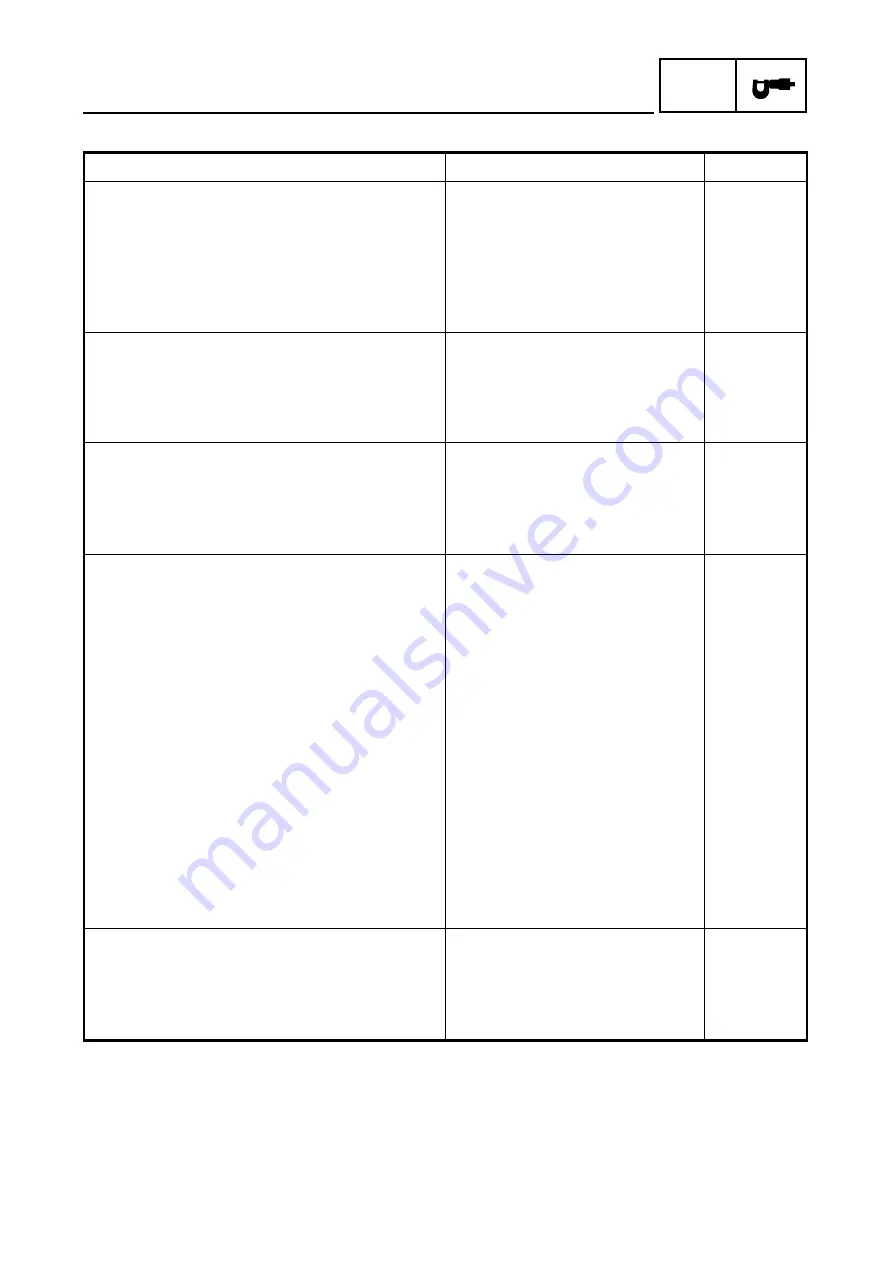
– 6 –
SPEC
ELECTRICAL
Item
Standard
Limit
C.D.I.:
Magneto model/manufacturer
F4T259/MITSUBISHI
----
Pickup coil resistance/color
189 ~ 231
Ω
at 20˚C (68˚F)/
White/Green – White/Red
----
Charging/rotor rotation direction detection
coil resistance/color
270 ~ 330
Ω
at 20˚C (68˚F)/
Red/White/Blue
----
C.D.I. unit model/manufacturer
F8T19871/MITSUBISHI
----
Charging system:
Type
A.C. magneto
----
Nominal output
14 V 16 A 5,000 r/min
----
Stator coil resistance/color
0.49 ~ 0.59
Ω
at 20˚C (68˚F)/
White – White
----
Rectifier/regulator:
Regulator type
Semi conductor-short circuit
----
Model/manufacturer
SH640E-11/SHINDENGEN
----
No load regulated voltage
14.1 ~ 14.9 V
----
Rectifier capacity
14 A
----
Electric starter system:
Type
Constant mesh type
----
Starter motor:
Model/manufacturer
SM-14/MITSUBA
----
Output
0.5 kW
----
Armature coil resistance
0.004 ~ 0.005
Ω
at 20˚C (68˚F)
----
Brush overall length
10 mm (0.4 in)
3.5 mm
(0.14 in)
Spring force
730 ~ 970 g (7.16 ~ 9.52 N)
----
Commutator diameter
28 mm (1.10 in)
27 mm
(1.06 in)
Mica undercut
0.7 mm (0.028 in)
----
Starter relay:
Model/manufacturer
MS5F-721/JIDECO
----
Amperage rating
180 A
----
Coil winding resistance/color
4.2 ~ 4.6
Ω
at 20˚C (68˚F)/
Blue/Black - Blue/White
----
Circuit breaker:
Type
Fuse
----
Amperage for individual circuit:
Main fuse
20 A
×
1
----
Reserve
20 A
×
1
----
MAINTENANCE SPECIFICATIONS