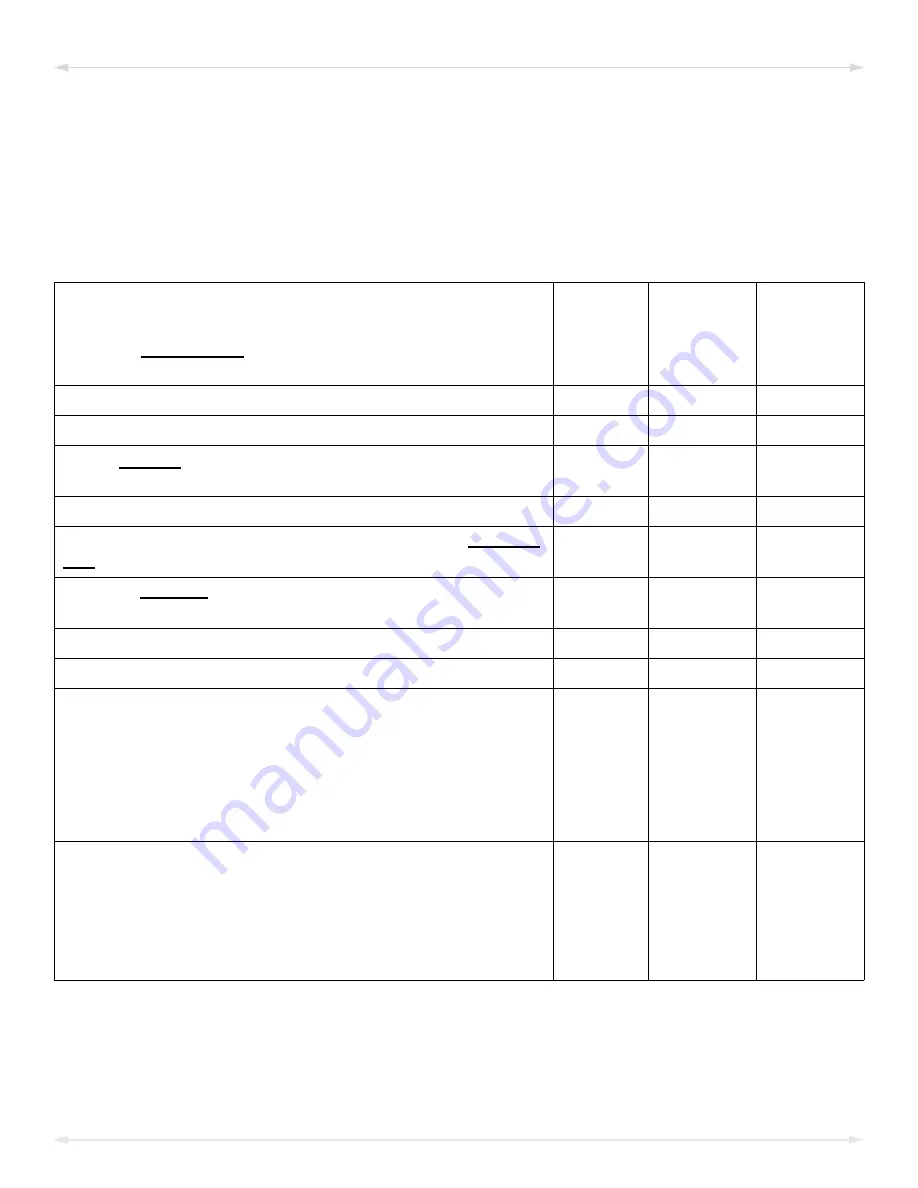
Rev 6.0/11-20
FL1-DC: #35026
19
INSPECTIONS AND TESTS
I
NSPECTION
S
CHEDULE
Perform inspections according to the following frequency schedule. If any fault is found, correct
it and perform the next most frequent inspection before using the vacuum lifter.
Every Lift Frequent
1
1...... The Frequent Inspection is also required whenever the lifter has been out of service for 1 month or more.
(every 20-40 hrs)
Action
Examine vacuum pad for contaminates or damage
(see
).
Examine load surface for contaminates or debris.
Examine controls and indicators for damage.
Check battery for adequate charge (see
Examine lifter’s structure for damage.
Examine vacuum system for damage (including vacuum
pad, fittings and hoses).
Examine air filter for conditions requiring service (see
“A
IR
F
ILTER
M
AINTENANCE
” in
).
Perform
Check for unusual vibrations or noises while operating lifter.
Examine entire lifter for evidence of:
• looseness, excessive wear or excessive corrosion
• deformation, cracks, dents to structural or functional
components
• cuts in vacuum pad or hoses
• any other hazardous conditions
Inspect entire electrical system for damage, wear or
contamination that could be hazardous, in compliance
with all local codes and regulatory standards.
Caution: Use appropriate cleaning methods for each
electrical part, as specified by codes and standards.
Improper cleaning can damage parts.
Note: If a lifter is used less than 1 day in a 2-week period, perform the Periodic Inspection before
using it.
Periodic
2
(every 250-400 hrs)
2...... The Periodic Inspection is also required whenever the lifter has been out of service for 1 year or more. Keep a written record of all Periodic Inspections. If
necessary, return the lifter to WPG or an authorized dealer for repair (see