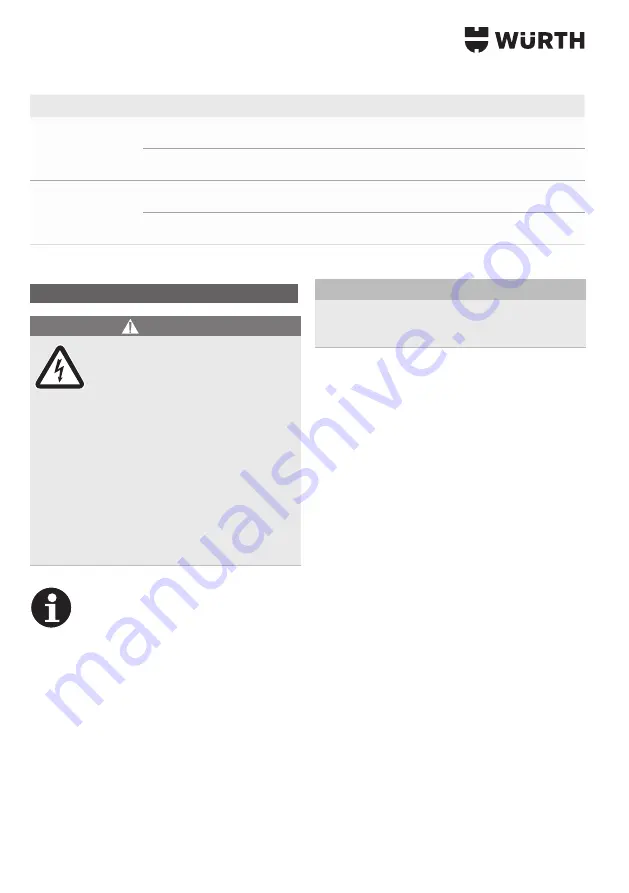
24
Fault
Possible cause
Remedy
Compressor runs
without building up
sufficient pressure.
Condensate drain leaking.
Ensure that the condensate drain
[7]
is closed.
Check the seal of the drain plug, replace as necessary
Non-return valve leaking.
The non-return valve must be repaired by a specialist
workshop.
Air tool does not
receive enough
pressure.
Pressure controller not turned
up high enough.
Turn pressure controller
[15]
up higher.
Hose connectors between com-
pressor and air tool are leaky.
Check the hose connectors, replace damaged parts as
necessary.
Maintenance / care
DANGER!
Before any work on the device:
¾
Switch off the device and unplug.
¾
Wait until the device is at a standstill.
¾
Ensure that the device and all air
tools and accessory parts are depres-
surised.
¾
Allow the device and all air tools and
accessory parts to cool.
After any work on the device:
¾
Start up and check all safety devices.
¾
Ensure that there are no tools or
similar on or in the device.
¾
Advanced maintenance and
repair work as described in this
chapter, must only be carried out by
specialists.
Note
Maintenance and inspections must be
planned and performed according to
the legal regulations dependent on
the set-up and operating mode of the
device.
Supervisory authorities can request the
submission of corresponding documen-
tation.
Attention!
Check the tightening torques of the cylinder head
bolts
on the compressor
[12]
after the first 50 and
250 operating hours (see technical data).
Before each use
▸
Inspect air hoses for damage, replace as neces-
sary.
▸
Check screw connections are tightly seated,
tighten as necessary.
▸
Check the supply cable for damage; if necessary
arrange replacement by an electrician.
▸
Check the oil level of the compressed air
oiler
[19]
, top up with pneumatic oil as neces-
sary.
Daily
▸
Drain the pressure tank condensation at the
condensate drain
[7]
.
Every 50 operating hours
▸
Clean the air filter
[13]
(Fig. VII)
.
▸
Check the compressor oil level at the oil sight
glass
[10]
, replenish the oil as necessary.
▸
Drain the condensation water at the filter pressure
reducer
[20]
.
▸
Clean or replace the air filter in the filter pressure
reducer
(Fig. VIII)
.
▸
Unscrew the belt guard
[1]
and check the V-belt,
if necessary retighten or replace
(Fig. IX)
.
— To adjust the belt tension, loosen the four screws
at the base of the motor and move the motor.
— Retighten the screws at the base of the motor.
—
Refit the belt guard.
Summary of Contents for 0701 225 0
Page 3: ...3 I 6 14 5 4 3 2 13 11 10 9 12 8 7 1 15 16 17 18 19 20...
Page 4: ...4 II III IV V VI VII VIII IX 6 19 13 1...
Page 126: ...126 GR Adolf W rth GmbH Co KG 3 1...
Page 127: ...127 a b c a b c d e a b c d e f g...
Page 128: ...128 a b c d e f g a...
Page 129: ...129...
Page 132: ...132 3 II 6 III I 7 I 10 11 IV 19 4 RCD 30 mA 2 3 3 14...
Page 133: ...133 15 3 16 6 18 17 VI 3 7 2 2 10...
Page 134: ...134 7 15 50 250 12 19 7 50 13 VII 10 20 VIII 1 IX...
Page 214: ...214 BG Adolf W rth GmbH Co KG 3 1...
Page 215: ...215 a b c a b c d e a b c d e f g...
Page 216: ...216 a b c d e f g a...
Page 217: ...217...
Page 220: ...220 3 II 6 III I 7 I 10 11 IV 19 4 RCD 30 mA...
Page 221: ...221 2 3 3 14 15 3 16 6 18 17 VI 3 7 2 2 10...
Page 222: ...222 7 15 50 250 12 19 7 50 13 VII 10 20 VIII 1 IX...
Page 258: ...258 RU Adolf W rth GmbH Co KG 3 1...
Page 259: ...259 a b c a b c d e a b c d e f g...
Page 260: ...260 a b c d e f g a...
Page 261: ...261...
Page 264: ...264 3 II 6 III I 7 I 10 11 IV 19 4 RCD 30...
Page 265: ...265 2 3 3 14 15 3 16 6 18 17 VI 3 7 2 2 10...
Page 266: ...266 7 15 50 250 12 19 7 50 13 VII 10 20 VIII 1 IX...
Page 291: ......