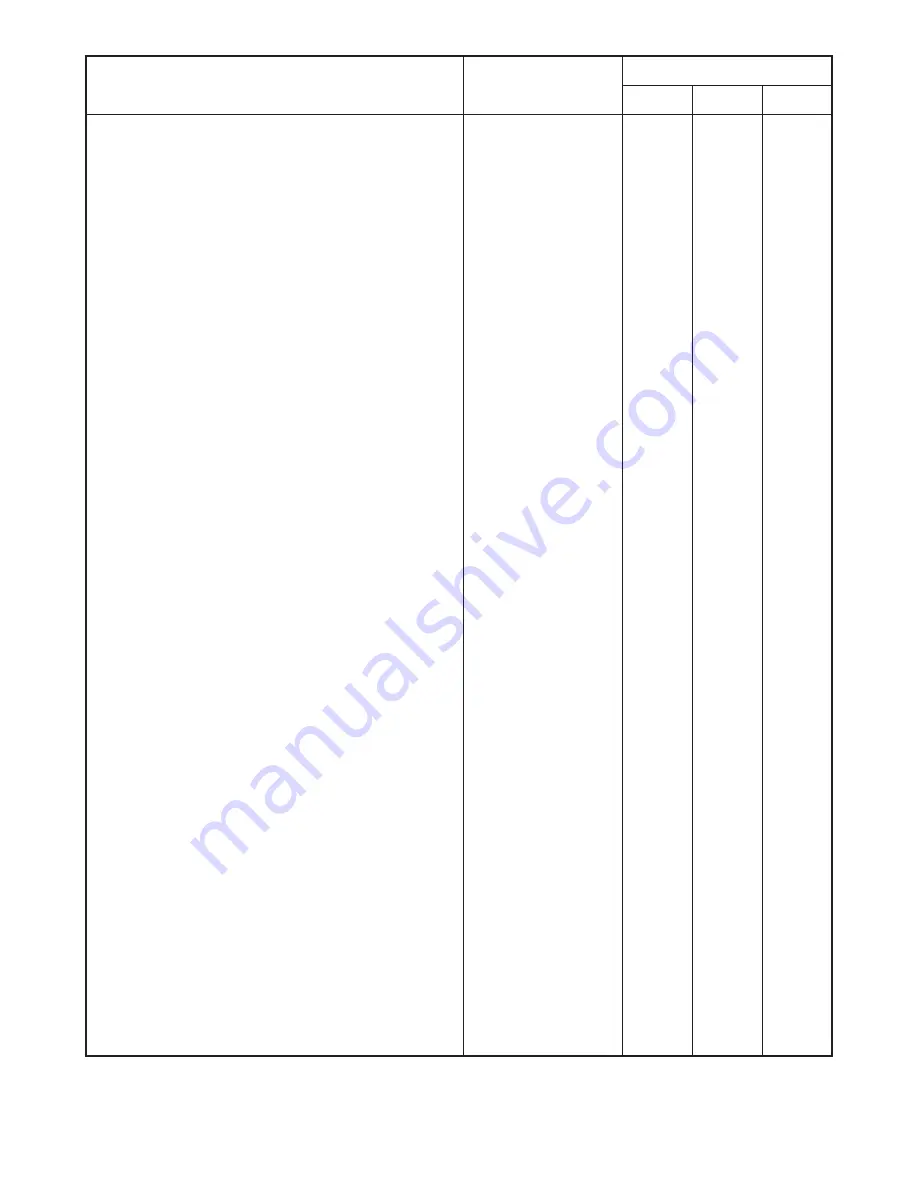
-27-
Rear wheel axle and nut
M20
x
1.5
125
12.5
90
Driven sprocket and wheel hub
M 8
x
1.25
50
5.0
36
Nipple (spoke)
-
3
0.3
2.2
Disc cover and rear brake caliper
M 6
x
1.0
7
0.7
5.1
Protector and rear brake caliper
M 6
x
1.0
7
0.7
5.1
Chain puller adjust bolt and locknut
M 8
x
1.25
16
1.6
11
Engine mounting:
Engine lower bracket and frame
M 8
x
1.25
34
3.4
24
Engine upper bracket and fram
M 8
x
1.25
34
3.4
24
Engine and engine bracket (front)
M10
x
1.25
69
6.9
50
Engine and engine bracket (upper)
M10
x
1.25
55
5.5
40
Engine and frame (lower)
M10
x
1.25
69
6.9
50
Engine guard (lower)
M 6
x
1.0
10
1.0
72
Engine guard (left/ right)
M 8
x
1.25
23
2.3
17
Pivot shaft and nut
M16
x
1.5
85
8.5
61
Relay arm and swingarm
M14
x
1.5
80
8.0
58
Relay arm and connecting rod
M14
x
1.5
80
8.0
58
Connecting rod and frame
M14
x
1.5
80
8.0
58
Rear shock absorber and frame
M10
x
1.25
56
5.6
40
Rear shock absorber and relay arm
M10
x
1.25
53
5.3
38
Rear frame and frame (upper)
M 8
x
1.25
32
3.2
23
Rear frame and frame (lower)
M 8
x
1.25
29
2.9
21
Swingarm and brake hose holder
M 5
x
0.8
1
0.1
0.7
Swingarm and patch
M 4
x
0.7
2
0.2
1.4
Drive chain tensioner mounting (upper)
M 8
x
1.25
19
1.9
13
Drive chain tensioner mounting (lower)
M 8
x
1.25
20
2.0
14
Chain support and swingarm
M 6
x
1.0
7
0.7
5.1
Seal guard and swingarm
M 5
x
0.8
6
0.6
4.3
Fuel tank mounting
M 6
x
1.0
10
1.0
7.2
Fuel tank and fuel cock
M 6
x
1.0
7
0.7
5.1
Fuel tank and seat set bracket
M 6
x
1.0
7
0.7
5.1
Fuel tank and hooking screw (fitting band)
M 6
x
1.0
7
0.7
5.1
Seat mounting
M 8
x
1.25
23
2.3
17
Side cover mounting
M 6
x
1.0
7
0.7
5.1
Front fender mounting
M 6
x
1.0
7
0.7
5.1
Rear fender mounting (front)
M 6
x
1.0
7
0.7
5.1
Rear fender mounting (rear)
M 6
x
1.0
10
1.0
7.2
Trip meter mounting
M 6
x
1.0
7
0.7
5.1
Meter cable holder
M 5
x
0.8
4
0.4
2.9
Headlight (left/ right)
M 6
x
1.0
10
1.0
7.2
Headlight (lower)
M 6
x
1.0
7
0.7
5.1
Taillight
M 6
x
1.0
4
0.4
2.9
Taillight lead clamp and rear fender
M 4
x
1.59
0.5
0.05
0.36
Coolant reservoir
M 6
x
1.0
7
0.7
5.1
Sidestand bracket
M10
x
1.25
66
6.6
48
Sidestand
M10
x
1.25
64
6.4
46
Item
Thread size
Tightening torque
Nm
m
d
kg
ft
d
lb