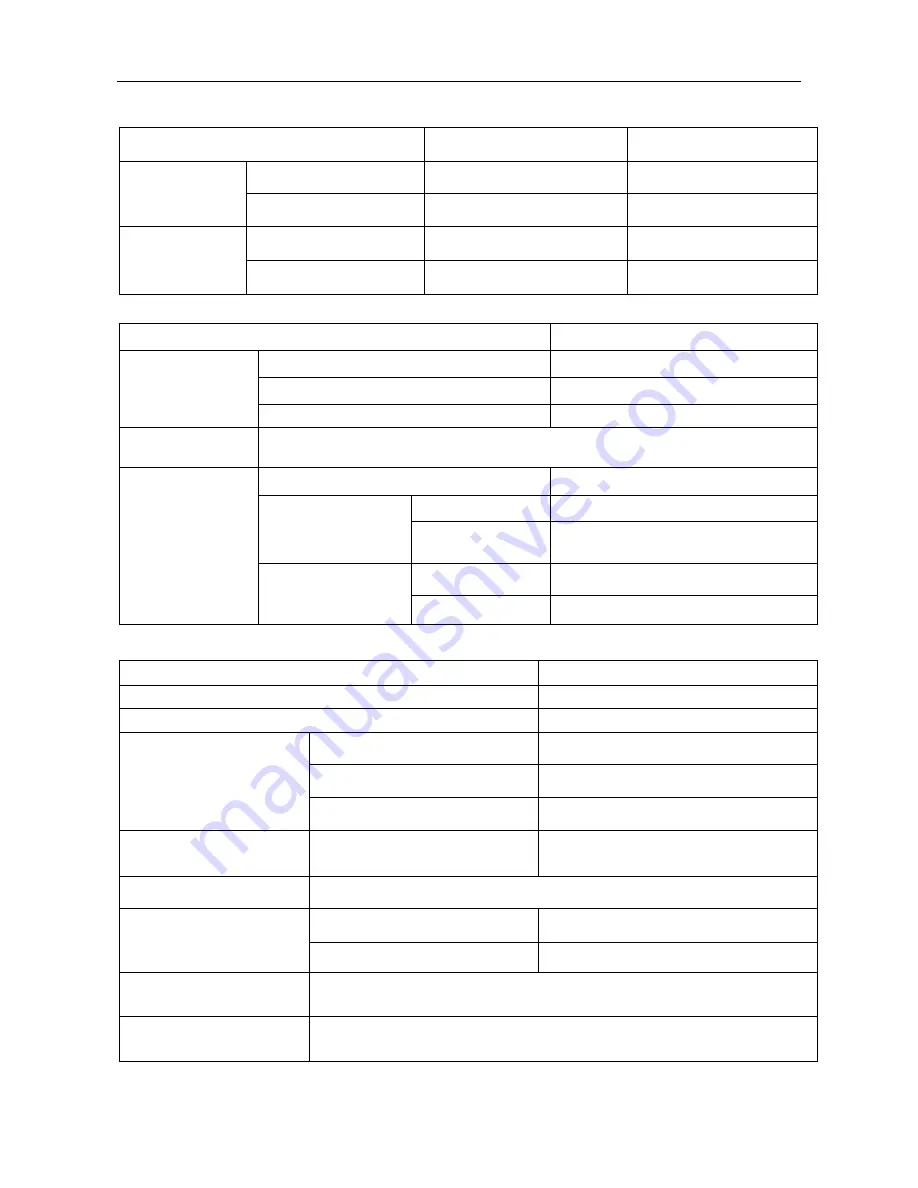
1. SERVICE INFORMATION
1-8
Brake System
Item
Standard Service
Limit
Front brake
Brake disc thickness
17mm
16mm
Brake Pedal Play
0mm
Rear brake
Brake disc thickness
17mm
16mm
Battery
、
Charging System
Item
Standard
Model
Permanent magnet AC type
Output
3- phase AC
AC magneto
Motor
Charging coil Resistance (20
℃
)
0.2-0.3
Ω
Rectifier Three-phase
annular
rectification, Silicon controlled
parallel-connected regulated voltage
Capacity
12V36Ah
Fully charged
12.8V
Terminal point
voltage
Insufficient
charge
<11.8V
Standard 0.9A/5~10H
Battery
Charging
current/time
Quick
4A/1H
Ignition system
Item
Standard
Ignition(Carburetor)
CDI ignition
Ignition(EFI)
ECU ignition
Type
DPR7EA-9(NGK)
Optional DR8EA,
D7RTC
Spark Plug
Spark plug gap
0.8-0.9mm
Ignition
timing(Carburetor)
Max. advanced angle
32
°
CA
Ignition timing(EFI)
BTDC10ºCA 1500r/min
Ignition Above
200V
Peak voltage
Pulse Generator
2V
Starter Relay Coil
Resistance
3
Ω
-5
Ω
Secondary Starter Relay
Coil Resistance
90
Ω
-100
Ω
Summary of Contents for XY500UTV
Page 1: ......
Page 2: ...Service Manual XY500UTV XY500LUTV XY500UE XY500UEL 4 4 ZHEJIANG XINYANG INDUSTRY CO LTD ...
Page 16: ...1 SERVICE INFORMATION 1 13 Cables Pipes Cable Routing 1 ...
Page 17: ...1 SERVICE INFORMATION 1 14 ...
Page 18: ...1 SERVICE INFORMATION 1 15 Carburetor Condition 1 ...
Page 19: ...1 SERVICE INFORMATION 1 16 Carburetor Condition EFI Condition ...
Page 20: ...1 SERVICE INFORMATION 1 17 Carburetor Condition 1 ...
Page 21: ...1 SERVICE INFORMATION 1 18 ...
Page 41: ...2 VEHICLE BODY MUFFLER 2 20 Description of visible parts ...
Page 44: ......
Page 66: ...4 COOLING AND LUBRICATIING SYSTEM 4 2 Cooling System Illustration 4 ...
Page 114: ...6 ENGINE REMOVAL INSPECTION INSTALLATION 6 29 Primary and Secondary Sheave 6 ...
Page 225: ......