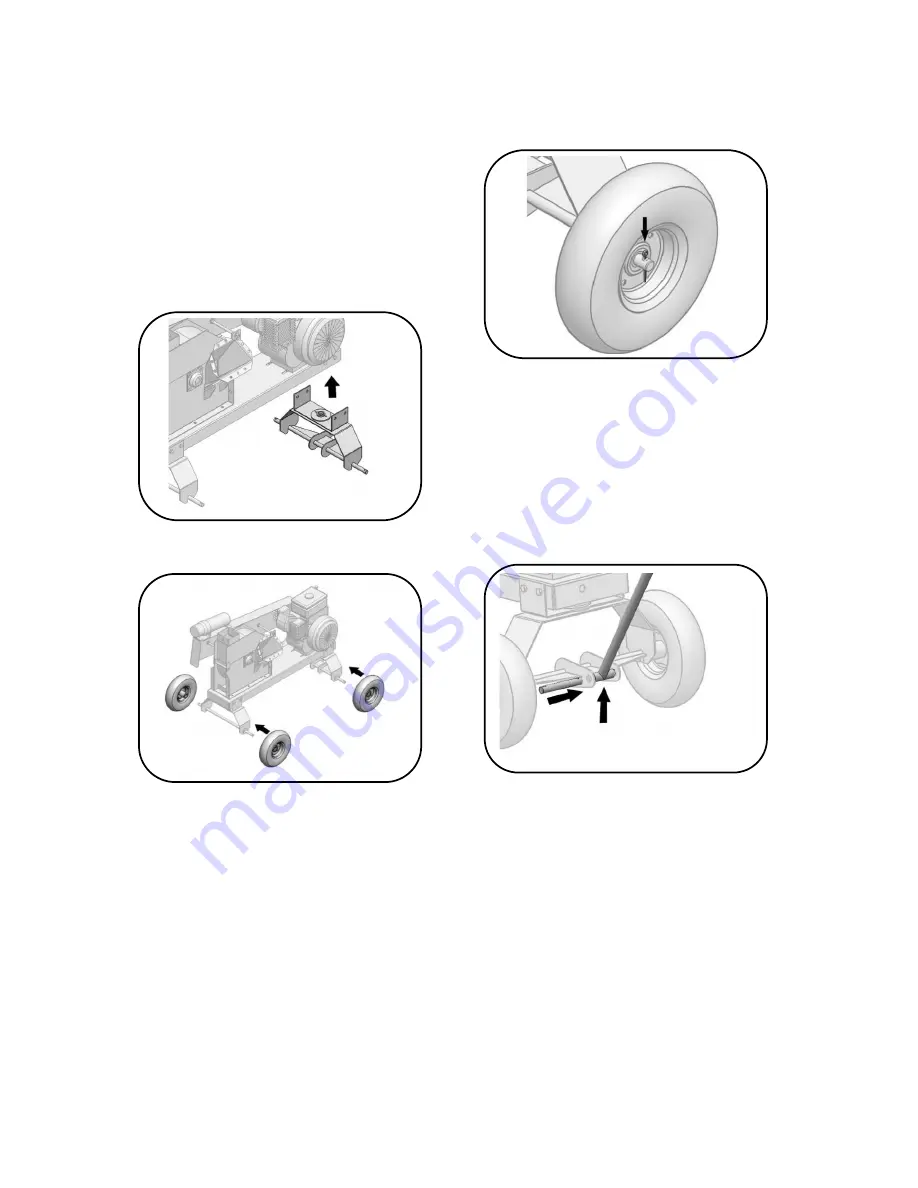
9
-Inserting rotating axle and boltit as shown in
Figure below.
a. 4 Hex Bolts 3/8 "x 1"
b. 4 Hex Nuts 3/8 "
c. 4 Pressure Washers 3/8 "
d. Plain Washers 4 3/8 "
-Insert tires in their respective shafts
-Place safety pin across each shaft with
pliers and warp them to prevent loosen of
your tires in operation, as shown in Fig.
4- 5/8” Washers
4 Cotter Pins 3/16 "x 1"
Pull Assembly
-Next figure shows the assembly of the pull
bar..
-Secure in place using safety cotter pins and
deforming to prevent slipping of the pin.
Nuts and Bolts: 1/8 "x 1" cotter pins (2 units)
Feed Hopper Assembly
-Assemble the hopper as shown in Fig.
Nuts and bolts:
a. 9-Hex Bolts ¼ "x 1"
b. 9-Pressure Washers ¼ "
c. 9-Plain Washers ¼ "
d. 9-Hex nuts ¼ "
Summary of Contents for YB2510
Page 23: ...23 NOTES...