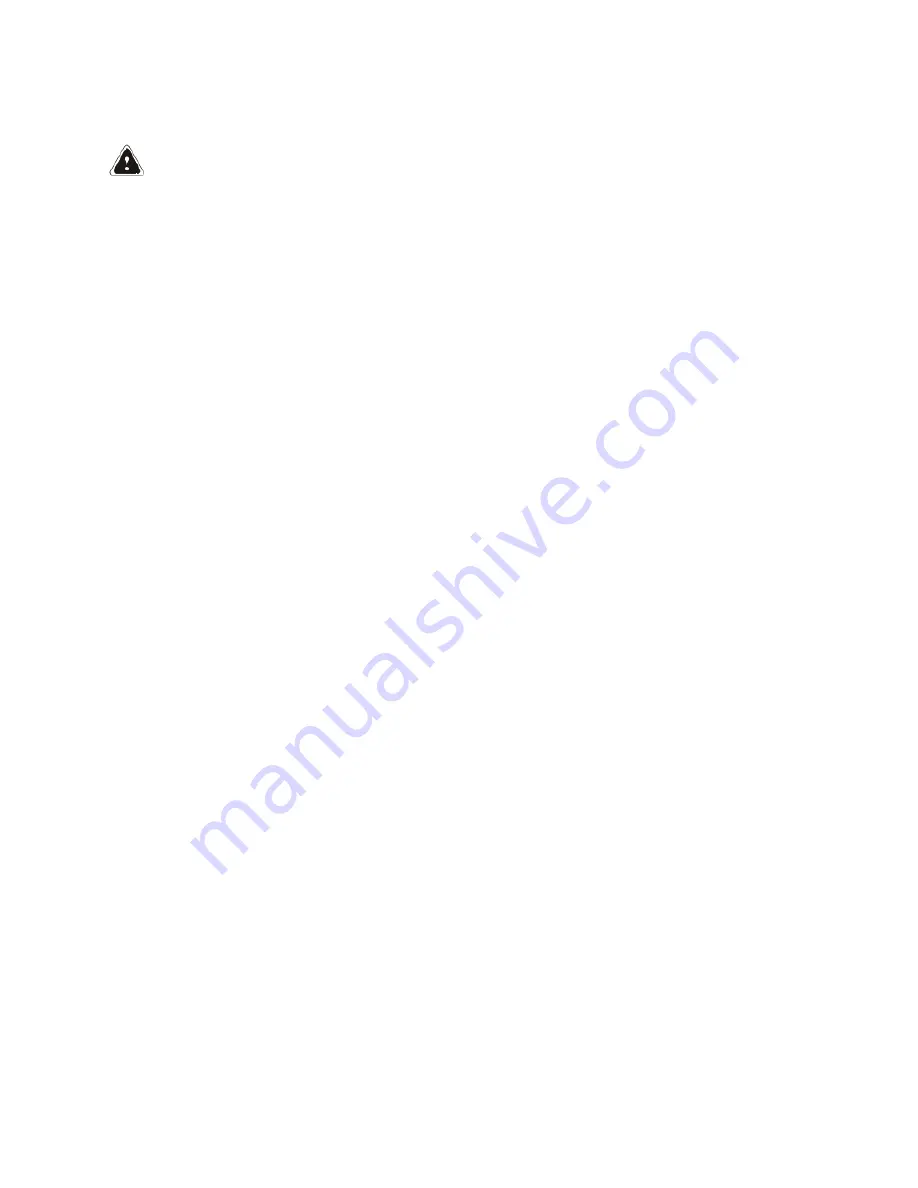
TROUBLESHOOT ELECTRICAL SYSTEM
WARNING
When examining the electrical wires, the key
switch and battery grounding wire should be
turned off and the wiring harness with the same
serial number should be connected. Check the
voltage of the electrical components. Avoid
contact with conductive accessories to prevent
short. Use the electric box wiring and schematic
drawings as reference, and follow the steps below
to inspect the wiring harness of the truck.
•
No damage on each electrical part
•
Each plug should be connected properly with no
rust and dirt
•
Each plug should maintain a safe distance of
10 mm (0.40 in.)from its ambient metal part.
•
The main wire shows no damage or decay
•
Each plug is labeled to avoid possible wrong
connection
•
All wiring should be kept away from high
temperature objects like the exhaust system
•
All wiring and fuel (gas) manifold should be kept
away from high temperature objects like the
exhaust system
When the truck fails, first check the electric box to
inspect for damage to the time relay and fuse (the time
relay will smell burned, if it is damaged). The middle of
the fuse will be blown. Use a multimeter to check when
these instances are not visible. Replace the damaged
parts with new ones. The specification of the new fuse
should not exceed that of the removed fuse.
Example 1: The IC truck could not be started
•
Turn the key and listen to hear if the starting
motor is working (engine will turn over). If
starting motor is not functioning, perform the
following.
