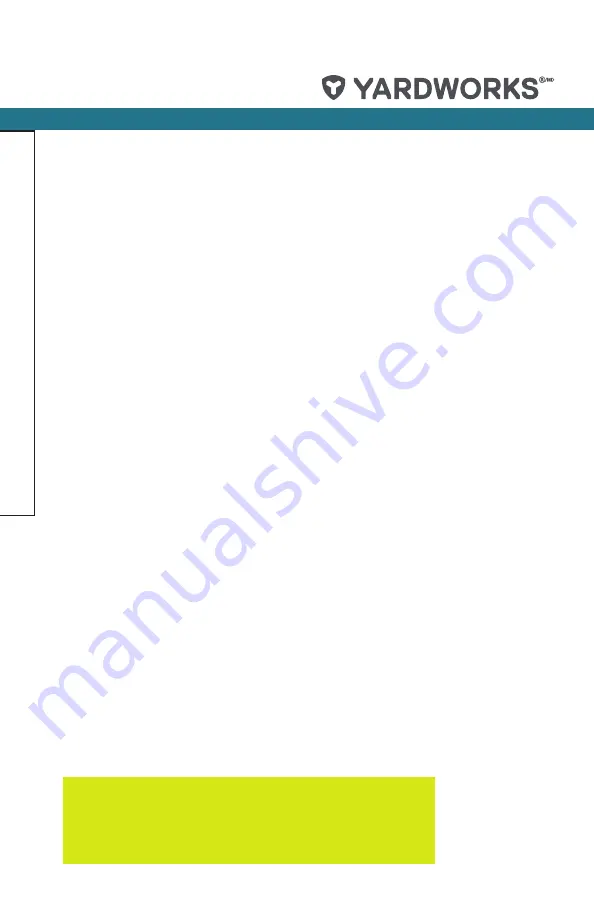
model no.
060-1300-6
| contact us: 1.866.523.5218
40
TI
ll
ING
T
IP
s
AND
Te
CHNI
q
U
es
CleARING THe TINes
The tines have a self-clearing action which eliminates most tangling of debris in the tines.
However, occasionally dry grass, stringy stalks or tough vines may become tangled. Follow
these procedures to help avoid tangling and to clean the tines, if necessary.
–
To reduce tangling, set the depth regulator deep enough to get maximum “chopping”
action as the tines chop the material against the ground. Also, try to till under crop
residues or cover crops while they are green, moist and tender.
–
While power composting, try swaying the handlebars from side to side about 6 to
12" (15 to 30 cm). This “fishtailing” action often clears the tines of debris.
–
If tangling occurs, lift the tines out of the soil and run the tiller in reverse (if unit is
equipped with powered reverse) for a few feet. This reversing action should unwind a
good deal of debris.
–
It may be necessary to remove the debris by hand (a pocket knife will help you to cut
away the material). Be sure to stop the engine and disconnect the spark plug wire
before clearing the tines by hand.
WARNING: Before clearing the tines by hand, stop the engine, allow
all moving parts to stop and disconnect the spark plug wire.
Remove the ignition key on electric start models.
Failure to follow this warning could result in personal injury.
Summary of Contents for 060-1300-6
Page 63: ...model no 060 1300 6 contact us 1 866 523 5218 63 PAGE INTENTIONALLY LEFT BLANK...
Page 65: ...model no 060 1300 6 contact us 1 866 523 5218 65 EXPLODED VIEW PRODUCT...
Page 66: ...model no 060 1300 6 contact us 1 866 523 5218 66 EXPLODED VIEW PRODUCT...
Page 67: ...model no 060 1300 6 contact us 1 866 523 5218 67 EXPLODED VIEW PRODUCT...
Page 73: ...model no 060 1300 6 contact us 1 866 523 5218 73 PAGE INTENTIONALLY LEFT BLANK...