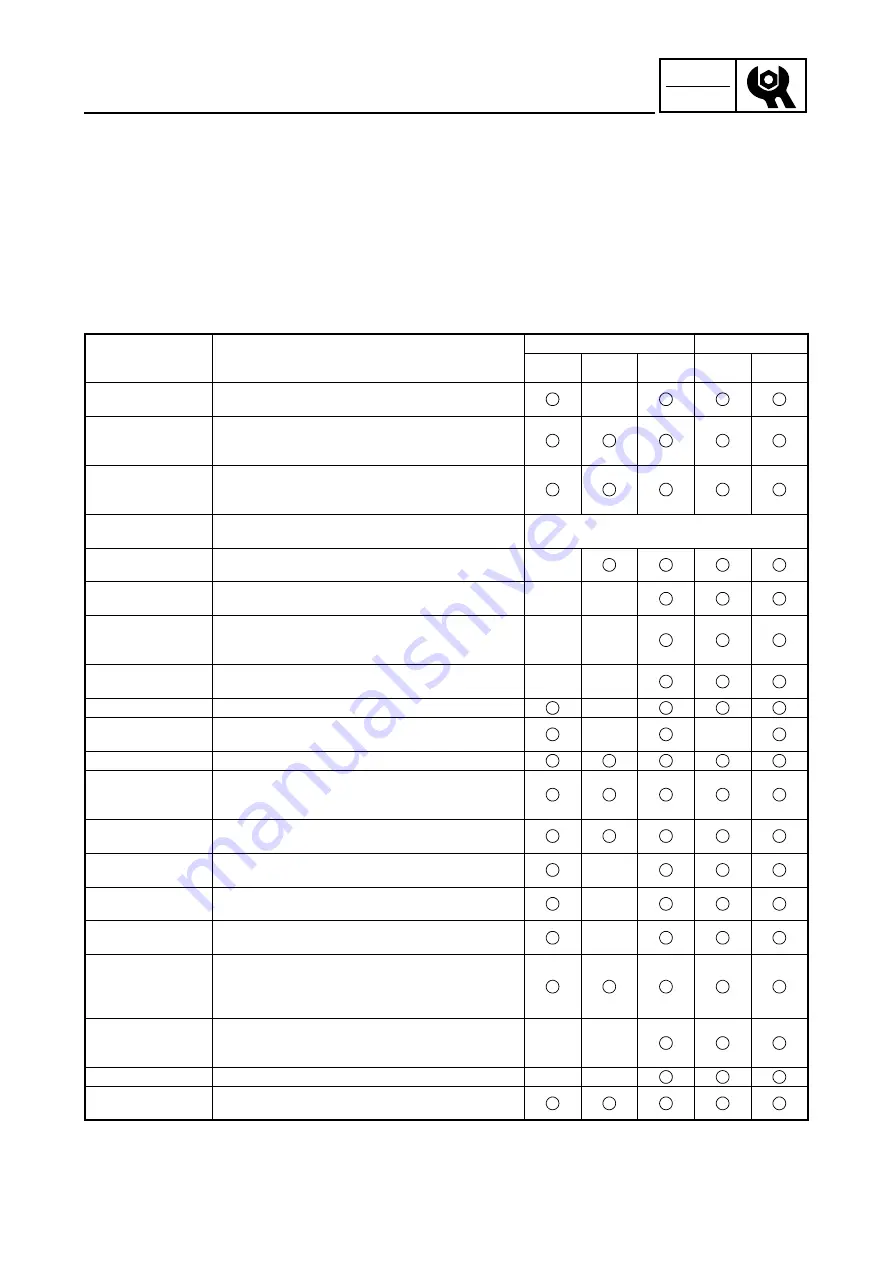
– 9 –
CHK
ADJ
INTRODUCTION/PERIODIC MAINTENANCE/
LUBRICATION INTERVALS
EB300000
PERIODIC CHECKS AND ADJUSTMENTS
INTRODUCTION
This chapter includes all information necessary to perform recommended inspections and adjust-
ments. These preventive maintenance procedures, if followed, will ensure more reliable vehicle
operation and a longer service life. The need for costly overhaul work will be greatly reduced. This
information applies to vehicles already in service as well as to new vehicles that are being prepared
for sale. All service technicians should be familiar with this entire chapter.
EB301000
PERIODIC MAINTENANCE/LUBRICATION INTERVALS
*
It is recommended that these items be serviced by a Yamaha dealer.
**
Lithium soap base grease
ITEM
ROUTINE
INITIAL
EVERY
1
month
3
months
6
months
6
months
1
year
Valves*
• Check valve clearance.
• Adjust if necessary.
Cooling system
• Check coolant leakage.
• Repair if necessary.
• Replace coolant every 24 months.
Spark plug
• Check condition.
• Adjust gap and clean.
• Replace if necessary.
Air filter element
• Clean.
• Replace if necessary.
Every 20 ~ 40 hours
(More often in wet or dusty areas.)
Carburetors*
• Check starter (choke) operation.
• Adjust engine idling speed and synchronization.
Crankcase breather
system*
• Check breather hose for cracks or damage.
• Replace if necessary.
Exhaust system*
• Check for leakage.
• Tighten if necessary.
• Replace gasket if necessary.
Fuel line*
• Check fuel hose for cracks or damage.
• Replace if necessary.
Engine oil
• Replace (Warm engine before draining).
Engine oil filter car-
tridge
• Replace if necessary.
Drive chain
• Check and adjust slack/alignment/clean/lube.
Front brake
• Check free play/operation/fluid leakage/See NOTE
Page 10.
• Correct if necessary.
Rear brake*
• Check operation/fluid leakage/See NOTE Page 10.
• Correct if necessary.
Clutch*
• Check operation.
• Adjust if necessary.
Wheels*
• Check balance/damage/runout.
• Replace if necessary.
Wheel bearings*
• Check bearing assembly for looseness/damage.
• Replace if damaged.
Steering system*
• Check operation.
• Repair if damaged.
• Check toe-in.
• Adjust if necessary.
Upper and lower arm
pivot and steering
shaft*
• Lubricate every 6 months.**
Rear arm pivot*
• Lubricate every 6 months.**
Fittings and fasten-
ers*
• Check all chassis fittings and fasteners.
• Correct if necessary.
Summary of Contents for YFM660RP 5LP2-AE2 2002
Page 1: ...YFM660R P SUPPLEMENTARY SERVICEMANUAL 5LP2 AE2 2002 ...
Page 2: ......
Page 8: ......
Page 32: ......