1. Check if the gear is at neutral position (with
OPS installed, whether the seat, seat belt
and hand brake are in place).
2. Check if the negative end of the wiring is
connected.
3. Check the start system (key switch) to
confirm it functions correctly.
4. Check for damage at the starting motor. If
the starting motor functions properly, check
if the oil supply system is working.
Example 2: The IC truck could be started but
could not move forward or reverse
•
For manually controlled truck, the gear is
controlled by the lever.
•
For the hydraulic controlled truck (With OPS
installed, make sure that the seat and seat belt
switch are off and hand brake is on), check the
gear switch’s input and output voltage to see if it
is 12V.
1. If there is no input, then check the power
supply for the gear switch lever.
2. If it is with input voltage but without output
voltage, it means that the gear switch lever
is damaged
3. If it is with both input and output voltage,
then check the voltage at where the
directional valve is located.
4. If voltage exists, the valve or transmission
is damaged. If there is no voltage, the
wiring between the gear switch lever and
directional valve is disconnected.
Troubleshooting
Truck will not start
1. Check if the starting condition is met when the
operator sits on the seat (whether the seat
switch is closed and grounded).
2. Check if the starting conditions are met and the
handbrake is pulled up (whether the handbrake
switch is closed and grounded).
3. Check if the starting conditions are met. For
Australian customers, if there is seat belt and
seat starting sequence, whether the starting
conditions are followed.
Lift, Lowering and Tilt functions are not working
1. Check if the seat switch is closed and grounded.
2. Check if the solenoid valve is closed. When the
seat switch is closed and grounded, there
should be 12V voltage input to the solenoid
valve. When the seat switch is closed and
grounded, there should be 12V voltage at the
output end of the electrical box.
3. Check if the and socket connections are tight or
loose.
4. Confirm there is voltage input to the solenoid
valve. If valve is not working, check the solenoid
valve spool.
Forward and reverse functions are not working
1. Check if the seat switch is closed and not
grounded.
8000 YRM 2199
Electrical System
81
Summary of Contents for A7S1
Page 4: ......
Page 7: ...TABLE OF CONTENTS Continued Lubrication System 83 PDM Schematics 85 Table of Contents iii ...
Page 8: ......
Page 36: ...Figure 25 2 2 5T Wheel Brakes Brake System 8000 YRM 2199 28 ...
Page 54: ...Figure 43 Oil Circuit of Hydraulic System Hydraulic System 8000 YRM 2199 46 ...
Page 69: ...Figure 58 Two Stage Free Lift and Three Stage Masts 8000 YRM 2199 Lifting System 61 ...
Page 76: ...Figure 61 With NISSAN engine K21 K25 Sheet 1 of 2 Electrical System 8000 YRM 2199 68 ...
Page 77: ...Figure 62 With NISSAN engine K21 K25 Sheet 2 of 2 8000 YRM 2199 Electrical System 69 ...
Page 78: ...Figure 63 With PSI engine Sheet 1 of 2 Electrical System 8000 YRM 2199 70 ...
Page 79: ...Figure 64 With PSI engine Sheet 2 of 2 8000 YRM 2199 Electrical System 71 ...
Page 80: ...Figure 65 With Mitsubishi engine S4S Sheet 1 of 2 Electrical System 8000 YRM 2199 72 ...
Page 81: ...Figure 66 With Mitsubishi engine S4S Sheet 2 of 2 8000 YRM 2199 Electrical System 73 ...
Page 82: ...Figure 67 With Xinchai engine Sheet 1 of 2 Electrical System 8000 YRM 2199 74 ...
Page 83: ...Figure 68 With Xinchai engine Sheet 2 of 2 8000 YRM 2199 Electrical System 75 ...
Page 84: ...Figure 69 With Yanmar engine 92 98 Sheet 1 of 2 Electrical System 8000 YRM 2199 76 ...
Page 85: ...Figure 70 With Yanmar engine 92 98 Sheet 2 of 2 8000 YRM 2199 Electrical System 77 ...
Page 86: ...Figure 71 With Yanmar engine 94 Sheet 1 of 2 Electrical System 8000 YRM 2199 78 ...
Page 87: ...Figure 72 With Yanmar engine 94 Sheet 2 of 2 8000 YRM 2199 Electrical System 79 ...
Page 88: ...Figure 73 Optional Accessories Electrical System 8000 YRM 2199 80 ...
Page 93: ...PDM Schematics 8000 YRM 2199 PDM Schematics 85 ...
Page 94: ......
Page 95: ...8000 YRM 2199 Figure 76 PDM Suitable For All Engines 87 88 blank ...
Page 96: ......
Page 97: ...8000 YRM 2199 Figure 77 PDM With OPS Suitable For All Engines 89 90 blank ...
Page 98: ......
Page 99: ......