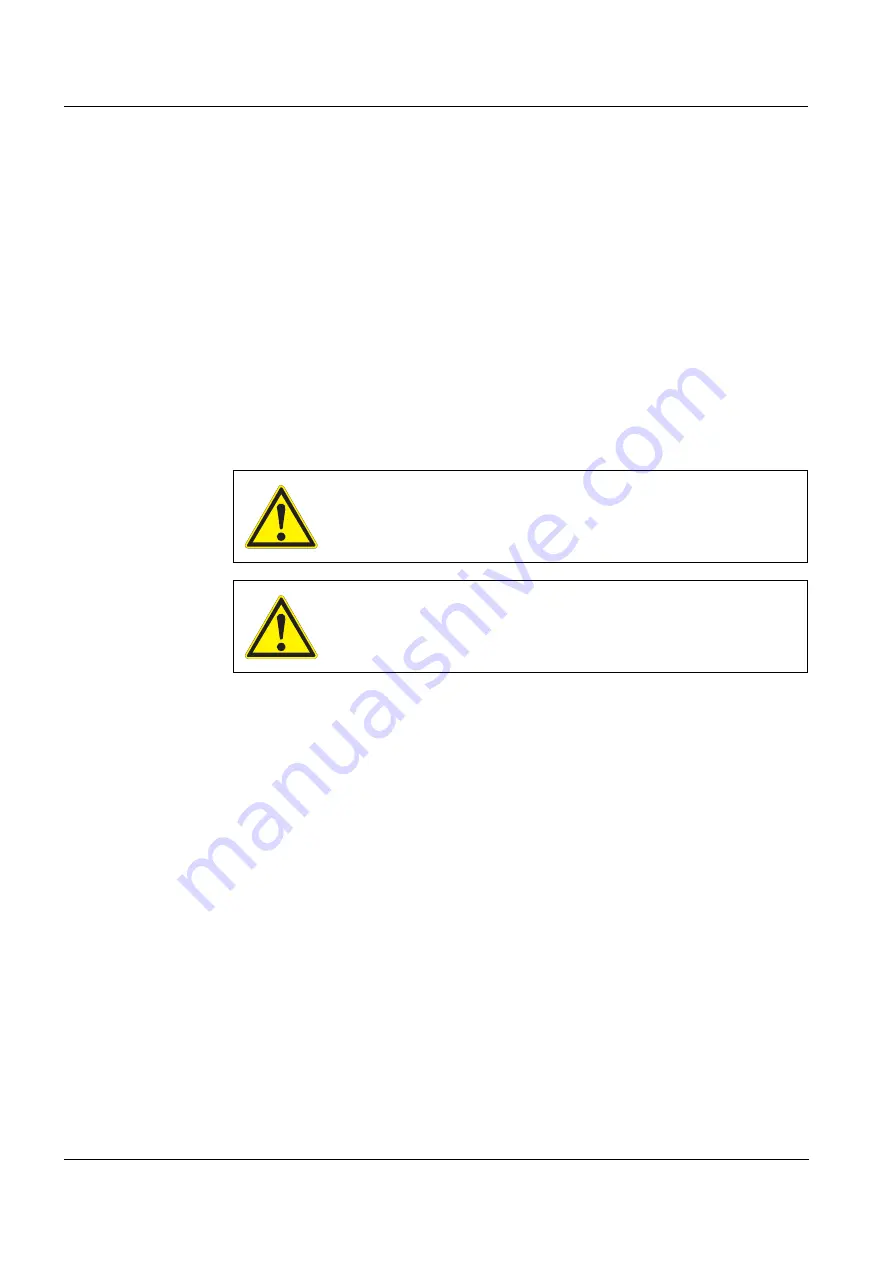
Safety
NitraVis 70x IQ TS
8
ba75952e03
05/2017
2
Safety
2.1
Safety information
2.1.1 Safety information in the operating manual
This operating manual provides important information on the safe operation of
the product. Read this operating manual thoroughly and make yourself familiar
with the product before putting it into operation or working with it. The operating
manual must be kept in the vicinity of the sensor so you can always find the infor
-
mation you need.
Important safety instructions are highlighted in this operating manual. They are
indicated by the warning symbol (triangle) in the left column. The signal word
(e.g. "CAUTION") indicates the level of danger:
NOTE
indicates a situation where goods might be damaged if the actions mentioned
are not taken.
2.1.2 Safety signs on the product
Note all labels, information signs and safety symbols on the product. A warning
symbol (triangle) without text refers to safety information in this operating
manual.
2.1.3 Further documents providing safety information
The following documents provide additional information, which you should
observe for your safety when working with the measuring system:
Operating manuals of other components of the IQ S
ENSOR
N
ET
system
(power packs, controller, accessories)
Safety datasheets of calibration and maintenance equipment (e.g. cleaning
solutions).
WARNING
indicates a possibly dangerous situation that can lead to seri
-
ous (irreversible) injury or death if the safety instruction is not
followed.
CAUTION
indicates a possibly dangerous situation that can lead to slight
(reversible) injury if the safety instruction is not followed.
Summary of Contents for WTW NitraVis 700 Series
Page 55: ......