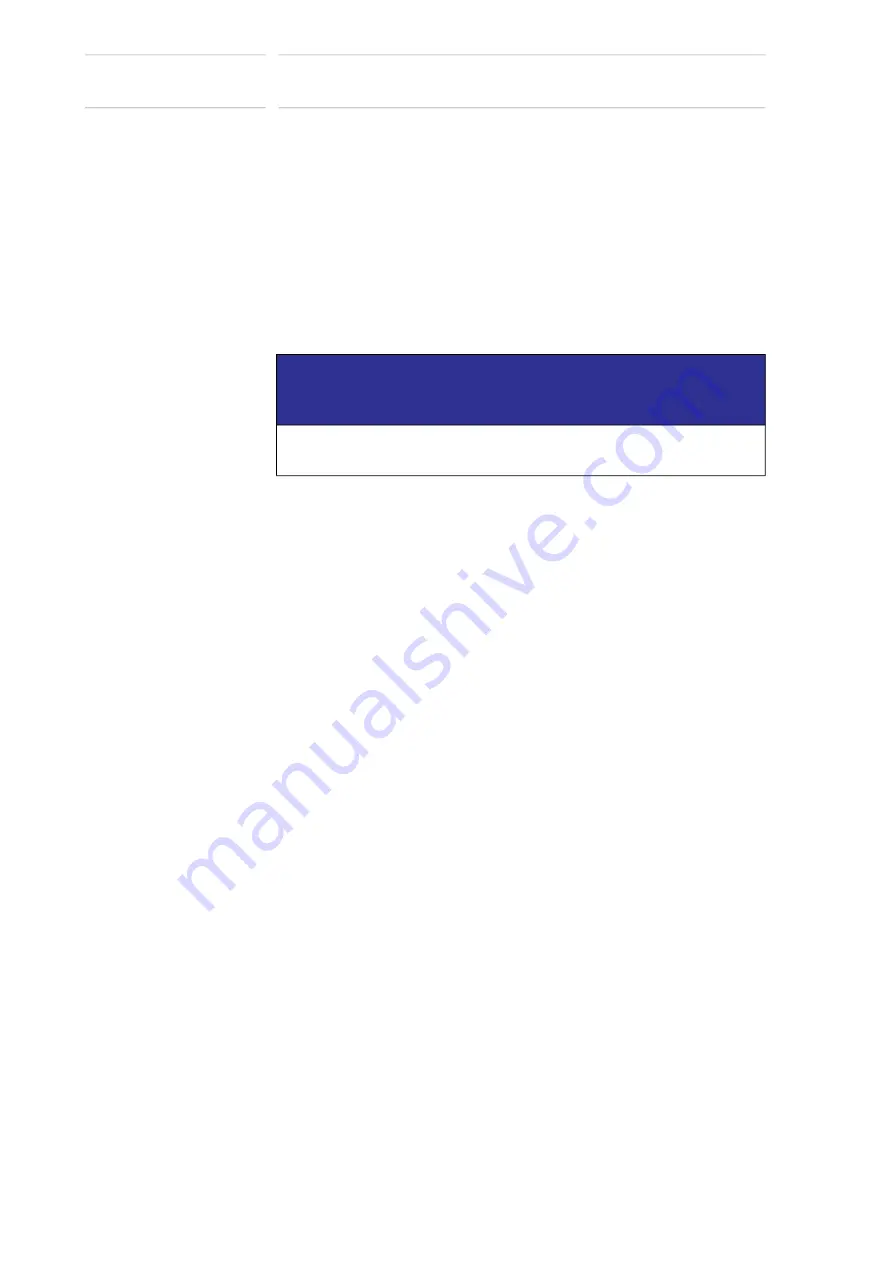
2-5
183574-1CD
183574-1CD
2
Equipment Description
2.3 Operator Station
ArcWorld 50/50S/52/52S
2.3.2 Operator Station — EMERGENCY STOP
Pressing the Operator Station’s EMERGENCY STOP button initiates an
E-STOP condition. Refer to
for information on the E-STOP
condition and the procedures for recovering from it.
2.3.3 Operator Station — POSITIONER AUTO/MANUAL
The POSITIONER AUTO/MANUAL selector switch is used to select
automatic or manual mode for the Positioner. When the selector switch is
in the AUTO position, the Robot welds parts immediately after the barrier
door closes. In MANUAL mode, the Positioner rotates, but the Robot does
not weld parts - this mode is useful to verify that the door operation is
occurring properly.
NOTICE
The POSITIONER AUTO/MANUAL command depends upon the
structure of the Control Master job.
60 of 126