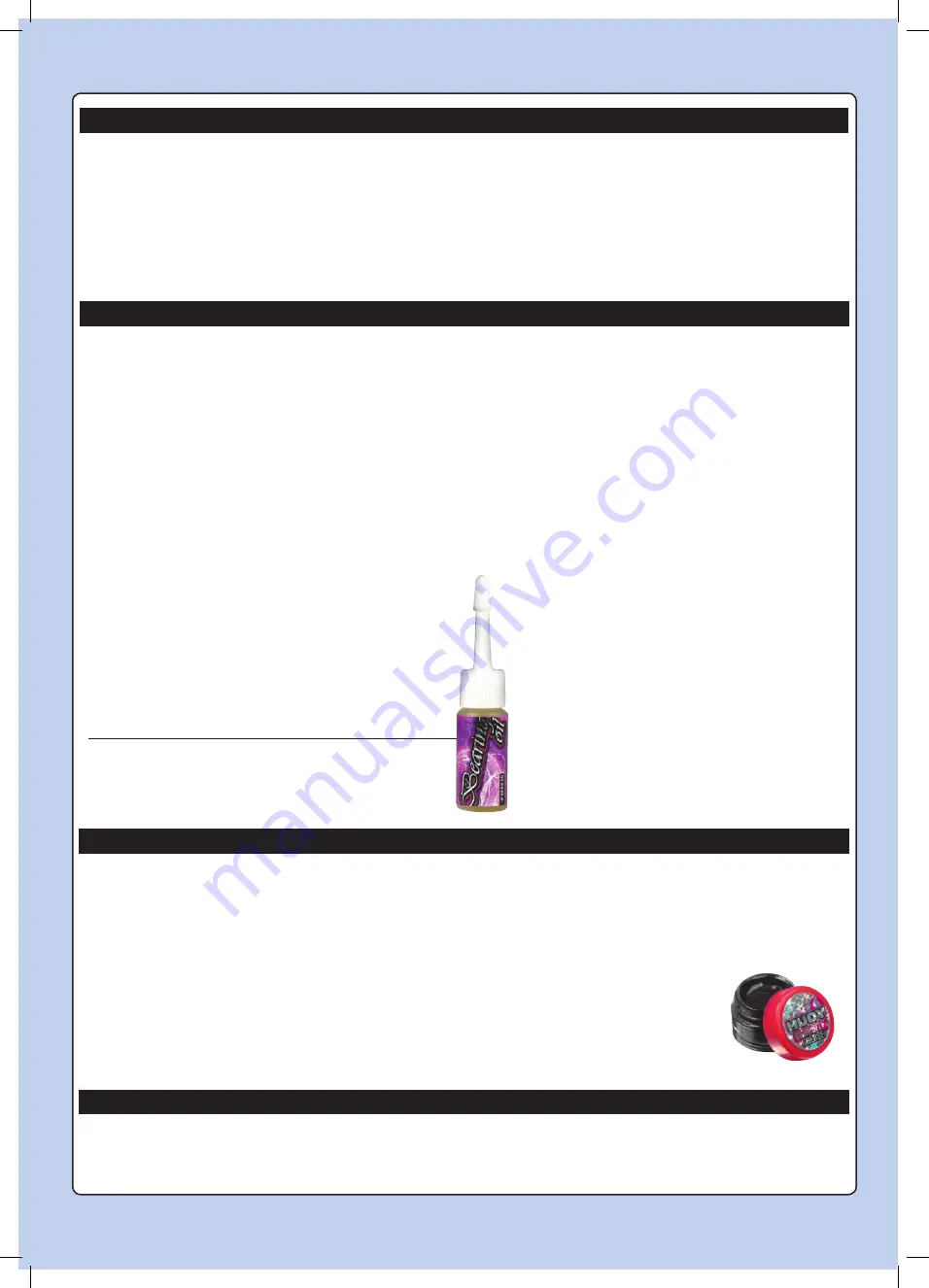
38
RECOMMENDED PRODUCTS
• Use #106230 HUDY Bearing Oil to lubricate the bearings.
SUSPENSION & DRIVETRAIN MAINTENANCE
• Check suspension for free movement during building and operation, and especially after running
and if you have crashed the car. If the suspension does not move freely, use the appropriate HUDY
Arm Reamer to clean and resize the holes of the suspension arms.
• Regularly check the drive shaft pins and if they show any wear must be immediately replaced
by new pins. If the car is run with worn pins, excessive wear on the diff outdrives will result. The
#106000 HUDY Drive Pin Replacement Tool (for 3mm Pins) is a compact, rugged multi-use tool
set for replacing 3mm drive pins in drive shafts. Use the HUDY replacement drive shaft pins 3x12
(#106051).
