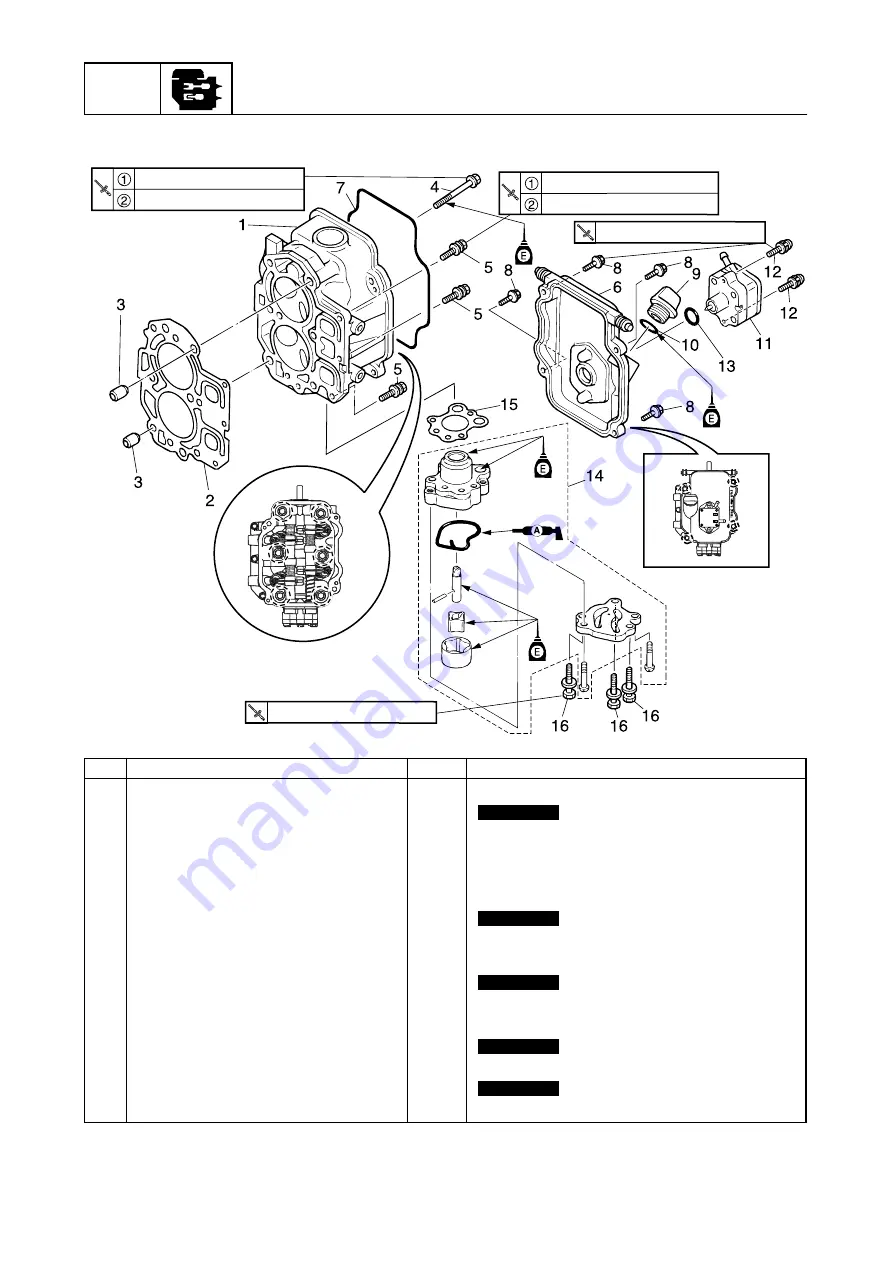
POWR
5-21
6D45F11
Power unit
6D45070E
6 N·m (0.6 kgf·m,4.4 ft·lb)
12 N·m (1.2 kgf·m, 8.7 ft·lb)
8 N·m (0.8 kgf·m, 5.8 ft·lb)
15 N·m (1.5 kgf·m,11 ft·lb)
30 N·m (3.0 kgf·m, 22 ft·lb)
8 N·m (0.8 kgf·m, 5.8 ft·lb)
No.
Part name
Q’ty
Remarks
1
Cylinder head assembly
1
2
Gasket
1
3
Dowel pin
2
4
Bolt
6
M8
×
74 mm
5
Bolt
3
M6
×
25 mm
6
Cylinder head cover
1
7
Seal
1
8
Bolt
4
M6
×
20 mm
9
Oil filler cap
1
10
O-ring
1
11
Fuel pump assembly
1
12
Screw
2
M6
×
30 mm
13
O-ring
1
14
Oil pump assembly
1
15
Gasket
1
16
Bolt
3
M6
×
35 mm
Not reusable
Not reusable
Not reusable
Not reusable
Not reusable
Cylinder head
6D45F11-05 03.10.9 20:44 Page 24