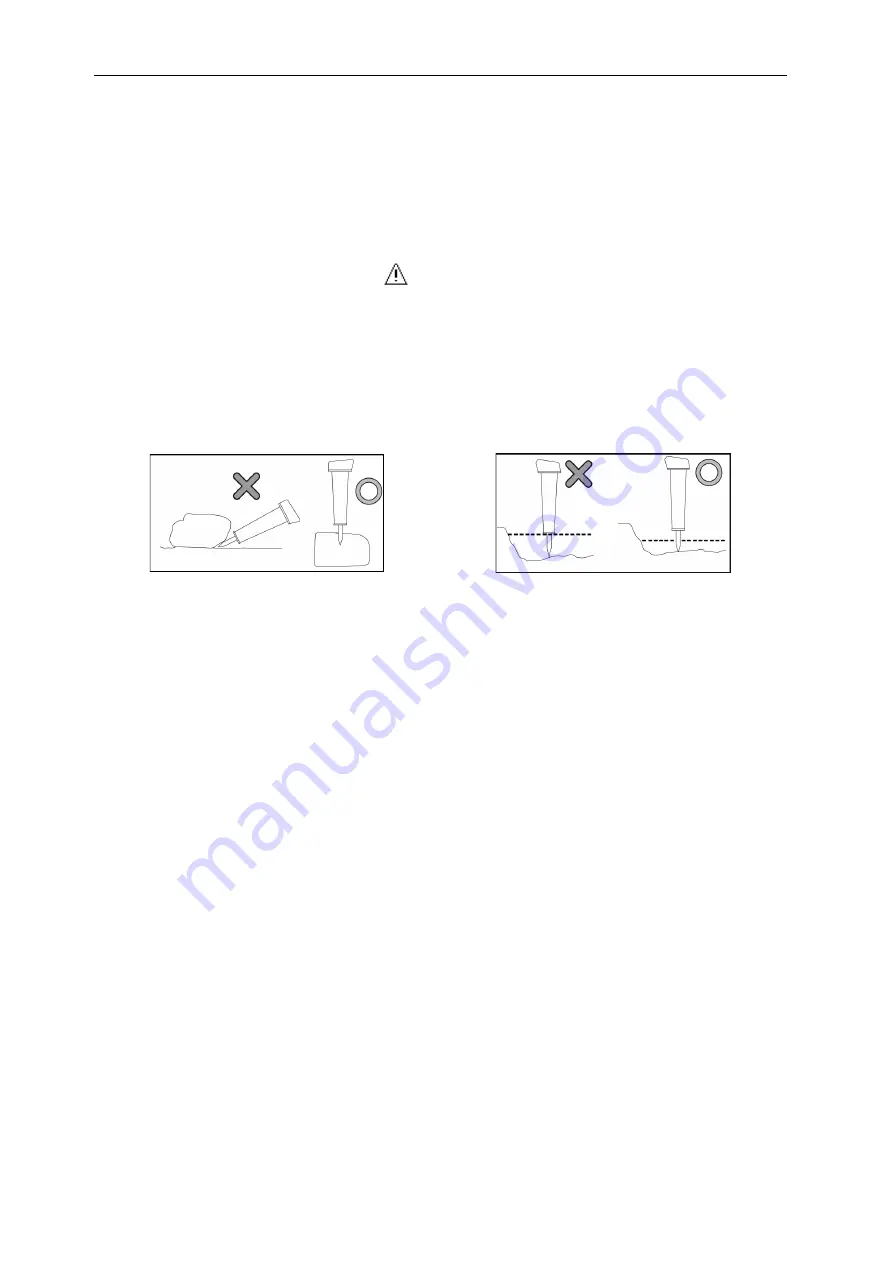
11 H
ANDLING OF ACCESSORIES
11.1 Hydraulic hammer SOCOMEC
Usage recommendations
WARNING
During the work phase, keep everyone out of the 20m danger zone.
IMPORTANT
•
The hammer must be at 90° to the working surface.
•
In a submerged area, make sure that the water does not reach the body of the hammer.
Note
The hammer can only operate within the following temperature range:
[-5°C ~ +45°C]
•
To avoid damaging the structure of the hammer and minimize vibration, the operator must be
smooth when using the tool.Be sure to set the engine speed if you are using a hammer.
•
Once the work requiring the hammer is finished, set the hammer vertically with respect to the
ground and leave it in this position to facilitate drainage of condensation on the side of the
piston.
Tool change
IMPORTANT
•
Do the following operations with gloves and safety shoes.
•
Always use oils and greases recommended by YANMAR.
1. Park the machine preferably on a stable, flat and level surface.
2. Place the accessory at about 30 cm above the ground in horizontal position.
3. Stop the engine.
4. To remove the tool from the housing:
105
Summary of Contents for SV26
Page 3: ......
Page 5: ......
Page 7: ......
Page 9: ......
Page 17: ......
Page 19: ...2 ...
Page 24: ...3 Warning labels 7 3 1 Location of the warning adhesive labels ...
Page 25: ...3 Warning labels 8 ...
Page 75: ...58 ...
Page 115: ...9 Rubber tracks 98 9 6 Track replacement 6 4 2 Track replacement page 149 ...
Page 145: ...128 ...
Page 175: ...158 ...
Page 179: ...162 ...
Page 181: ...164 ...
Page 187: ...170 ...
Page 200: ...C Notes 183 ...
Page 204: ...MINI EXCAVATOR http www yanmar eu ...
Page 205: ...MINI EXCAVATOR SV26 USER OPERATION AND MAINTENANCE MANUAL ...