• Regularly inspect and replace the pins that connect the wheel drive shafts with wheel axles. Use
HUDY Graphite Grease to lubricate the drive shaft connecting joints and the diff gears.
HUDY SPRING STEEL™
The HUDY Spring Steel™ used in the car is the strongest and most durable steel material on the
RC market. While items made from HUDY Spring Steel™ are still subject to wear, the lifespan is
considerably longer than any other material. As parts made from HUDY Spring Steel™ wear, the
HUDY #106230
HUDY #106210
MAINTENANCE
• For club racing, it is recommended to check the shocks for air inside before each race and only re-fill
and bleed them if necessary. Before each race day, make sure you take the spring off of each shock,
hold it up to your ear, and quickly compress the shock rod fully into the body while listening for any
air making a “whistling” or “squishy” sound as it passes through the piston holes. If you hear any
air, refill and bleed your shocks. For high-competition racing, it is recommended that the shocks be
re-filled and bled before a large event.
➊
Remove the seals on both sides of the bearing (if present). If the seals bend a little and you can see
a kink, carefully flatten the kink out by hand.
➋
Spray the seals with motor cleaner and blow dry with compressed air.
➌
Spray the bearing on both sides with motor cleaner.
➍
Spin the bearing while it is still wet to dislodge any particles with the cleaner.
➎
Spray the bearing on both sides again.
If you spin test the bearing after you have re-oiled and sealed it, it will not spin freely for an extended
period of time. The lightest of oils may allow it to spin for 1-2 seconds. This is normal and once you
have mounted the bearings in the car again, the drive train will spin freely.
Make sure you use a motor cleaner that does not leave a residue after it dries as this may cause drag
and wear in the bearings.
SHOCK MAINTENANCE
The most important maintenance task for keeping consistent shock performance is refilling and bleeding them correctly. If built correctly, it will not be necessary to re-build them often. Replacing warped/hard
o-rings, scarred piston rods, or shaved/split/loose composite upper and lower ball joints are also important.
BEARING MAINTENANCE
Ball-bearings in an off-road car must be properly maintained for smooth operation and long lifespan.
The XB2 ball-bearings are degreased and are lubricated with HUDY Bearing Oil. The following procedures are recommended to clean all of the bearings in your off-road car. For high-competition racing, we
recommended doing this every 3-4 weeks, or before a major race.
• If building or pairing new shocks, always make sure they are the same length using a shock
length measuring tool and adjust the lower ball joints as needed.
• During regular shock operation, oil naturally gets on the shock shaft and drop-by-drop slightly
gets out of the shock body. Shocks should be inspected regularly after each race, and oil replaced
as required.
➏
Blow both sides of the bearing dry with compressed air to make sure particles come out.
➐
Hold the inner part of the bearing with my left thumb/forefinger and spin it to make sure it
spins free without any abnormal vibrations or sounds.
➑
Place one drop of bearing oil into each side of the bearing.
➒
Replace both seals at the same time by lining them up on each side of the bearing and
lightly pressing them in all the way around the bearings circumference with your thumb and
forefinger. Do not press too hard or use any type of tool, such as a wrench tip, to push the
blue seals in as they will push in too far, bend and cause drag.
• Pivot balls and ball-joints will naturally wear for some time and will generate play. If there
is too much play the pivot balls and ball joints need to be replaced.
• If the car is run in wet conditions, apply WD-40® on all drivetrain parts before the run. After
the run, clean and dry the parts again.
brown color will fade (get lighter) but it will not affect the strength of the material. The brown
color is only a surface treatment and if the brown color will wear the durability of the part
will be still strong.
