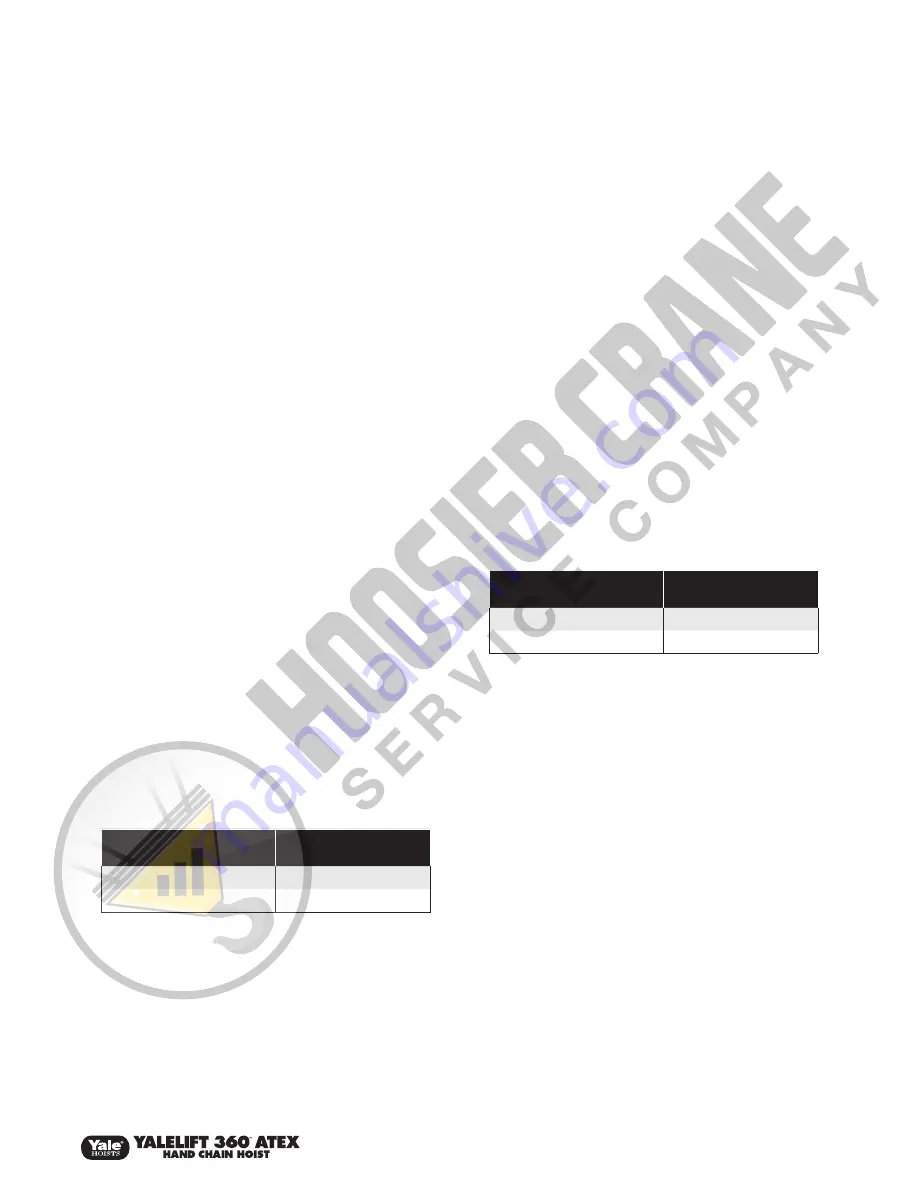
13
P/N 10001646 Rev. AA
June 2015
MAINTENANCE (CONTINUED)
2. To inspect or replace the liftwheel, chain guide or stripper, it is
necessary to disassemble the hoist. Remove the load chain
(See “REPLACING LOAD CHAIN” on previous page) and then
remove the handwheel cap and the handwheel cover support.
Lift off the handwheel cover and slide it down the hand chain.
Lift the hand chain out of the hand wheel pockets. Remove
cotter pin, castle nut and washer from the drive shaft. Remove
handwheel overload clutch assembly by turning handwheel
counter clockwise. Slide front brake disc, ratchet disc assembly
and rear brake disc from pressure disk. Remove retaining ring
and then remove pressure disc by turning counter clockwise.
Remove the handwheel side plate, by sliding it over drive shaft.
Remove the stripper and chain guide. Examine the stripper,
chain guide, liftwheel and loose end connector for wear and
damage.
If the stripper, chain guide and/or loose end connector are worn
or damaged they should be replaced. If the liftwheel is not worn
or damaged, reassemble the hoist in reverse to the order given
above. If the liftwheel is to be replaced, continue to disassemble
the hoist.
