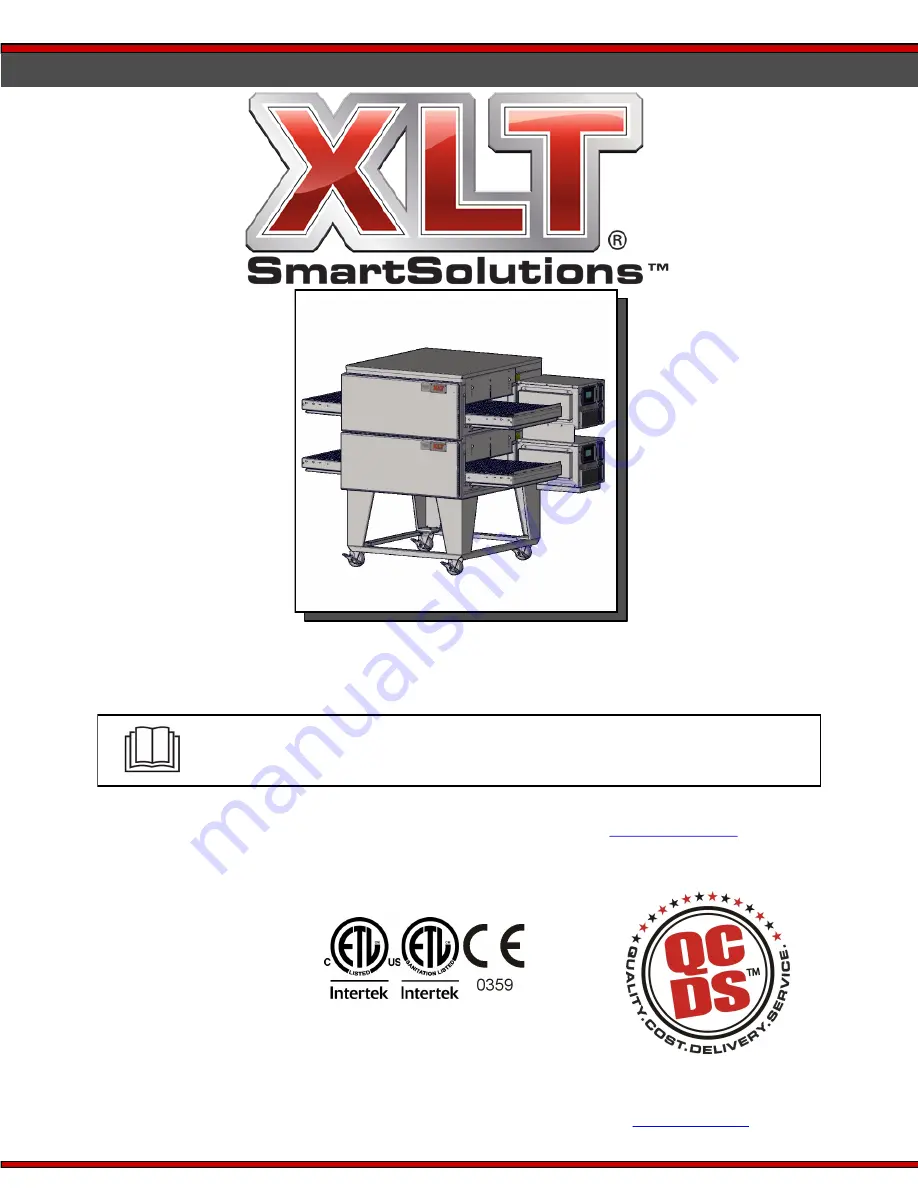
XLT Ovens
PO Box 9090
Wichita, Kansas 67277
US: 888-443-2751 FAX: 316-943-2769 INTL: 316-943-2751 WEB:
RD 9005C
SWA
06/11/2020
For use with the following XLT Radiant Oven Versions:
Standard (S)
A
World (W)
A
2000887
Current versions of this manual, Rough-In Specifications, Parts & Service Manual, Architectural Drawings,
& a list of International Authorized Distributors are available at:
XLT Radiant Oven
Installation & Operation Manual
Read This Manual Before Using This Appliance.
Original Instructions