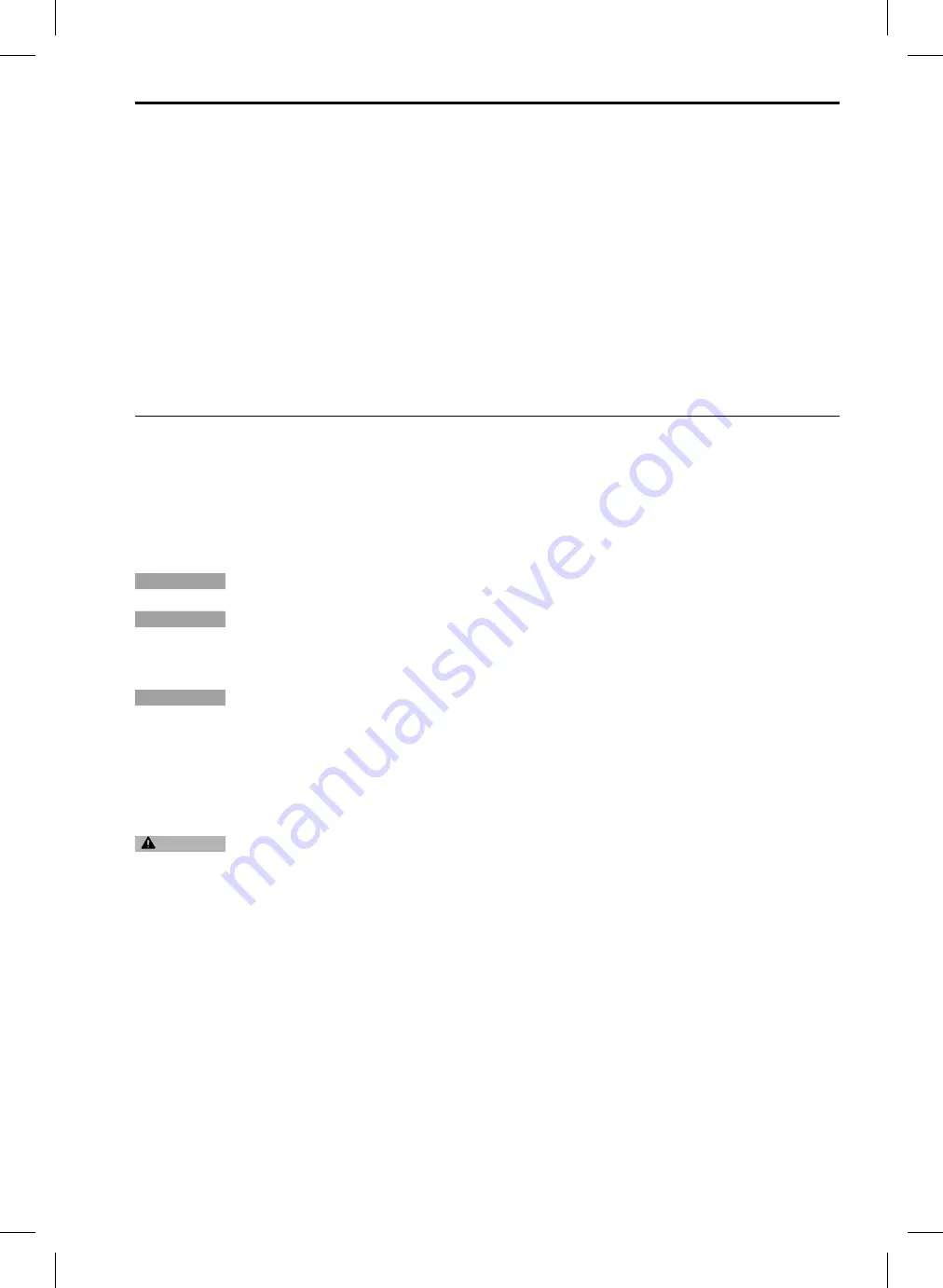
2 Mechanical & Electrical Installation
YASKAWA ELECTRIC
SIEP C710617 19A YASKAWA AC Drive CR700 Technical Manual
107
If a device does not have protection against high frequencies, high frequency leakage currents can cause the
device to malfunction. If you have a malfunction on a device that is not protected, decrease the carrier frequency
of the drive, switch to a better breaker, or use an ELCB with a minimum cumulative sensitivity amperage of 200
mA for each drive.
These conditions can have an effect on leakage current:
•
Drive capacity
•
Carrier Frequency
•
Wiring distance and types of motor cables
•
EMI/RFI filter
To prevent damage and injury to personnel and drives, use a high-frequency ELCB that is rated for AC and DC
power supplies.
Note:
Yaskawa recommends these ELCBs, which are designed to operate with high frequencies.
•
Mitsubishi Electric Corporation; NV series
•
Schneider Electric; NS series
◆
Dynamic Braking Option, Motor Protection
■
Install an Electromagnetic Contactor (MC) at Input Side of Drive
When the protective functions of the drive have been triggered, or when an emergency stop has occurred, and
according to the sequence, the main circuit power supply is to be shut off, an MC can be used instead of a molded-
case circuit breaker (MCCB). However, caution should be observed, since if an MC on the input side of the drive
(primary side) is used to forcefully stop the drive, regenerative braking will not operate, and a coast to stop will
occur.
NOTICE
Do not connect electromagnetic switches or MCs to the output motor circuits without correct sequencing.
Incorrect sequencing of output motor circuits could cause damage to the drive.
NOTICE
Turn the drive ON (Run) and OFF (Stop) a maximum of one time each 30 minutes with the MC on the power
source side to extend the service life of the relay contacts and electrolytic capacitors in the drive. Run and Stop the motor as
much as possible with the drive. The drive can fail if users frequently turn the drive ON and OFF with the MC on the power
source side to Run and Stop the drive. Incorrect operation can decrease the service life of the relay contacts and electrolytic
capacitors.
NOTICE
Use an MC to make sure that you can fully remove power to the drive when necessary. Wire the MC to open
when a fault output terminal is triggered.
Note:
When it is necessary to prevent machinery from restarting after recovery from a momentary power loss that occurred during run, an MC
can be installed at the input side of the drive, and a sequence that does not automatically enable the Run command after recovery of
power should be configured.
Protect the Braking Resistor/Braking Resistor Unit
Use an MC on the input side (primary side) to prevent damage to the braking resistor/braking resistor unit.
WARNING
Fire Hazard. When you use a braking unit, use a thermal relay on the braking resistors and set a fault contact
output for the braking resistor unit to disconnect drive main power through an input contactor.
Incorrect braking circuit
protection can overheat the resistors and cause death or serious injury by fire.
■
Install a Thermal Overload Relay on the Drive Output
A thermal overload relay disconnects the power line to the motor during a motor overload condition to prevent
damage to the motor.
Install a thermal overload relay between the drive and motor in these conditions:
•
When operating more than one motor from one drive.
•
When operating the motor directly from the power line with a power line bypass.
When operating one motor from one drive, it is not necessary to install a thermal overload relay. The drive has
electronic motor overload protection in the drive software.
Note:
•
When you install a thermal overload relay, set parameter
L1-01 = 0 [Motor Overload (oL1) Protection = Disabled]
.
•
Set up a sequence that will trip an external fault (coast to stop) for the contacts of the thermal overload relay.