NOTE: Two points of caution to be observed in disassembly and
assembly of the gears:
a. Loose rollers are used in various locations in some units.
Care must be taken so as to not lose or misplace these.
b. For proper operation, the correct number of rollers must
be installed at the rotating points. Applying grease to the
rollers will help hold them in position during assembly.
Remove the gear cover, end covers
and gears. Remove drive
shaft by sliding it out and remove locking ring. Remove washer
and liftwheel gear. Remove the liftwheel and replace it. The
liftwheel may require pressing out of liftwheel bearings. Check
the gears and other parts for excessive wear, cracks and
distortion. Replace parts as necessary and then reassemble the
unit in reverse to the order in which it was disassembled. Install
the load chain per manual section “REPLACING LOAD CHAIN”,
on previous page. After the hoist is completely reassembled, it
must be tested for proper operation (See “TESTING”, page 15).
3.
HANDWHEEL OVERLOAD CLUTCH ASSEMBLY:
NOTE: Slip clutch is an option on Yale Yalelift 360™ ATEX hoist (not standard)
To inspect or replace handwheel overload clutch assembly,
it is necessary to partially disassemble the hoist. Remove the
handwheel cap and the handwheel cover support. Lift off the
handwheel cover and slide it down the hand chain. Lift the hand
chain out of the handwheel pockets. Remove cotter pin,
castle nut and washer from the drive shaft. Remove handwheel
overload clutch assembly by turning handwheel counter
clockwise. Use spanner socket tool (available from Columbus
McKinnon) to remove groove nut from handwheel brake hub.
Slide Belleville spring washer, pressure plate front brake disc,
handwheel and rear brake disc from handwheel brake hub.
Inspect both brake discs and replace if excessive wear, scoring,
glazing or contamination is found. If brake disc is worn down
to the following thickness, replacement is required:
Capacity
(ton)
Thickness Min.
in.
(mm)
¼, ½, 1, 1½ & 2
.043
(1.1)
3, 4, 5, 6, 8, 10 & 12
.063
(1.6)
Inspect pressure plate, handwheel and handwheel brake hub
friction surfaces, replace if excessively scored.
Replace parts as necessary and then reassemble the unit
in reverse to the order in which it was disassembled. Once
the handwheel overload clutch is assembled, tighten/torque
the groove nut with the spanner socket tool (available from
Columbus McKinnon).
The handwheel overload clutch should be adjusted to
approximately 125% of rated capacity. This setting must be
checked with the handwheel overload clutch assembled into
the hoist (See “ADJUSTMENT OF LOAD LIMITER”).
4. To inspect or replace the pawl or pawl spring, it is necessary
to partially disassemble the hoist. Remove the hand chain wheel
cover and slide it down the hand chain. Lift the hand chain out of
the hand chain wheel pockets. Remove the cotter pin, castle nut
and washer from the drive shaft. Remove hand chain wheel by
turning hand chain wheel counter clockwise.
Remove retaining ring, pawl, and pawl spring from handwheel
side plate assembly. Inspect pawl and pawl spring for wear,
replace if worn. Replace parts as necessary and then reassemble
the unit in reverse to the order in which it was disassembled.
After the hoist is completely reassembled, it must be tested for
proper operation (See “TESTING”, page 15).
5. To replace hook latch, grind off head of rivet and drive it out.
Remove and discard the latch and spring. Attach the new latch
and spring using the roll pin provided in the latch kit.
ADJUSTMENT OF LOAD LIMITER
NOTE: Slip clutch is an option on Yale Yalelift 360™ ATEX hoist (not standard)
To adjust the load limiter:
1. Remove the hoist from the supporting structure and lay it on
a flat working surface with the handwheel facing up.
2. Remove the three screws securing the plastic center cap and
remove the cap from the handwheel cover.
3. Block the load chain by inserting a screwdriver or pin through the
load chain just below the hoist frame. Operate the handwheel in
the up direction to remove the slack from the load chain, closing
and locking the brake.
4. Change the adjustment of the load limiter by tightening
the groove nut with the spanner socket tool (available from
Columbus McKinnon.) to increase the setting or by loosening the
groove nut to decrease the setting.
5. Perform required load tests after adjustment. (See “TESTING”,
page 15). Revise the adjustment if necessary. NOTE: The hoist
should not be able to lift 150% of the rated capacity load if the
load limiter has been properly adjusted.
6. Replace the center cap in the handwheel cover.
Capacity
(ton)
Spanner Socket Tool
Product Code
¼, ½, 1
00401422
1½, 2, 3, 4, 5, 6, 8, 10 & 12
00401424