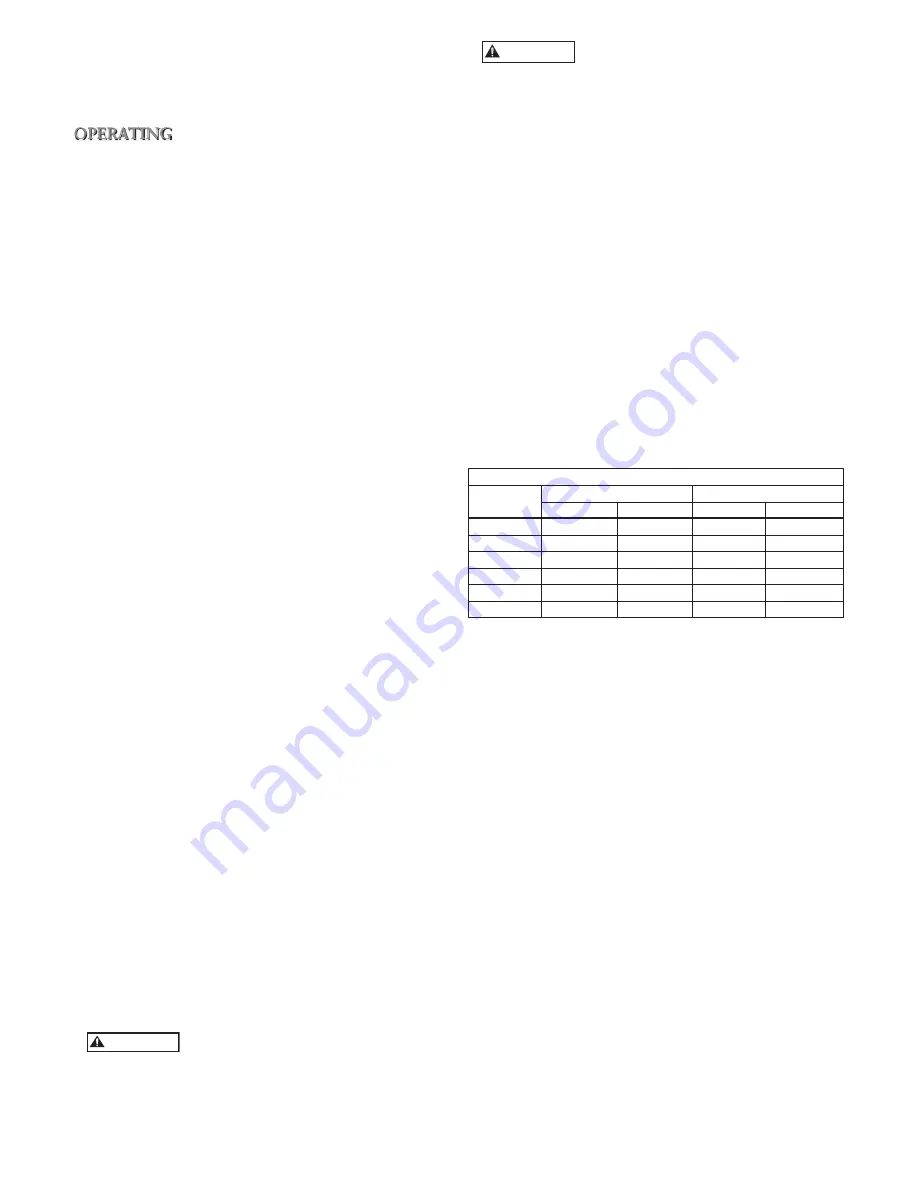
4
• If the pump is operated against a low discharge pres-
sure, it may be noisy. Throttle down the discharge gate
valve until the noise is eliminated. This restriction will
not cause any appreciable loss in capacity.
OPERATING
PRIMING
• Fill the pump tank with liquid before starting. This
may be done through the elbow on the side of the tank.
Use pipe compound when replacing the plug in the
side elbow. These Goulds Water Technology prime and
reprime themselves providing the pump tank is filled
with liquid. Should you lose this liquid from the tank
accidentally or by draining purposely, it will be neces-
sary to refill it with liquid before starting. High suction
lifts, or long suction lines, require additional time and
reduce the performance of the pump. Should you have
difficulty, refer to the Troubleshooting Guide.
• Always keep liquid in the pump tank. No further
lubrication of the pump end is necessary including the
seal assembly. If flow does not start within five minutes,
stop the motor and determine cause (see Trouble-shoot-
ing Guide). Be sure all suction and discharge valves are
open when the pump is priming. Operating the pump
with a closed valve in the system can cause pump dam-
age.
ROTATION
• Your pump is specifically designed to rotate as indicated
by the arrow on the pump tank. Three phase motors
can rotate in either direction. Check the rotation. Inter-
changing any two leads of a three phase motor will
reverse the rotation, if this is found necessary.
WINTER STORAGE
• During freezing weather, it is especially important to
drain all of the liquid from the pump tank. This will
prevent ice from cracking the tank or internal parts.
• To maintain the excellent performance of the pump, fol-
low the motor manufacturer’s storage instructions.
LUBRICATION
• The latest engineering advancements have been in-
corporated into our self-lubricating shaft seal. The liquid
being pumped cools and lubricates the seal, therefore
the pump should never be run dry. A seal well vent has
been provided to protect the electric motor from liquid
damage should the seal leak. DO NOT plug this vent. If
leakage becomes excessive, replace the seal assembly.
MAINTENANCE
• If your pump is not used for a few days, drain the liquid
completely. This will prevent aggravating costly rust
formations.
All electrical work MUST be done by
a licensed electrician. Before working
on motors be certain that the electrical power is off at
the main junction box. Disconnect the fuse or circuit
breaker and have the main switch tagged “Do Not Ener-
gize This Switch, Personnel Working on Equipment”.
Some motors are equipped with built-
in thermal over-loads to shut off the
motor in the event the temperature becomes excessive
(as a result of mechanical or electrical problems; such
as low voltage, poor ventilation, overloaded lines, etc.).
These motors will restart automatically as the motor
cools down. For safety sake, do not work on any motor,
without first shutting off the electricity at the source as
outlined above in the “Warning”. Also all three phase
motors are not thermal protected and motor starters are
recommended.
INSTRUCTIONS FOR LICENSED ELECTRICIANS:
TURN POWER OFF
1. Determine the voltage of the power supply line to
motor. Voltage, phase, ampere draw, and cycles are
given on the motor nameplate.
The wire used to supply power to the motor must be
large enough to carry the amperes for the required
length without excessive voltage drop. The follow-
ing table is meant to be a guide only to the minimum
proper wire size selection. Always consult local electri-
cal codes.
Typical AWG Wire Size for Single Phase Jet Pump Motors
50 Ft. Wire Length
100 Ft. Wire Length
HP
115 V
230 V
115 V
230 V
1
⁄
3
14 – 12 –
½ 14 14 10 14
¾ 12 14 10 14
1 12 14 8 14
1½
10
14
8
12
2 8 12 8 12
WARNING
CAUTION
INSTRUCTIONS FOR LICENSED ELECTRICIANS: