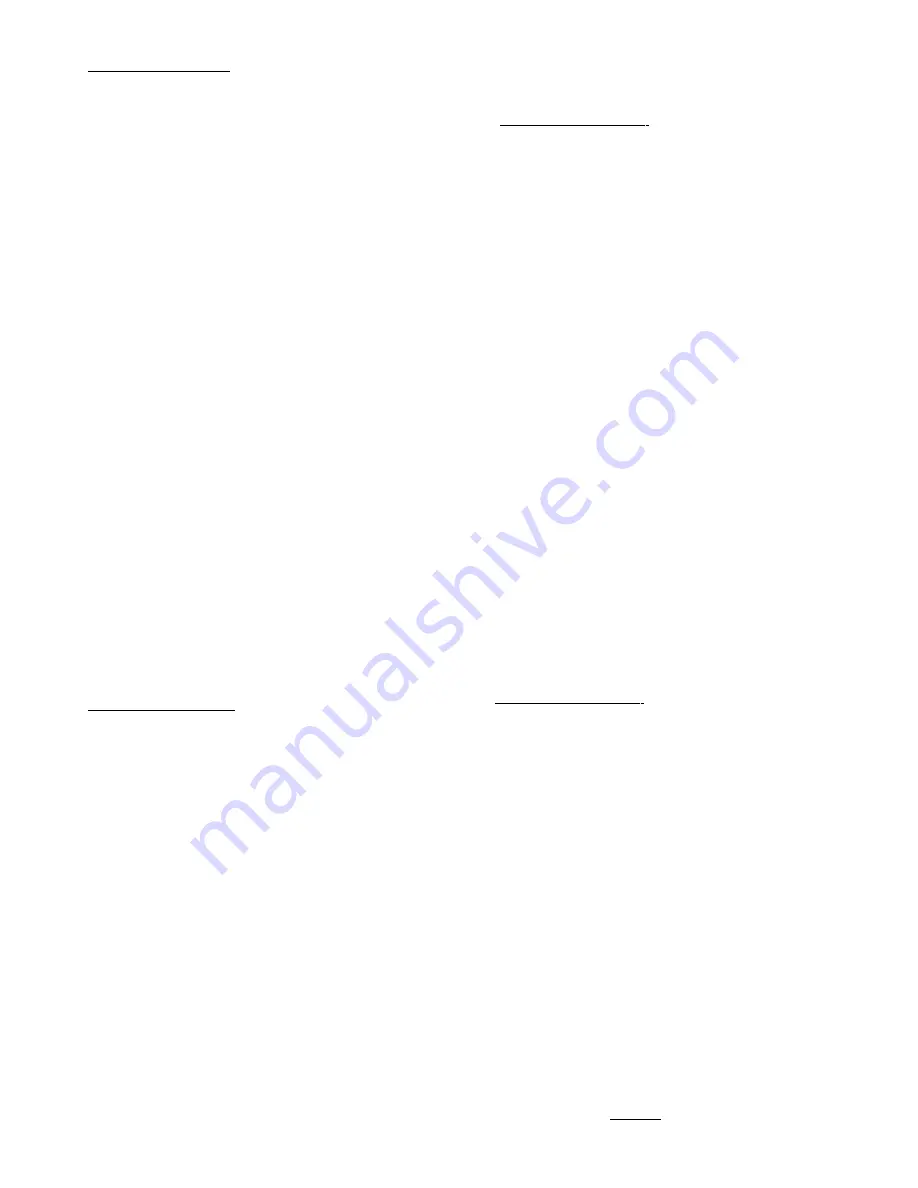
Page 18
f. Reeving - 6 part single.
See Figure 5-8,
'
for diagram.
See Figure 9-15 for bottom block parts - 9/16" rope.
See Figure 9-19 for bottom block parts - 3/8" rope.
With new cable installed on drum as described in
Paragraph 5-9.c, single reeved above, proceed with
rereeving following steps below:
(1) Grasp cable at a point one-third (approx. 14’0") the
distance hanging below the rope drum and form a
loop. Place one upper sheave in this loop. Slide upper
sheave with ca ble into sheave pocket; partially insert
sheave pin to hold sheave in place.
(2) Repeat (1) above and install second upper sheave
with rope. Insert sheave pin and install key plates and
bolts to secure sheave pin.
