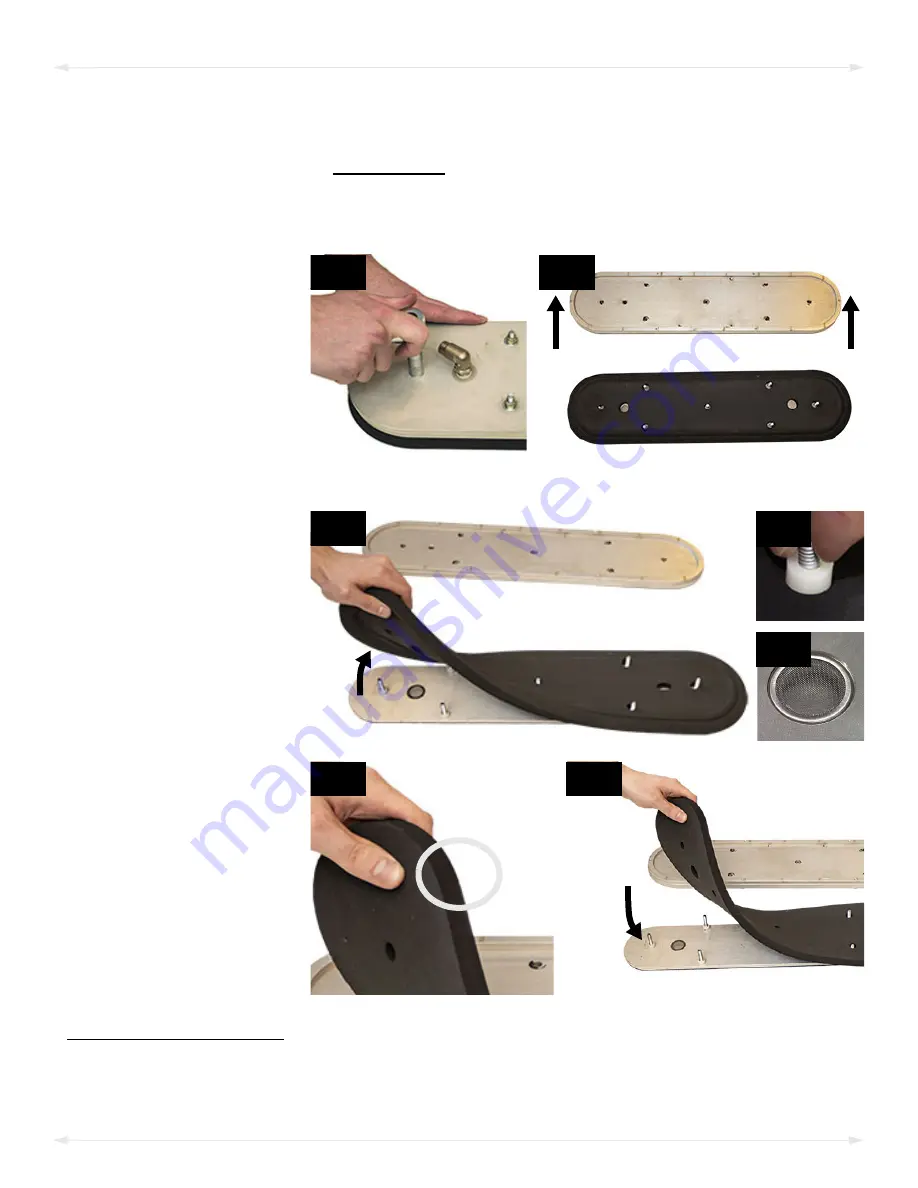
MRTALP4-DC3: #35058
Rev 7.4/12-21
36
T
O
R
EPLACE
P
AD
I
NSERTS
IN
VPFS625 P
ADS
If the vacuum lifter has VPFS625 vacuum pads
(#58383)
, replace its pad inserts
(#49726)
:
Note: The Pad Repair Kit
(#58387)
also includes associated hardware. Instead of setting aside
and reusing the existing hardware as directed below, use the hardware supplied with the kit.
1)
1A
1B
Remove the 1/4-20
lock nuts and washers
that secure the top
plate to the face plate
of the pad assembly
(fig. 1A). Then remove
the top plate (arrows
in fig. 1B).
Note: Set aside the removed hardware.
1
2)
2A
2C
2B
Remove the old pad
insert (fig. 2A). Then
remove the white
spacers (fig. 2B) from
the old insert and set
them aside.
Note: Leave the pad’s
filter screen
(#15630)
in place (fig. 2C).
3)
3A
4A
Inspect the edge of
the new pad insert, to
determine which side
of the insert’s face has
the smoother edge
(circled in fig. 3A).
Note: The difference in
the edge’s smoothness
will be subtle.
4) Install the new pad insert, making sure the smoother edge faces down (fig. 4A).
1..... A pad repair kit
(#58387)
, which includes a replacement pad insert as well as the hardware required to install it, is also available.
MAINTENANCE