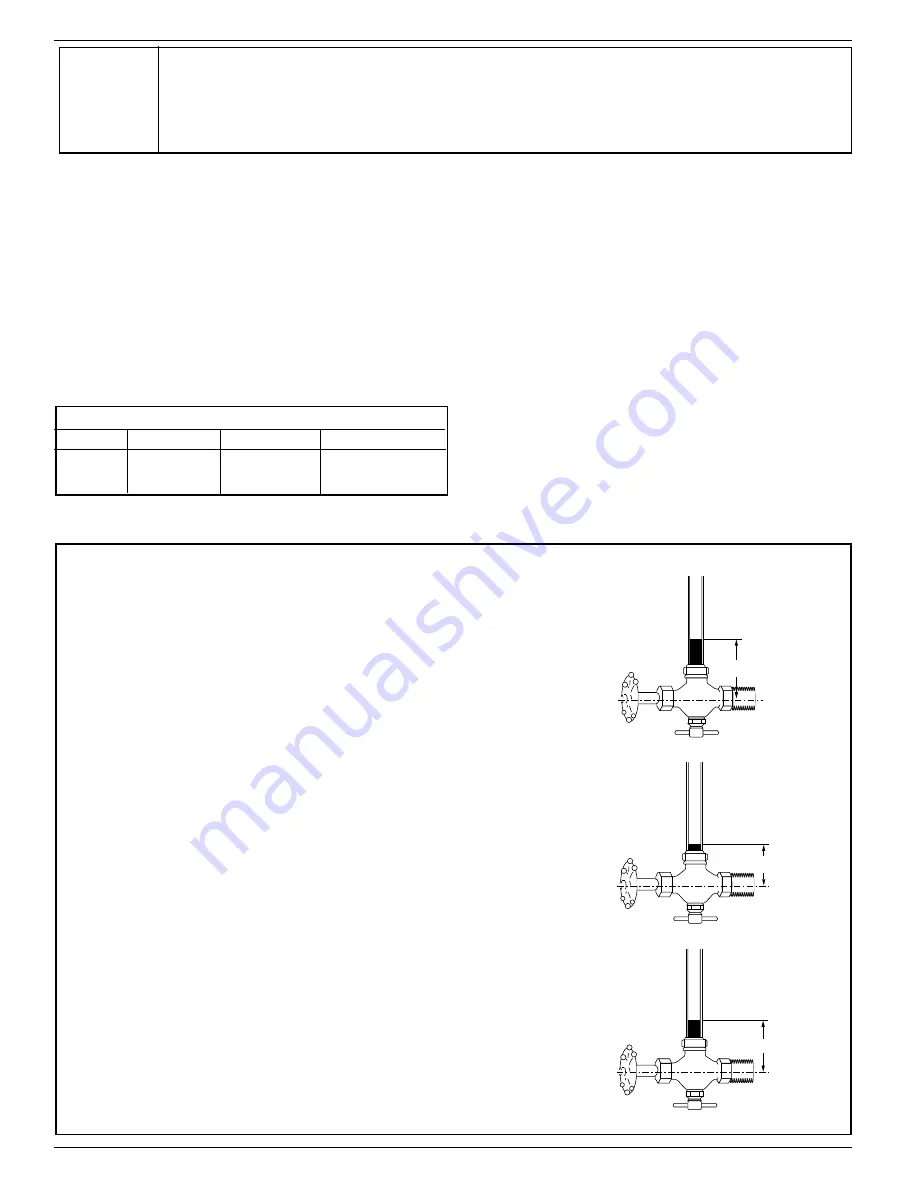
Water Feeder
Closing Level
Low
Water Cut-Off
Burner Starts
2
1
/
4
" (57mm)
3
7
/
16
" (87mm)
2
3
/
4
" (70mm)
Feeder keeps water
level 3
7
/
16
" (87mm)
above center of lower
gauge glass tapping
If extreme priming or
foaming causes water
line to fall 1
3
/
16
" (30mm)
below feeder closing
level, cut-off switch
stops the burner
When water level is
restored
1
/
2
" (13mm)
above emergency.
Cut-off switch starts
burner and the water
feeder resumes
control
Motor Switch Rating (Amperes)
Voltage
Full Load
Locked Rotor
Pilot Duty
120 VAC
10.2
61.2
125 VA at 120
240 VAC
5.1
30.6
or 240 VAC, 60 Hz
OPERATION
Series 47/47-2 Operating Levels
All Models
•
Maximum Water Pressure:
150 psi (10.5 kg/cm
2
)
•
Maximum Water Temp:
120˚F (49˚C)
•
Water Connection Size:
1
/
2
” NPT
47/47-2
•
Maximum Boiler Pressure:
25 psi (1.76 kg/cm
2
)
247/247-2
•
Maximum Boiler Pressure:
30 psi (2.1 kg/cm
2
)
Electrical Ratings
Series 47 Water Feeders and Series 47-2
Combination Water Feeder/Low Water Cut-Off
maintain minimum water level in the boiler during
normal operation.
Series 47-2 Combination Water Feeder/Low
Water Cut-Off allows the burner to operate on
demand as the water level is restored to its
proper level.
Series 47-2 Combination Water Feeder/Low
Water Cut-Off shuts off the burner if the boiler
water level drops 1 3/16” (30mm) below the water
feeder’s closing level.
2
CAUTION:
A more frequent replacement interval may be necessary based on the condition of
the unit at time of inspection. McDonnell Miller s warranty is one (1) year from date
of installation or two (2) years from the date of manufacture.
Failure to follow this warning could cause property damage, personal inj ury or death.
&
'