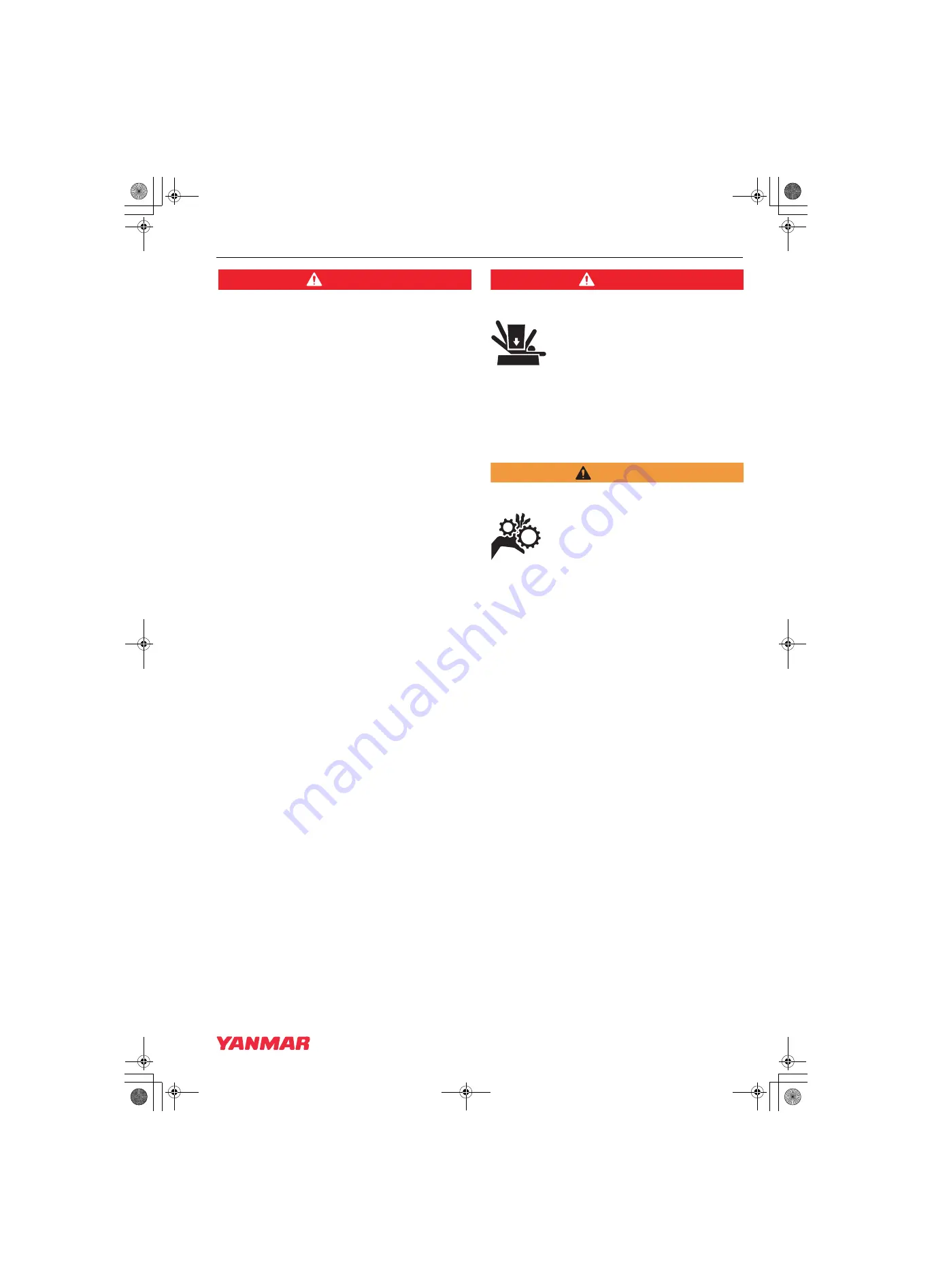
SAFETY
3TNV88F Service Manual
3-5
Safety Precautions
DANGER
(Continued)
• Be sure to place the diesel fuel container on
the ground when transferring the diesel fuel
from the pump to the container. Hold the hose
nozzle firmly against the side of the container
while filling it. This prevents static electricity
buildup which could cause sparks and ignite
fuel vapors.
• Never place diesel fuel or other flammable
material such as oil, hay or dried grass close
to the engine during engine operation or
shortly after shutdown.
• Before you operate the engine, check for fuel
leaks. Replace rubberized fuel hoses every
two years or every 2000 hours of engine
operation, whichever comes first, even if the
engine has been out of service. Rubberized
fuel lines tend to dry out and become brittle
after two years or 2000 hours of engine
operation, whichever comes first.
• Never remove the fuel cap with the engine
running.
• Never use diesel fuel as a cleaning agent.
• Place an approved container under the air
bleed port when you prime the fuel system.
Never use a shop rag to catch the fuel. Wipe
up any spills immediately. Always close the
air bleed port after you complete priming the
system.
• Wear eye protection. The fuel system is under
pressure and fuel could spray out when you
open the air bleed port.
• If the unit has an electric fuel pump, turn the
key switch to the ON position for 10 to 15
seconds, or until the fuel coming out of the air
bleed port is free of bubbles, to allow the
electric fuel pump to prime the system.
• If the unit has a mechanical fuel pump,
operate the fuel priming pump several times
until the fuel coming out of the air bleed port
is free of bubbles.
• Failure to comply will result in death or
serious injury.
DANGER
Crush Hazard!
• When you need to transport an
engine for repair, have a helper
assist you to attach it to a hoist
and load it on a truck.
• Never stand under a hoisted engine. If the
hoist mechanism fails, the engine will fall on
you, causing death or serious injury.
• Failure to comply will result in death or
serious injury.
WARNING
Sever Hazard!
• Keep hands and other body parts
away from moving/rotating parts
such as the cooling fan, flywheel
or PTO shaft.
• Wear tight-fitting clothing and keep your hair
short or tie it back while the engine is
running.
• Remove all jewelry before you operate or
service the machine.
• Never start the engine in gear. Sudden
movement of the engine and/or machine
could cause death or serious personal injury.
• Never operate the engine without the guards
in place.
• Before you start the engine make sure that all
bystanders are clear of the area.
• Keep children and pets away while the engine
is operating.
• Check before starting the engine that any
tools or shop rags used during maintenance
have been removed from the area.
• Failure to comply could result in death or
serious injury.
3TNV88F_SVM_A4.book 5 ページ 2012年7月26日 木曜日 午後6時4分