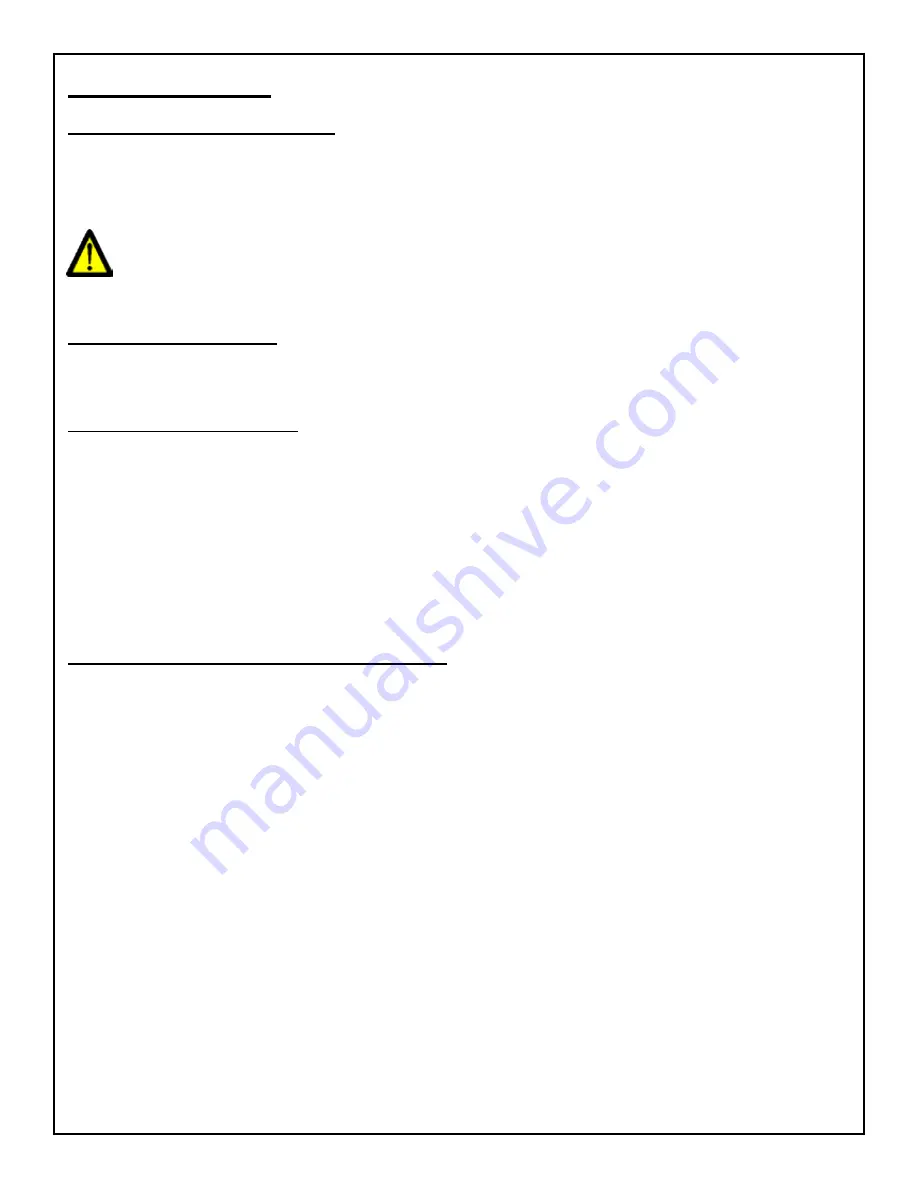
6
Machine Set-Up
Checking Oil Levels and Filters
Check oil levels prior to starting engine.
Do not screw dip stick in to check oil
. Refer to engine owner’s
manual for the proper procedure. DO NOT OVERFILL OIL LEVEL; to do so may cause damage to the
engine and may elevate harmful emissions. Use 10W30 oil. Always check oil daily before using the machine
(see “Daily Maintenance”).
Be sure the carburetor air
filter
is free of dust, oil, etc. Dirty
filters
are the most frequent cause of
elevated toxic emissions.
Check recoil dust filte
r. Clean or replace if necessary. See the instructions in the engine owner’s manual.
Adjusting Handle Height
The machine is equipped with an adjustable handle for comfort and use. Most
find
it necessary to adjust the
handle to “belt height” for optimum control. A 9/16 wrench is used to loosen and tighten the pivot points.
Installing the Fuel Cylinder
1. Take machine to well ventilated area.
2.
Check cylinder for overfill (see “Refilling Propane Fuel Cylinder”).
3.
Place
cylinder on the machine in tank holding area and secure the strap.
4. Connect fuel cylinder to the machine using the “Rego” connection. Tighten hand tight. Do not use a
wrench or pliers or cross thread the Rego connection.
5. Open the service valve slowly. Be alert for the odor of propane that may indicate a leak.
6. To remove the cylinder, reverse the procedure.
Installing or Removing Pad Driver and Pads
Consult an authorized distributor to assist you in selecting the correct pad for your specific needs.
Pad Driver Installation:
1. Tilt machine on the right side.
2.
Place
pad driver on drive shaft and spin pad driver clockwise to install.
Pad Removal & Installation:
1. Tilt machine back on rear caster or service position.
2. Remove center-lock from pad driver.
3. Center new pad on pad driver and secure with center-lock ring.
Pad Driver Removal:
1. Apply downward pressure on bell of machine deck.
2. Use ¾” open end wrench on top of drive shaft exposed on top of deck.
3. Strike the wrench with a rubber mallet to break loose the shaft from the pad driver.
(Counterclockwise)
4. Remove pad driver by spinning it off counterclockwise.
Summary of Contents for Genie Presto Pro
Page 16: ......