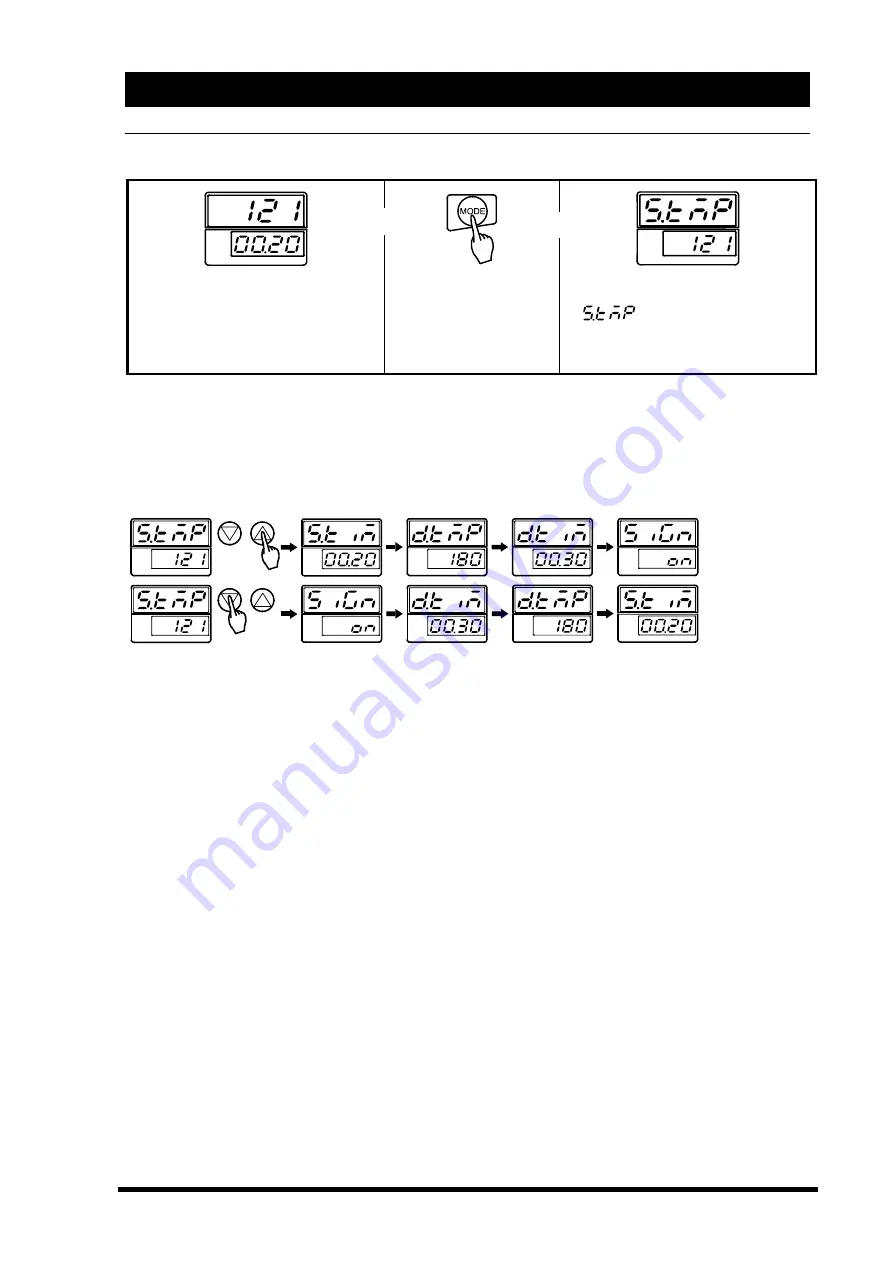
22
Program “MODE”
“MODE” key Information
How to use the “MODE” key
Turn the circuit breaker on.
The sterilizer automatically starts in
stand-by mode, and the display
show current set point.
Push the “MODE”
key.
→
Main display starts blinking
(Sterilization Temp.)
Setting other parameters
・
Turn the circuit breaker on.
・
Push the “MODE” key.
・
Use the
▽△
keys to select desired parameter.
Î
Î