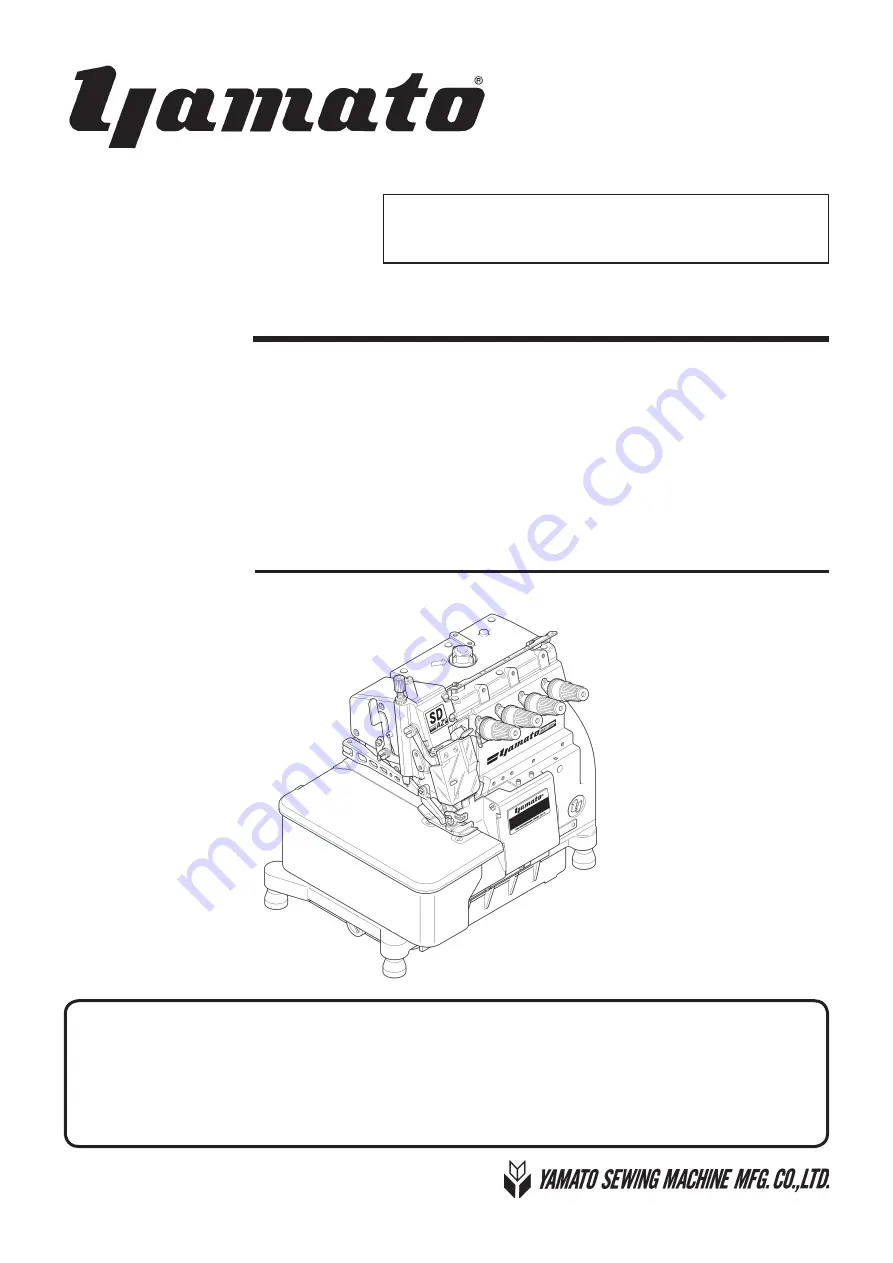
Instruction Manual
SUPPER HIGH SPEED OVERLOCK MACHINE
SUPPER HIGH SPEED SAFETY STITCH MACHINE
AZ7000SDR-8
class
AZ7000SDR-8,AZ7003SDR-8,AZ7016SDR-8
AZ7020SDR-8,AZ7025SDR-8,AZ7120SDR-8,AZ7125SDR-8
AZ7500SDR-8
class
AZ7500SDR-8,AZ7520SDR-8,AZ7525SDR-8
AZ7500SDR-31,AZ7520SDR-31,AZR7525SDR-31
Thank you for purchasing the AZ7000SDR-8 and AZ7500SDR-8 class. Before using your
AZ7000SDR-8 and AZ7500SDR-8 class, please read the instruction manual and understand
the contents well.
After reading the instruction manual, please keep it in a location where it is easily accessible
to the operator.