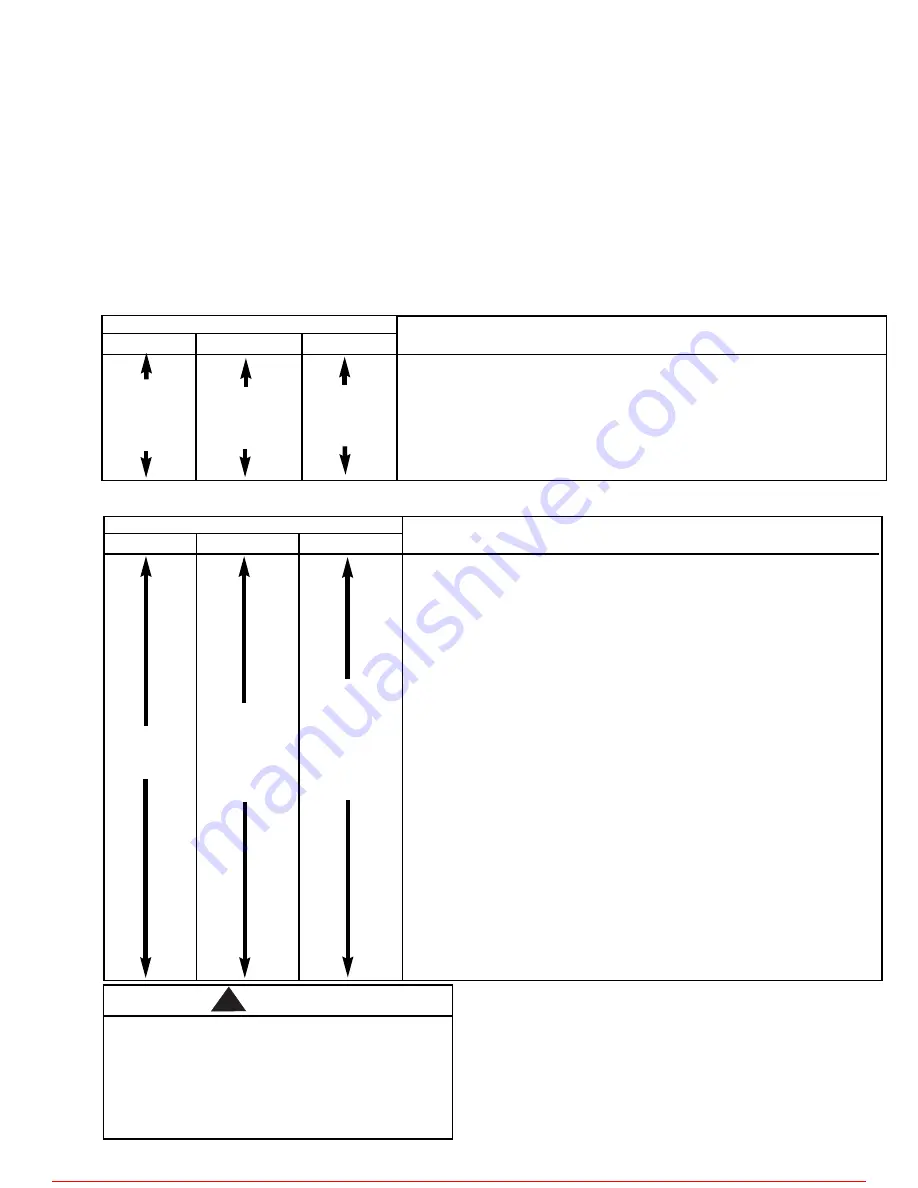
Minimum Inspection Schedule
Frequent Inspections
: These inspections are
visual examinations by the operator or other des-
ignated personnel. Records of such inspections are
not required. The frequent inspections are to be
performed monthly for normal service, weekly to
monthly for heavy service, and daily to weekly for
severe service and they should include those items
listed in Table 1.
Periodic Inspections:
These inspections are visu-
al inspections of external conditions by an appoint-
ed person. Records of periodic inspections are to
be kept to provide the basis for continuing evalua-
tion of the condition of the hoist.
Periodic inspections are to be performed yearly for
normal service, semi-annually for heavy service and
quarterly for severe service and they are to include
those items listed in Table 2.
Any parts that are deemed unserviceable are to be
replaced with new parts before the unit is returned
to service. It is very important that the unserviceable
parts be destroyed and properly disposed of to
prevent their possible future use as a repair item.
TYPE OF SERVICE
Normal
Heavy
Severe
TYPE OF SERVICE
Normal
Heavy
Severe
ITEM
a) Brake for evidence of slippage.
b) Hooks for damage, cracks or excessive throat opening, latch
engagement and latch operation - see page 6.
c) Inspect load chain for adequate lubrication, signs of wear,
damaged links or foreign matter - see page 6.
d) Inspect reeving of the load chain to make sure it is proper -
see page 6.
ITEM
a) Frequent inspections per Table 1.
b) External evidence of loose bolts or nuts.
c) External evidence of worn, corroded, cracked or distorted hook
blocks, suspension bolts, gears, pins, bearings, hand chain wheel,
frames, hoist hanger, load chain guide, hook block pin on 1/4
thru 2 ton units, dead end pin on 3, 4, 8 and 10 ton units, and
dead end screw on 5 and 6 ton units.
d) External evidence of damage to hooks, hook nuts or collars and
hook nut or collar pins.
e) External evidence of damage or excessive wear of the pockets of
the liftwheel, handwheel, hook block sheaves and hanger sheaves.
f) External evidence of worn, glazed or oil contaminated friction
discs, scoring of handwheel hub, ratchet, and friction hub.
g) External evidence of worn pawl and ratchet teeth; corroded,
stretched or broken pawl spring.
h) Supporting structure and trolley, if used, for continued ability to
support the imposed loads.
i)
Inspect trolley wheels for external wear on the tread and flange,
and for wear on the internal bearing as evidenced by looseness
on the stud.
j)
Warning label and tube for absence or illegibility.
k) Check for proper connections at dead end and loose end of load
chain.
l)
Load Limiter components for corrosion.
Monthly
W
eekly
to
Monthly
Daily
to W
eekly
Table 1 Minimum Frequency Inspections
Table 2 Minimum Periodic Inspections
Y
early
Twice a Y
ear
Every 3 Months
Any deficiencies are to be corrected before returning the
hoist to service. Operating a hoist with worn or damaged
parts or a malfunctioning hoist may result in serious
personal injury to the operator, nearby personnel and/or
property damage.
Also, the external conditions may show the need for dis-
assembly to permit a more detailed inspection which, in
turn, may require the use of nondestructive type testing.
PREVENTIVE MAINTENANCE
In addition to the above inspection procedure, a preventive
maintenance program should be established to prolong
the useful life of the hoist and maintain its reliability and
continued safe use. The program should include the
periodic inspections with particular attention being paid
to the lubrication of various components using the
recommended lubricants.
5
WARNING
!
For more information contact: Sievert Crane and Hoist, (708) 771-1600, parts@sievertelectric.com, www.sievertcrane.com