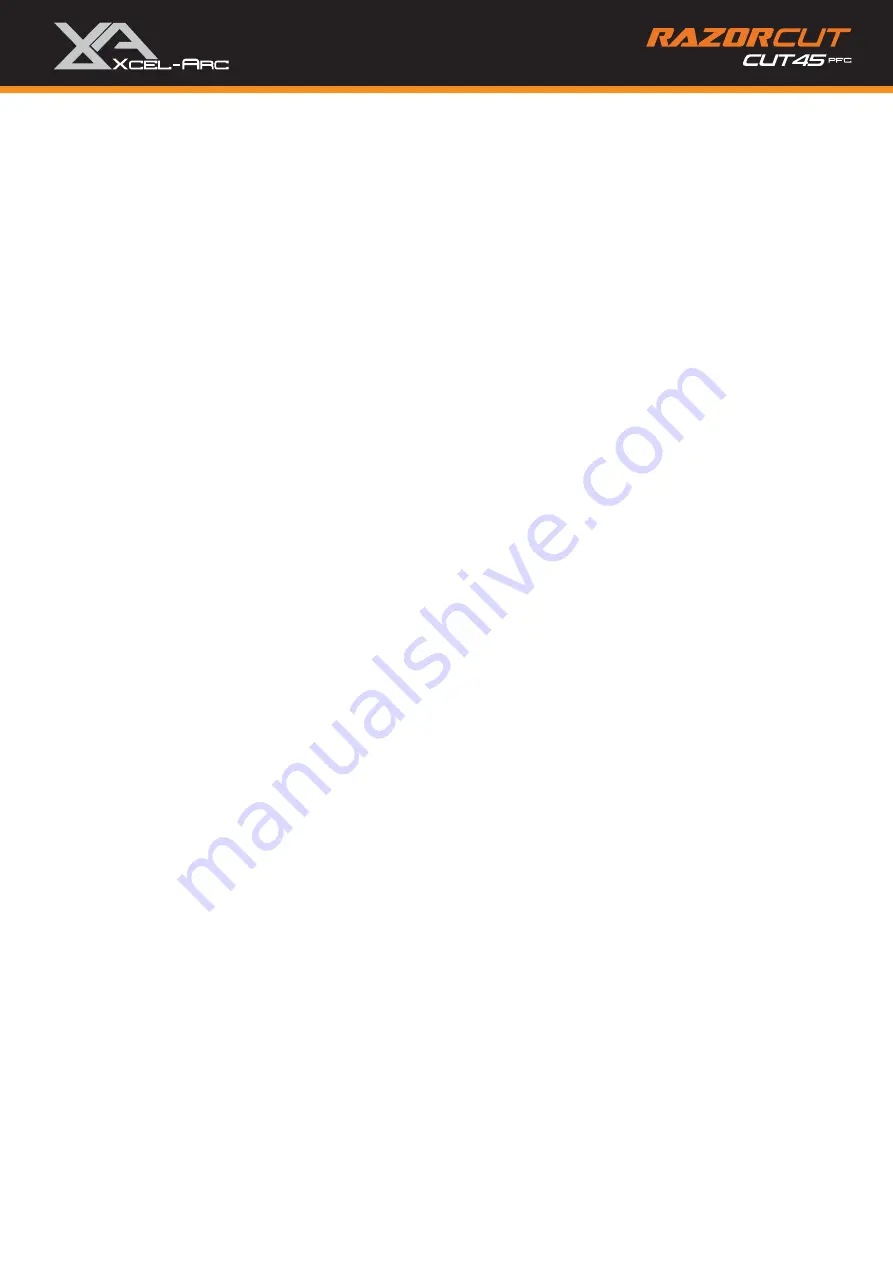
6
CAUTION
1. Working Environment.
1.1
The environment in which this Plasma Cutter equipment is installed must be free of grinding dust,
corrosive chemicals, flammable gas or materials etc, and at no more than maximum of 80% humidity.
1.2
When using the machine outdoors protect the machine from direct sun light, rain water and snow etc;
the temperature of working environment should be maintained within -10°C to +40°C.
1.3
Keep this equipment 30cm distant from the wall.
1.4
Ensure the working environment is well ventilated.
2. Safety Tips.
2.1
Ventilation
This equipment is small-sized, compact in structure, and of excellent performance in amperage output.
The fan is used to dissipate heat generated by this equipment during the welding operation.
Important:
Maintain good ventilation of the louvers of this equipment. The minimum distance between
this equipment and any other objects in or near the working area should be 30 cm. Good ventilation is
of critical importance for the normal performance and service life of this equipment.
2.2
Thermal Overload protection.
Should the machine be used to an excessive level, or in high temperature environment, poorly
ventilated area or if the fan malfunctions the Thermal Overload Switch will be activated and the
machine will cease to operate. Under this circumstance, leave the machine switched on to keep the
built-in fan working to bring down the temperature inside the equipment. The machine will be ready for
use again when the internal temperature reaches safe level.
2.3
Over-Voltage Supply
Regarding the power supply voltage range of the machine, please refer to “Main parameter” table.
This equipment is of automatic voltage compensation, which enables the maintaining of the voltage
range within the given range. In case that the voltage of input power supply amperage exceeds the
stipulated value, it is possible to cause damage to the components of this equipment. Please ensure
your primary power supply is correct.
2.4
Do not come into contact with the output terminals while the machine is in operation. An electric shock
may possibly occur.
MAINTENANCE
Exposure to extremely dusty, damp, or corrosive air is damaging to this plasma cutter. In order to prevent
any possible failure or fault of this welding equipment, clean the dust at regular intervals with clean and dry
compressed air of required pressure.
Please note that:
lack of maintenance can result in the cancellation of the warranty; the warranty of this
plasma cuting equipment will be void if the machine has been modified, an attempt to take apart the
machine or open the factory-made sealing of the machine without the consent of an authorized
representative of the manufacturer.
TROUBLE SHOOTING
Caution: Only qualified technicians are authorized to undertake the repair of this Plasma cutter equipment.
For your safety and to avoid Electrical Shock, please observe all safety notes and precautions
detailed in this manual.
Note:
• Our equipment as described in this manual conforms to all applicable rules and regulations of the
‘LowVoltage Directive’ (European Council Directive 73/23/EEC) as set out and amended by Council
Directive 93/68/EEC) and to the National legislation for the enforcement of this Directive.
• Our equipment as described in this manual conforms to all applicable rules and regulations of the
European Council Directive 89/336/EEC, (EMC Directive) and to the National legislation for he
enforcement of this Directive.