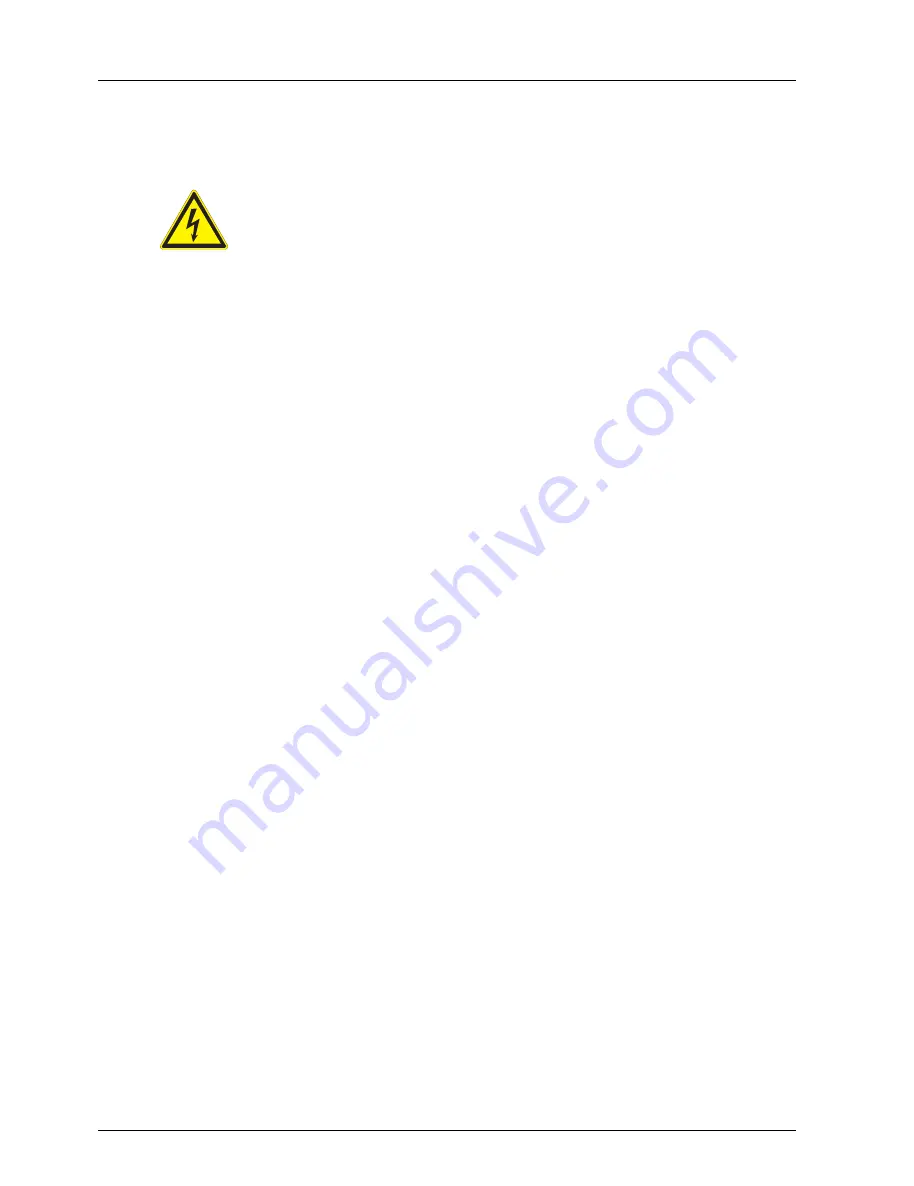
3 - 4
ba75731e04
12/2013
Installation
Cleaning Air Box
3.5
Electrical connection
3.5.1 General installation instructions
WARNING
If the power supply is connected incorrectly, it may represent a danger to
life from electric shock. Pay attention to the following points during instal-
lation:
The Cleaning Air Box may only be connected by a trained electrician.
The power supply must fulfill the specifications given on the nameplate
and in chapter 8 T
ECHNICAL
DATA
.
The Cleaning Air Box may only be connected when it is voltage-free.
An electrical interrupt facility (e.g. switch) for the Cleaning Air Box must
be available on site (see section 3.3 S
AFETY
REQUIREMENTS
ON
THE
ELECTRICAL
INSTALLATION
)
.
The line power supply must only be switched on while the enclosure lid
is closed.
Control line
As the control line, use a two-wire cable without shielding. The cable must meet
the requirements according to section 3.3 S
AFETY
REQUIREMENTS
ON
THE
ELECTRICAL
INSTALLATION
and chapter 8 T
ECHNICAL
DATA
.
NOTE
No external voltages must be fed into the control line. With the
IQ S
ENSOR
N
ET
System 182, the control cycle must not be connected to the auxiliary supply out-
put of the Universal Transmitter DIQ/S 182.
Control relays
Before putting the Cleaning Air Box into operation, make sure that the nominal
voltage of the Cleaning Air Box (see chapter 8 T
ECHNICAL
DATA
) does not
exceed the maximum switching voltage of the relay (see technical data of the
relay).
NOTE
If the nominal voltage of the Cleaning Air Box exceeds the maximum switching
voltage of the relay (such as with the relay of the MIQ/VIS), the relay will be de-
stroyed.
General
installation
notes
Observe the following points when attaching connecting wires to the terminal
strip:
Shorten all the wires to be used to the length required for the installation
Always fit all the ends of the wires with wire end sleeves before connecting
them to the terminal strip
Any wires that are not used and project into the housing must be cut off as
closely as possible to the cable gland.
Close all unused cable glands with blind plugs.
All manuals and user guides at all-guides.com