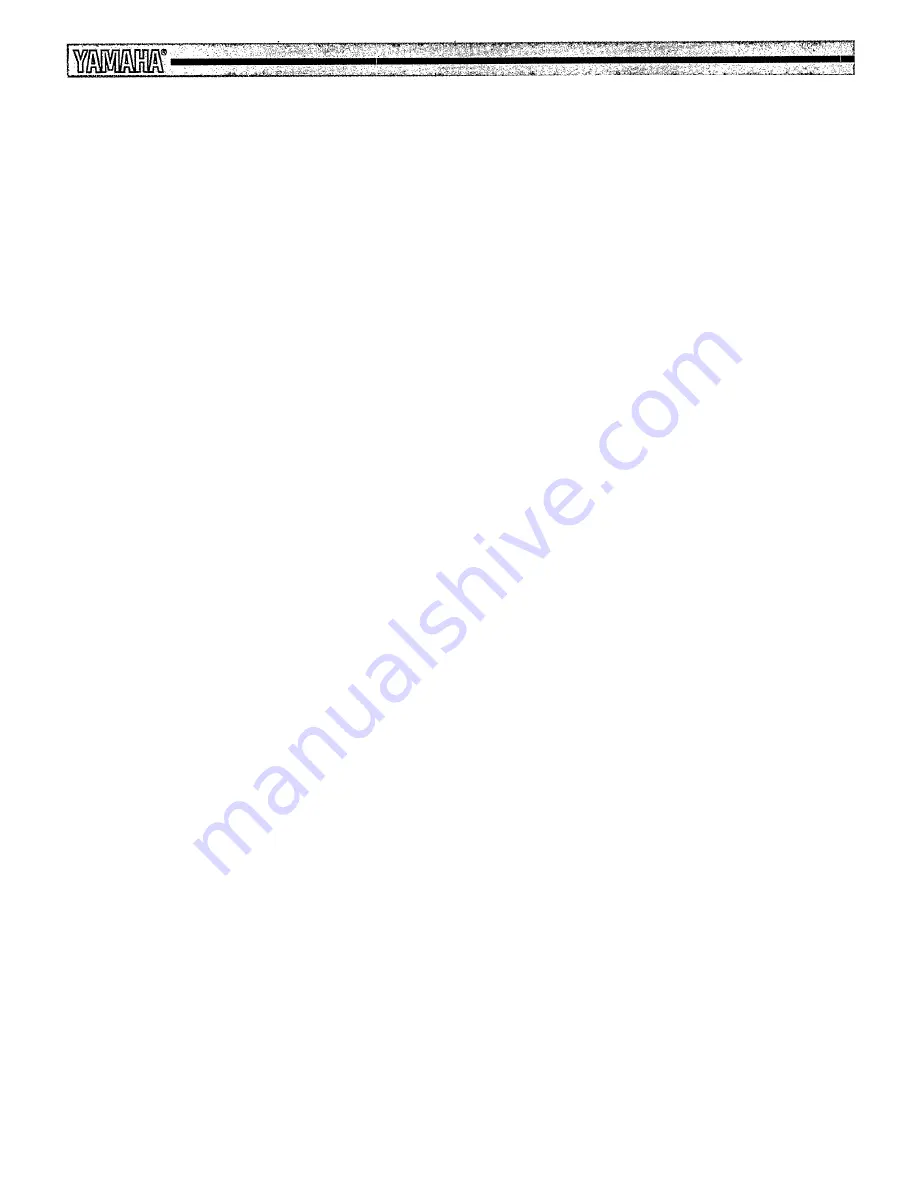
Before actually mounting the selected components, it
is wise to carefully plan out each rack with an eye to
signal flow, heat flow, and weight distribution. It might
be best to mount together components that function as a
group: the equalizer, active crossover and power ampli-
fier for a single loudspeaker or array, for example. On
the other hand, some prefer to mount all the equalizers
for the system in one rack, all the power amplifiers in
another, and so on. If you select the latter approach,
you may find that the power amplifier racks are danger-
l
ous y heavy. Also, if one all the same rack is damaged,
you could be out of business, whereas loss of a mixed
rack will only partially impair the system. It is far
better to put some thought into such matters before-
hand than to do all the work and then correct mistakes
after they cause major problems.
At its best, configuring equipment racks is a true
craft combining a focus on practical utility and careful
engineering with a concern for clean appearance. In a
well prepared rack, electronic devices are accessible yet
protected, and are neatly and consistently mounted
with proper hardware. Interior and exterior work
lamps, integral power distribution, ground-fault indica-
tion and a well stocked spare fuse compartment are
among the extra touches that are usually provided.
Equipment that may generate strong electromagnetic
fields (power amps with large transformers) should be
separated from equipment that has high gain (micro-
phone and phono cartridge preamplifiers or cassette
decks).
The hallmark of a professional rack is the care that
is taken with the internal wiring. Color coding and/or
clear and logical cable marking facilitate troubleshoot-
ing and reflects an understanding of the electronic
signal flow. Belated groups of connections are neatly
routed and bundled with cable ties. Audio signal cables
are kept separate from power cords, and low level signal
cables are separated from high level signal cables.
Excess cable (including any service loop) is neatly
stowed and tied down, and all connections are secured
so that they stay in place in shipment.
Finally, touring sound professionals protect their
equipment racks in foam-lined flight cases equipped
with wheels and handles to facilitate handling. Given
the considerable investment in equipment, materials
and time that a fully loaded rack represents, such
protection is essential. Flight cases in standard sizes
are available from a number of manufacturers, and it
is generally not necessary or economical to make them
yourself.
Page 4-18
Summary of Contents for PM4000
Page 1: ...PROFESSIONAL AUDIO MIXING CONSOLE PM4000 OPERATING MANUAL YAMAHA ...
Page 2: ...PM4000 OPERATING MANUAL ...
Page 7: ...Section 1 Introduction ...
Page 11: ...Section 2 Brief Operating Instruction ...
Page 47: ...Section 3 Specifications ...
Page 51: ...Dimensional Drawings PM4000 Console all versions Page 3 4 ...
Page 52: ...Page 3 5 ...
Page 53: ...Page 3 6 PM4000 Console Rear Profiles ...
Page 54: ...Module Block Diagrams See back of the manual for overall system block diagram Page 3 7 ...
Page 55: ...Page 3 8 ...
Page 56: ...Page 3 9 ...
Page 57: ...Page 3 10 ...
Page 58: ...Page 3 11 ...
Page 59: ...Page 3 12 ...
Page 60: ...Section 4 Installation Notes ...
Page 72: ...Figure 4 13 Cables For Use With Balanced Sources Page 4 12 ...
Page 79: ...SECTION 5 Gain Structure and Levels ...
Page 82: ...Figure 5 1 Dynamic Range and Headroom in Sound Systems Page 5 3 ...
Page 86: ...Section 6 Optional Functions ...
Page 106: ...Section 7 Operating Notes and Hints ...
Page 119: ...Section 8 Applications ...
Page 127: ...Section 9 Maintenance ...
Page 131: ......
Page 132: ...YAMAHA VN02300 ...