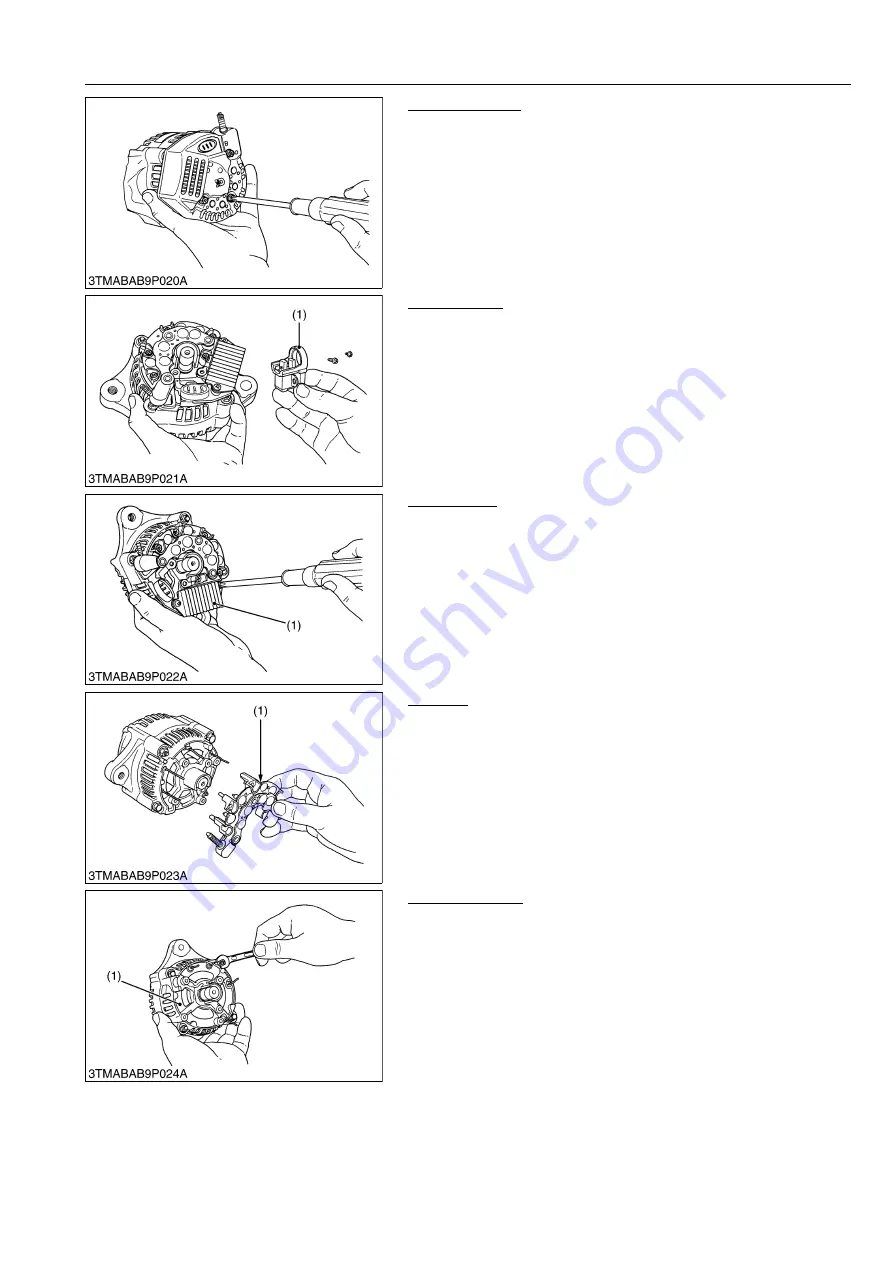
ELECTRICAL SYSTEM
L4100, WSM
9-S23
(EU)
Rear End Cover
1. Unscrew the three rear end cover screws and the
B
terminal
nut, and remove the rear end cover.
WSM000001ELS0024US0
Brush Holder
1. Unscrew the two screws holding the brush holder, and remove
the brush holder (1).
WSM000001ELS0025US0
IC Regulator
1. Unscrew the three screws holding the IC regulator, and remove
the IC regulator (1).
WSM000001ELS0026US0
Rectifier
1. Remove the four screws holding the rectifier and the stator lead
wires.
2. Remove the rectifier (1).
WSM000001ELS0027US0
Rear End Frame
1. Unscrew the two nuts and two screws holding the drive end
frame and the rear end frame.
2. Remove the rear end frame (1).
WSM000001ELS0028US0
(1) Brush Holder
(1) IC Regulator
(1) Rectifier
(1) Rear End Frame
KiSC issued 08, 2012 A
Summary of Contents for Kubota L4100
Page 1: ...L4100 WORKSHOP MANUAL TRACTOR KiSC issued 08 2012 A...
Page 3: ...I INFORMATION KiSC issued 08 2012 A...
Page 9: ...INFORMATION L4100 WSM I 5 EU 9Y1210278INI0002US0 KiSC issued 08 2012 A...
Page 13: ...INFORMATION L4100 WSM I 9 EU Mid mount type ROPS 9Y1210278INI0006US0 KiSC issued 08 2012 A...
Page 14: ...G GENERAL KiSC issued 08 2012 A...
Page 67: ...1 ENGINE KiSC issued 08 2012 A...
Page 130: ...2 CLUTCH KiSC issued 08 2012 A...
Page 160: ...3 TRANSMISSION KiSC issued 08 2012 A...
Page 161: ...CONTENTS 1 STRUCTURE 3 M1 MECHANISM KiSC issued 08 2012 A...
Page 201: ...4 REAR AXLE KiSC issued 08 2012 A...
Page 202: ...CONTENTS 1 STRUCTURE 4 M1 MECHANISM KiSC issued 08 2012 A...
Page 210: ...5 BRAKES KiSC issued 08 2012 A...
Page 211: ...CONTENTS 1 STRUCTURE 5 M1 2 OPERATION 5 M2 MECHANISM KiSC issued 08 2012 A...
Page 224: ...6 FRONT AXLE KiSC issued 08 2012 A...
Page 225: ...CONTENTS 1 STRUCTURE 6 M1 2 FRONT WHEEL ALIGNMENT 6 M2 MECHANISM KiSC issued 08 2012 A...
Page 245: ...7 STEERING KiSC issued 08 2012 A...
Page 264: ...8 HYDRAULIC SYSTEM KiSC issued 08 2012 A...