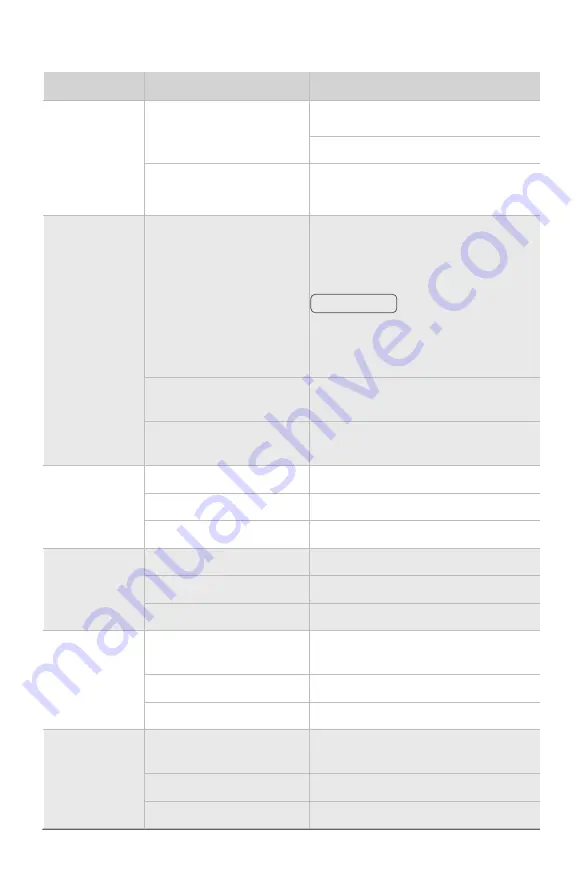
XAG AUSTRALIA
54
Button
Operation
Description
Pause/Resume
Short Press
(Calibration Mode) Next
Hover the Aircraft
Long Press
Resume Task
Fn
Long Press
Enter/Exit Mapping Mode:
Short Press L1:
Mark current position
Short Press L2:
Undo previous Mark
In Mapping Mode, remote controller can only
be used for mapping rather than piloting the
aircraft.
Long Press
(Fn + Pause/Resume)
Return-to-Land (RTL)
Long Press
(Fn + Both stick to Bottom Left)
Enable – Calibration Mode
F1 Knob
Twiddle
(Auxiliary Mode) Adjust Route spacing
Short Press
Enable – Obstacle Avoidance
Long Press
Disable – Obstacle Avoidance
F2 Knob
Twiddle
(Auxiliary Mode) Adjust Route direction
Short Press
Disable – Terrain Following
Long Press
Enable – Terrain Following
F3 Knob
Twiddle
Spraying:
Adjust Droplet Size
Spreading:
Adjust Feed Rate
Short Press
Toggle One-Nozzle/Two-Nozzle Spraying
Long Press
Toggle Constant/Variable Rate Spraying
F4 Knob
Twiddle
Spraying:
Adjust Flow Rate
Spreading:
Adjust Dosage Rate
Short Press
Disable – Spraying / Spreading
Long Press
Enable – Spraying / Spreading
ℹ
IMPORTANT
Button Functions
Summary of Contents for P100 Pro
Page 1: ...XAG P100 Pro Pilot s Operating Handbook EN Version AU V1 0 Type 3WWDZ 50AH...
Page 2: ......
Page 26: ...XAG AUSTRALIA 26 Wiring Guide...
Page 27: ...27 XAG AUSTRALIA...
Page 61: ...61 XAG AUSTRALIA...
Page 79: ...79 XAG AUSTRALIA 01 02 03 04 05 XAG One APP User Interface APP UI Accounts Menu...