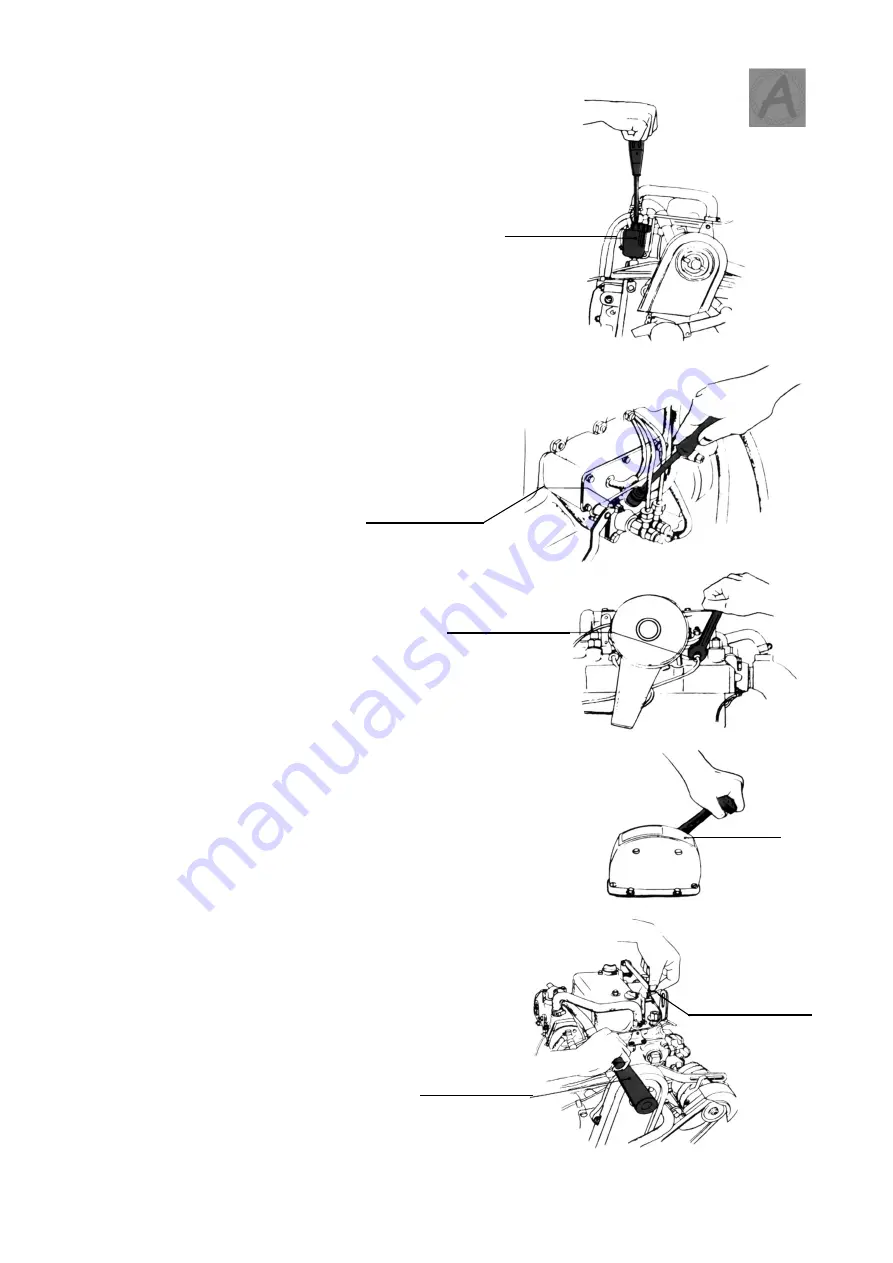
AIR VENTING
1)
Open the fuel cock.
2)
Loosen the air venting plug on the fuel
strainer.
After bubbles stop coming out with the
fuel, tighten again.
3)
Loosen both the fuel joint on the side of
the fuel strainer and the air venting plug
on the fuel injection pump.
And after bubbles stop coming out with
the fuel, tighten the latter plug and then
tighten former.
4)
Remove the nipple on the side of the
injection valve.
5)
Set the speed control lever to
the FULL position.
6)
Disengage the decompression lever and
turn the starting handle about 20 - 30 times
until air in the high pressure line is expelled.
7)
Tighten the nipple on the side of the
injection valve, turn the starting handle
until the sound of fuel injection from the
fuel injection valve is heard.
By this procedure, air can be completely
vented from the fuel line.
VII
14.
Fuel oil strainer
Fuel injection pump
Fuel injection valve
Full
Decompression lever
Starting handle