(3) Thread rope end socket through limit switch weight;
then, pass it over partial sheave, inside hoist, and
insert in anchor fitting at hoist frame. Be certain power
is off before opening electrical compartment cover for
access to anchor fitting. With end fitting properly
seated in anchor, replace cotter pin in end of socket.
Three loops have now been formed for bottom block
sheaves.
(4) Place sheave in each loop. Install one sheave with
cable in bottom block; partially insert sheave pin to
hold sheave in place. Note: Be certain to install spacer
washers between sheaves, when shown on parts
illustration.
(5) Repeat step 4 for remaining bottom block sheaves.
Install sheave pin through sheaves. Replace key plates
and bolts securing sheave pin.
(6) Replace sheave guard.
(7) Lubricate cable per Paragraph 4-3.
g. Reeving - 2 part double.
See Figure 5-8,
(
for diagram.
See Figure 9-16 for block parts.
With new rope installed on drum as described in Paragraph
5-9.c, double reeved above, proceed with rereeving
following steps below:
(1) Form loops in the two ropes coming from rope drum.
Place these loops into bottom block pockets and slide
pipe or rod through sheave pin holes. Note position of
ropes passing limit stop bar.
(2) Partially insert upper block sheave pin in opening and
install one spacer washer. Raise remaining rope up to
hoist, form a loop and place upper sheave in this loop.
(3) Place sheave with rope into upper sheave pocket and
slide pin partially thru sheave. Install remaining washer
and push pin thru side plates. Install snap ring on
each end of pin to secure pin in place.
(4) Insert lower sheave pin into bottom block removing
pipe as sheave pin is inserted. Be certain washers are
replaced as shown on parts illustration. With sheave
pin installed, replace key plates and bolts to secure
sheave pin.
(5) Replace sheave guard.
(6) Lubricate rope per Paragraph 4-3.
h. Reevinq - 3 part double.
See Figure 5-8,
$
for diagram.
See Figure 9-17, for block parts.
With new rope installed on rope drum as described in
Paragraph 5-9.c, double reeved above, proceed with
rereeving following steps below:
(1) Form loops in the two ropes coming from rope drum.
Place these loops into bottom block pockets and slide
pipe or rod through sheave pin holes. Note position
of ropes passing limit stop bar.
(2) Grasp remaining rope at midpoint loop and raise two
rope parts up to the hoist. Carefully form two upper
sheave loops and insert into upper sheave pockets.
Slide pipe or rod through sheave pin holes to hold
the two ropes.
(3) Pull remaining rope down to the lower block equalizer
sheave. Place equalizer sheave in loop and sheave
with rope in sheave pocket. Insert sheave pin thru
one washer, the sheave and the other washer.
(4) Push sheave pin thru side plates and install snap
ring on each end of pin to secure pin.
(5) Insert lower sheave pin into bottom block thru washers
and sheaves as shown on parts illustration, removing
pipe as sheave pin is inserted.
(6) Install key plates and bolts to secure pin.
(7) Repeat steps 5 & 6 for upper block sheaves.
(8) Replace sheave guard.
(9) Lubricate rope per Paragraph 4-3.
j. Reevinq - 4 part double.
See Figure 5-8,
)
for diagram.
See Figure 9-18, for block parts.
With new rope installed on rope drum as described in
Paragraph 5-9.c, double reeved above, proceed with
rereeving following steps below:
(1) Form loop in each rope coming from rope drum. Place
these loops into outside sheave pockets in bottom
block. Note position of ropes passing limit stop bar.
Slide pipe or rod thru sheave pin holes to hold the
two ropes.
(2) Grasp remaining rope at midpoint loop and raise loop
with two ropes up to the hoist. Carefully form two
upper sheave loops and insert sheaves with rope
into upper sheave pockets. Slide pipe thru upper
sheave pin holes to hold the two ropes.
(3) Pull loop and two ropes down to the bottom block.
Pass ropes across bottom block between ropes placed
there in step 1. Note position of ropes passing limit
stop bar.
(4) Carefully remove pipe while holding first two ropes in
bottom block and insert ropes in step 3 into outside
block pockets between existing ropes.
Summary of Contents for SHAW-BOX
Page 66: ...NOTES ...
Page 67: ...NOTES ...