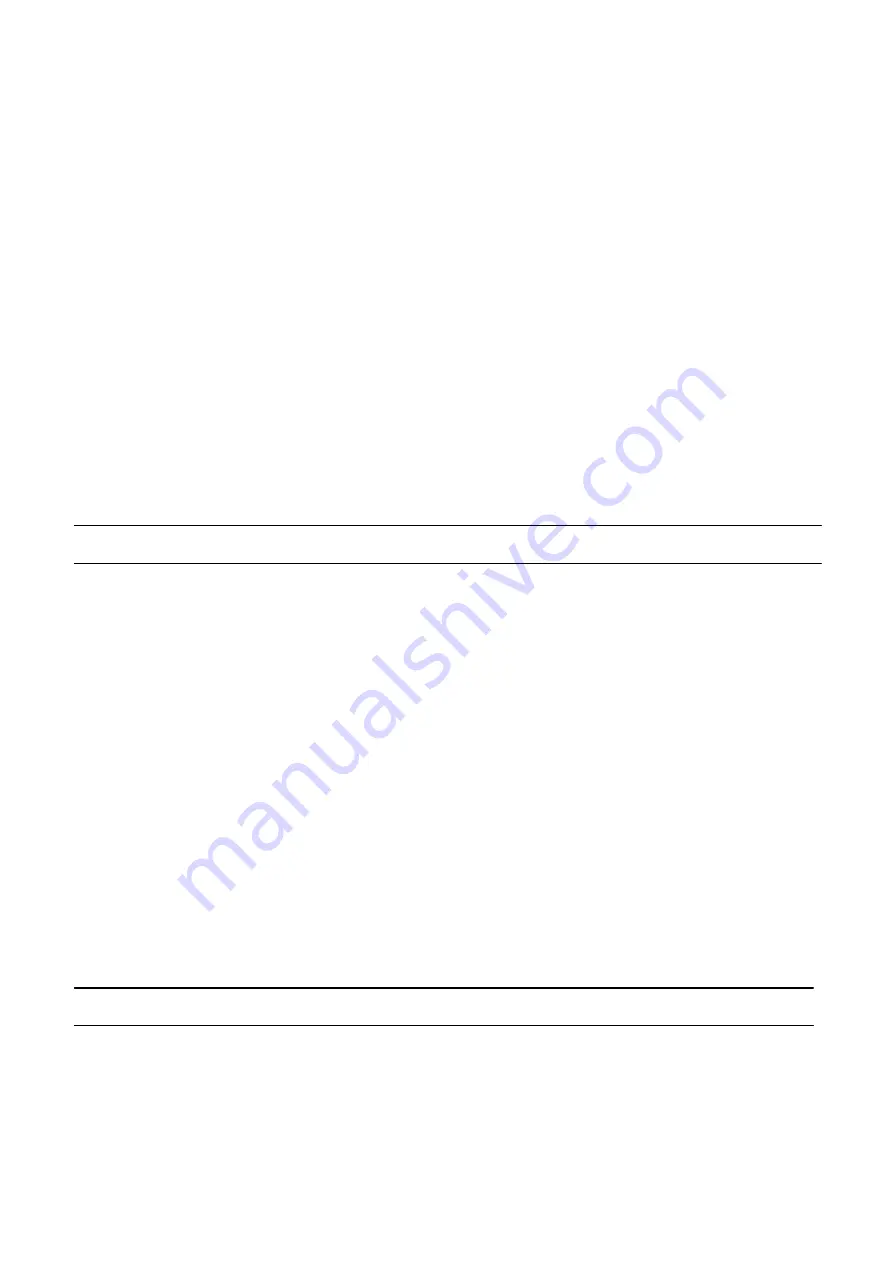
11
(2) Mount the core bit shank on the main body in the same manner as in mounting the drill bit and the
bull point.
(Fig. 11)
(3) Fit in the drill bit by aligning its screw portion with the core bit tip. When the position of the
concave is shifted by turning the turn drill bit clockwise, the drill bit never slips off even when the
drill is used in a downward direction.
(Fig. 12)
2. Drilling holes
(1) Connect the plug to the power source.
(2) By straightly and gently pressing dill bit to the wall or floor surface, the entire surface of the core
bit tip attains contact to start the hole drilling job.
(Fig. 13)
(3) When the hole depth reaches approximately 5mm, the hole position can be determined. Then
remove the dill bit from the core bit and continue the hole drilling job.
CAUTION:
When removing the dill bit, always disconnect the plug from the receptacle.
3. How to dismount the core bit
○
By holding the rotary hammer (with the core bit inserted) in an upward position, drive the rotary
hammer to repeat impact operation two or three times, whereby the screw is loosened and the rotary
hammer becomes ready for disassembly.
(Fig. 14)
○
Remove the core bit shank from the rotary hammer, hold the core bit with one hand, and strongly
strike the head of the SDS max shank portion of the core bit shank with a manual hammer two or
three times, whereby the round head screw is loosened and the rotary hammer is ready for
disassembly.
(Fig. 15)
HOW TO REPLACE GREASE
Low viscosity grease is applied to this rotary hammer so that it can be used for a long period without
replacing the grease. Please contact the nearest service center for grease replacement when any grease
is leaking from loosened screw.
Further use of the rotary hammer with lock off grease will cause the machine to seize up reduce the
service life.
CAUTION:
A special grease is used with this machine, therefore, the normal performance of the machine may be
badly affected by use of other grease. Please be sure to let one of our service agents undertake
replacement of the grease.
When you have to replacement the grease by yourself, please following the order:
CAUTION:
Before replenishing the grease, turn the power off and pull out the power plug.
(1) Remove the oil tank cover and wipe off the grease inside.
(Fig. 16)
(2) Supply 30g of XINPU Electric Hammer Grease (Standard accessory, contained in tube) to the
crank case.
(3) After replenishing the grease, install the oil tank cover securely.
NOTE:
The XINPU Electric Hammer Grease is of the low viscosity type. If necessary purchase from an
XINPU Authorized Service Center.
MAINTENANCE AND INSPECTION
1. Inspecting the tool
Since use of a dull tool will degrade efficiency and cause possible motor malfunction, sharpen or
replace the tool as soon as abrasion is noted.
2. Inspecting the mounting screws
Regularly inspect all mounting screws and ensure that they are properly tightened. Should any of the
screws be loose, retighten them immediately. Failure to do so could result in serious hazard.
Summary of Contents for XP-R48VA
Page 2: ...2 1 2 3 4 5 6 7 8 9 10 11 12 13 14 15 16 ...
Page 13: ...13 ...
Page 14: ...14 ...
Page 15: ...15 ...