XT2 SET-UP SHEET VER. 1 ©XRAY 2016
OUT
FRONT TOE
°
UPPER
SHOCK POSITION
FRONT
REAR
1
2
3
2
1
LONGER BUSHINGS
UP
DOWN
SHIM
mm
SHIM
mm
DRIVE SHAFT
CVD
ECS
SHIM
mm
STEERING BLOCK
MEDIUM
HARD
REAR UPRIGHT
MEDIUM
HARD
ALU
0.5°
1°
0.5°
1°
ROLL CENTER
ECCENTRIC BUSHINGS
IN
REAR TOE
°
CASTER
UPPER DECK
MEDIUM
HARD
BATTERY STRAP
COMPOSITE
GRAPHITE
ROLL CENTER
HOLDER
COMPOSITE
ALU
ROLL CENTER
HOLDER
MEDIUM
HARD
ALU
IN FRONT OF ARM
WHEELBASE SHIM
0mm
1mm
2
3
1
2 3
1
LOWER SHOCK POSITION
LOWER SHOCK POSITION
CAMBER LINK
LOCATION
1
2
3
3
2
1
APPLIED
APPLIED
SHOCKS
ELECTRONICS LAYOUT
ELECTRONICS
TIRES
ANTI ROLL BARS
GEARING
cSt
cSt
ø1.7mm
ø1.6mm
SPRINGS
OIL
REBOUND
%
%
PISTONS
ø1.3mm
ø1.4mm
ø1.2mm
mm
mm
ø
ø
HOLES
HOLES
HOLES
HOLES
6
3
2
HOLES
HOLES
HOLES
6
3
2
HOLES
MOTOR POSITION
REAR
FRONT
MIDDLE
REAR
FRONT
MIDDLE
RIGHT
LEFT
BATTERY POSITION
TRANSMISSION
BALL DIFF
GEAR DIFF
DIFFERENTIAL
STEEL
COMPOSITE
SATELITE GEARS
ADJUSTMENT
SLIPPER
TYPE
INSERTS
WHEELS
RACE
TRACK
NAME
DATE
LAPS
BEST LAP TIME
FINAL POSITION
sec
PINION
SPUR GEAR
T
T
THICKNESS
MOTOR
SPEEDO
BATTERIES
QUALIFYING POSITION
OIL
cSt
mm
1
2
mm
mm
DOWNSTOP SHIM
mm
DOWNSTOP SHIM
mm
SHOCK TOWER
COMPOSITE
GRAPHITE
COMPOSITE
GRAPHITE
BODY
LIGHT
OTHER
STANDARD
ROLL CENTER
ROLL
CENTER
RIDE HEIGHT
#107721 GAUGE
RIDE HEIGHT
mm
RIDE HEIGHT
mm
REAR CAMBER
°
-
CHASSIS FLEX
SCREW USED
SCREW NOT USED
MEDIUM
HARD
CHASSIS BRACE
STANDARD
LOW PROFILE
SERVO WEIGHT
COMPOSITE
ALU
ARM MOUNT
BRASS
BUMP STEER SHIM
mm
LENGTH
mm
LENGTH
mm
UPSTOP SHIM
mm
UPSTOP SHIM
mm
CASTER BLOCK
MEDIUM
HARD
BALANCE
g
BALANCE
g
BALL JOINT
KIT
KIT
KICK-UP ANGLE
KIT 26° 29°
23°
STEERING BUMP STEER
SCREW
YES
NO
MOTOR MOUNT BRACE SCREW
UPPER
BRACE
SCREW
INSERT UNDER PISTON
INSERT UNDER PISTON
INSERT ABOVE COLLAR
INSERT ABOVE COLLAR
EXTENSION
0 SLOTS
1 SLOT
2 SLOTS
SHIMS
mm
LEFT = RIGHT
ACKERMANN
SIZE
TIGHT
OPEN
TRACTION
SURFACE
SMOOTH
MEDIUM
MEDIUM
MEDIUM
BUMPY
TYPE
CARPET
ASTRO
CONDITION
BLUE GROOVE
HARD PACKED
DRY
DUSTY
LOAMY
WET
CLAY
TRACK
VERY-LOW
VERY-HIGH
CASTER BUSHINGS
0°
2.5°
5°
STEERING PLATE
COMPOSITE
ALU
STEERING ARMS
COMPOSITE
ALU
BUMP STEER SHIM
mm
LEFT = RIGHT
....................................................................................
..................................................................
OTHER
OTHER
OTHER
SHIMS
mm
MEDIUM
HARD
REAR ARM
GRAPHITE
FRONT CAMBER
°
-
MEDIUM
HARD
FRONT ARM
GRAPHITE
OFFSET
SLOTS
UPPER BRACE
KIT
OTHER
IN FRONT OF ARM
WHEELBASE SHIM
mm
ALU
CHASSIS
OTHER
SIDE BRACE
GRAPHITE
SIDE GUARD
MEDIUM
HARD
OTHER
OTHER
OFFSET
SLOTS
HIGH
STANDARD
NONE
WING
HIGH
/mm
FLEX LINKAGE
YES
NO
SUSPENSION HOLDERS
ALU
BRASS
ALU
BRASS
RR
RF
Summary of Contents for XT2
Page 1: ......